Integrating a collaborative robot (cobot) can be a big step for many companies. Yet, in today's manufacturing industry, it is almost insurmountable to strive for increased efficiency, productivity and safety. Not only to stay ahead of the competition, but also given digital developments and the shift to Industry 4.0. In this blog, we provide a roadmap to ensure that the implementation of a cobot goes as smoothly as possible.
Step 1: Assess current business processes
Before integrating a cobot, it is crucial to conduct a thorough evaluation of current business processes. Identify the tasks that are repetitive, dangerous or labor-intensive, as they are best suited for automation with cobots. Analyze where the most inefficiencies occur and where a cobot can make the most difference.
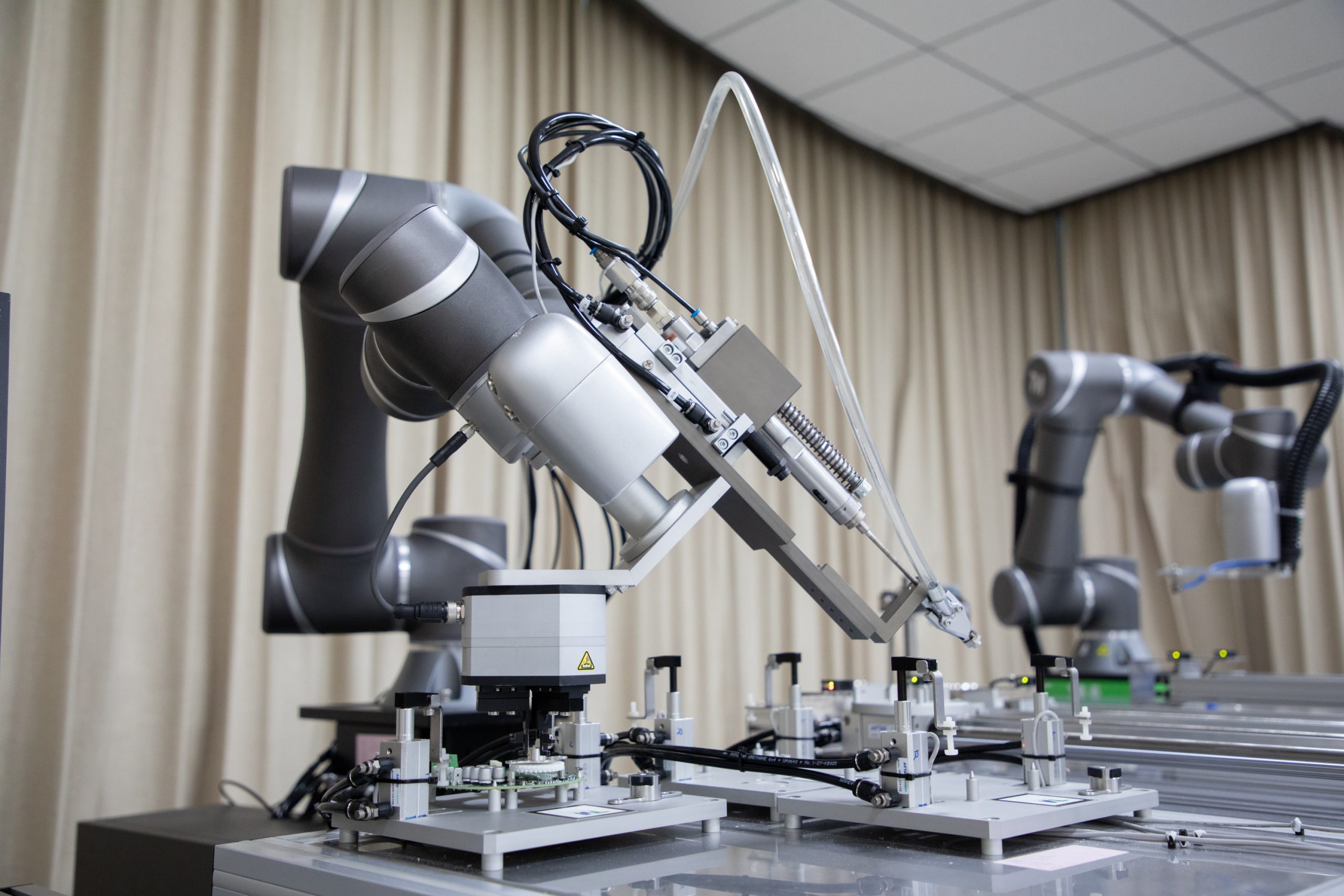
Tips:
- Conduct a time and motion study to identify bottlenecks.
- Involve employees in the evaluation to gain valuable insights.
Step 2: Set goals and KPIs
Define clear goals and key performance indicators (KPIs) for integrating a cobot. Whether it's to increase production, improve quality, reduce lead time or increase safety, having measurable goals helps assess success.
Tips:
- Formulate SMART goals (Specific, Measurable, Acceptable, Realistic, Time-bound).
- Consider both quantitative and qualitative goals.
Step 3: Choose the right cobot
Choosing the right cobot is a crucial step. Cobots vary in size, power, precision and functionality. Make sure the chosen cobot is suitable for the specific tasks you want to automate.
Tips:
- Consult a specialist or work with an experienced integrator.
- Consider compatibility with existing systems and future expandability.
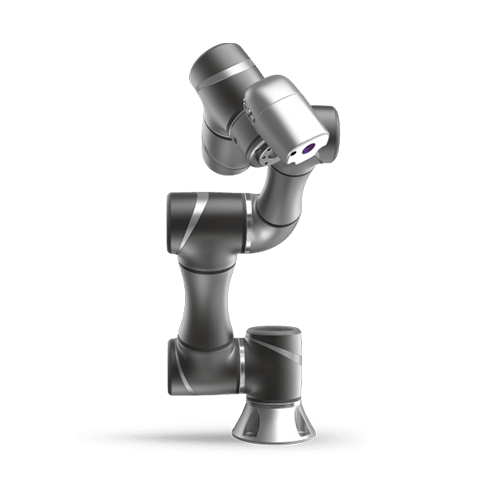
Step 4: Write a detailed implementation plan
A detailed implementation plan helps coordinate all parties involved and ensures that the integration goes smoothly. The plan should include the following aspects, among others:
- Timeline: Establish a realistic timeline for each phase of the integration.
- Roles and responsibilities: Define who is responsible for what tasks.
- Risk analysis: Identify potential risks.
Tips:
- Schedule regular meetings to discuss progress.
- Provide sufficient buffer in the schedule for unexpected problems.
Step 5: Run a simulation
A detailed simulation can help test the integration of cobots into business processes. In addition, it can reveal potential problems without actually disrupting production.
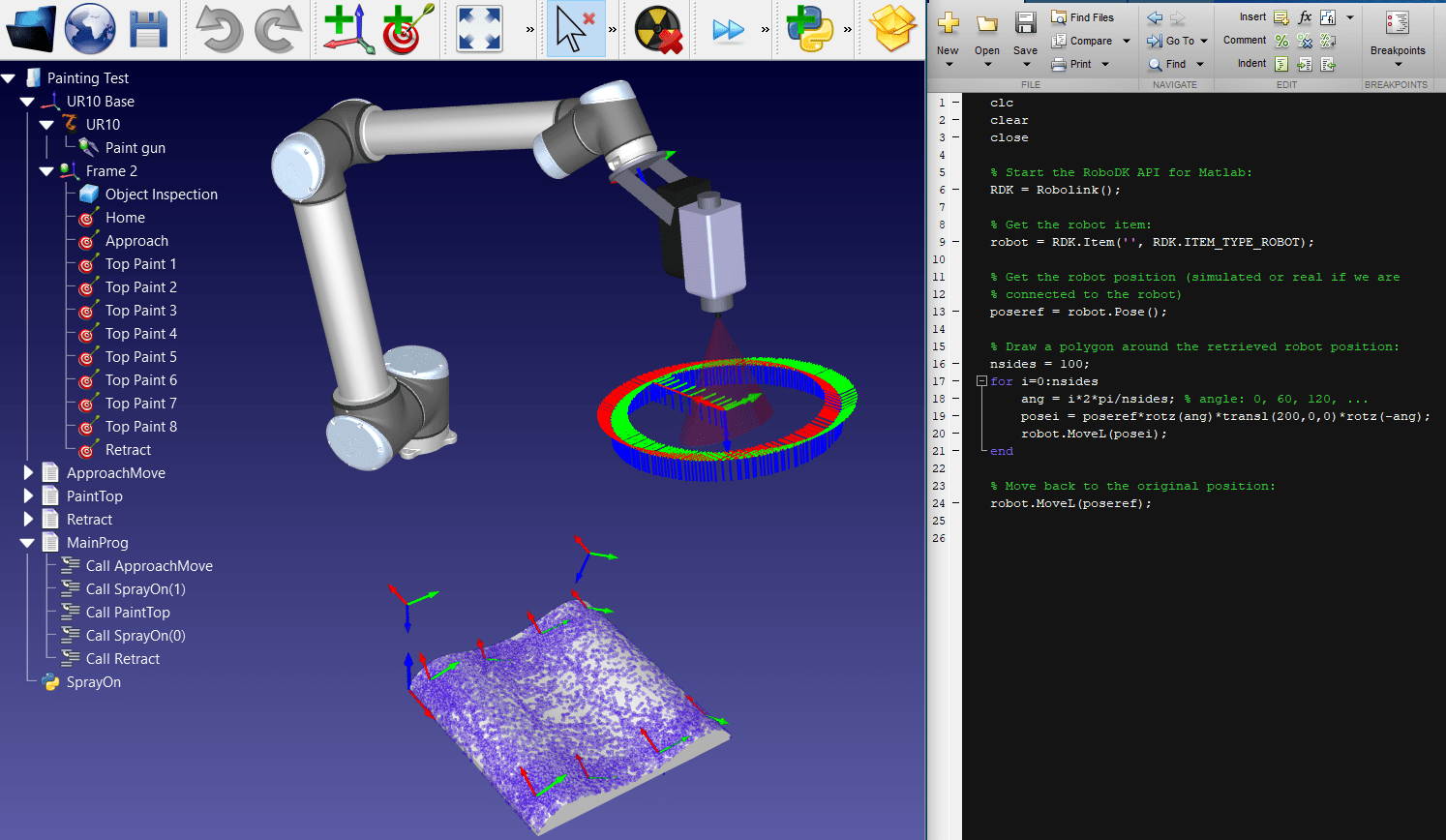
Tips:
- Use specialized software to create realistic simulations of your production process.
- Involve different departments to ensure a broad view of possible scenarios and challenges.
- Thoroughly analyze the simulation results and adjust the implementation plan if necessary.
- Document all findings and learning points so they can be applied during actual integration.
Step 6: Perform actual integration
After a successful simulation, it is time to actually integrate the cobots into your production process. Make sure that all preparatory steps have been completed and that all parties involved are ready for implementation.
Tips:
- Follow the implementation plan closely to ensure a smooth integration.
- Provide adequate support during the initial phase of integration.
- Test the cobot thoroughly in the actual production environment to ensure proper operation.
Step 7: Train your employees
Employees must be well prepared for the arrival of the cobots. Training is essential to ensure they understand how to work safely and effectively with the cobots.
Tips:
- Offer both theoretical and practical training.
- Organize training sessions with small groups for personal attention.
- Provide ongoing education and in-service training.
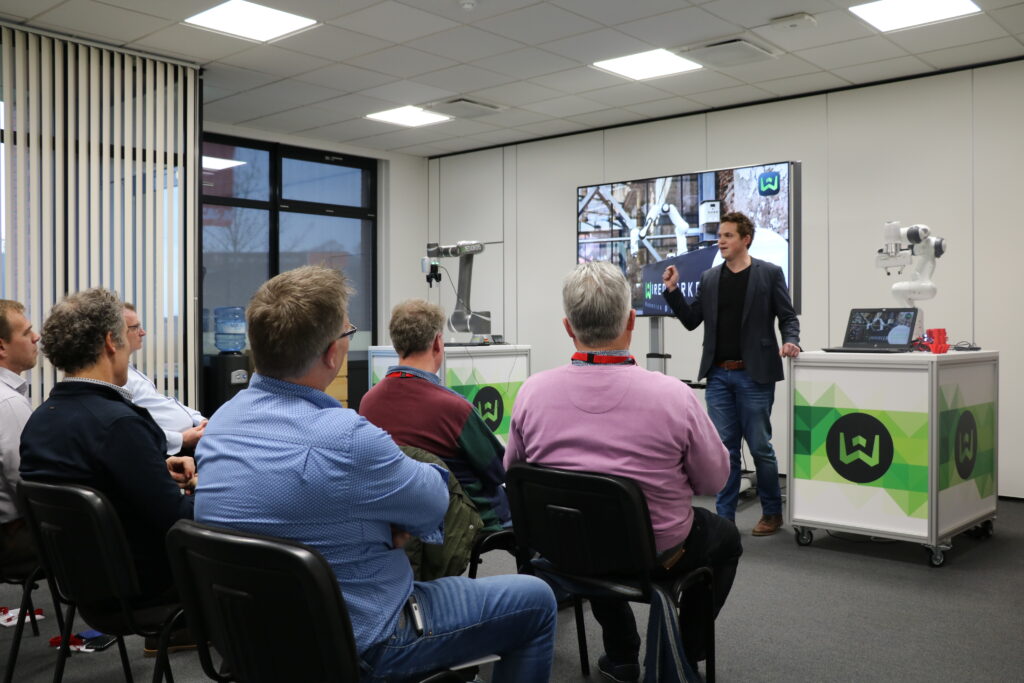
Step 8: Monitor and maintenance
The work does not end after the initial integration. It is important to continuously monitor the performance of the cobots and perform regular maintenance to ensure optimal operation.
Tips:
- Establish a schedule for preventive maintenance.
- Use monitoring tools to track performance in real time.
- Be proactive in addressing any problems.
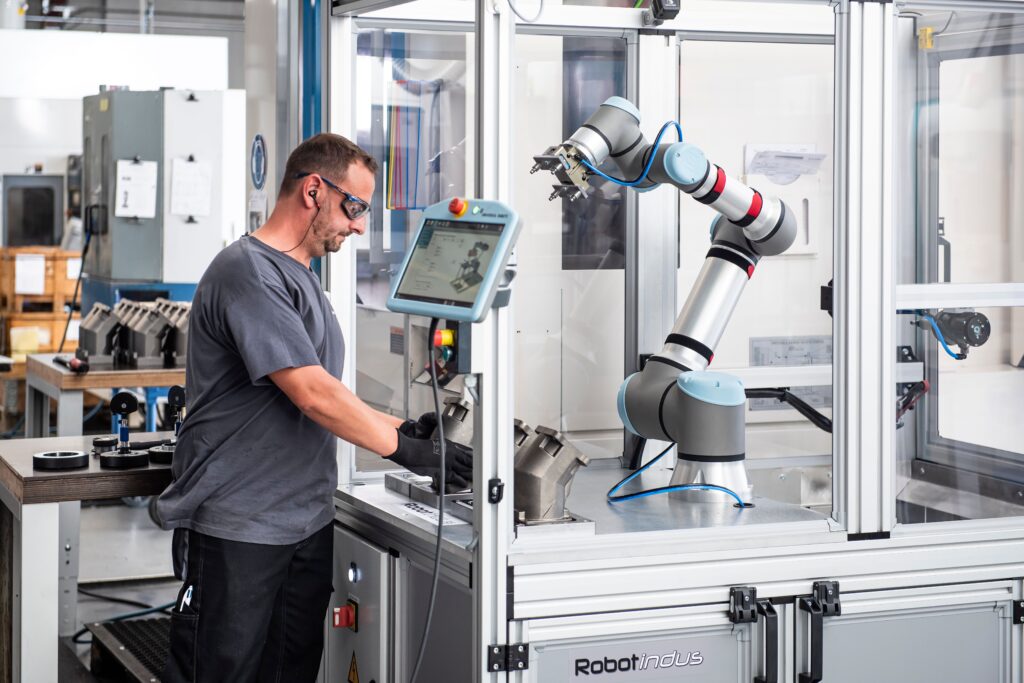
Step 9: Evaluate and improve
Regular evaluation of cobot integration helps identify further areas for improvement. Use KPIs and employee feedback to assess the effectiveness of the cobots and adjust as needed.
Tips:
- Schedule periodic review sessions.
- Be open to adjustments and improvements.
Step 10: Keep innovating
The world of robotics and automation is constantly evolving. Stay on top of the latest developments and innovations to ensure that your business always stays ahead.
Tips:
- Attend trade shows and conferences.
- Invest in research and development.
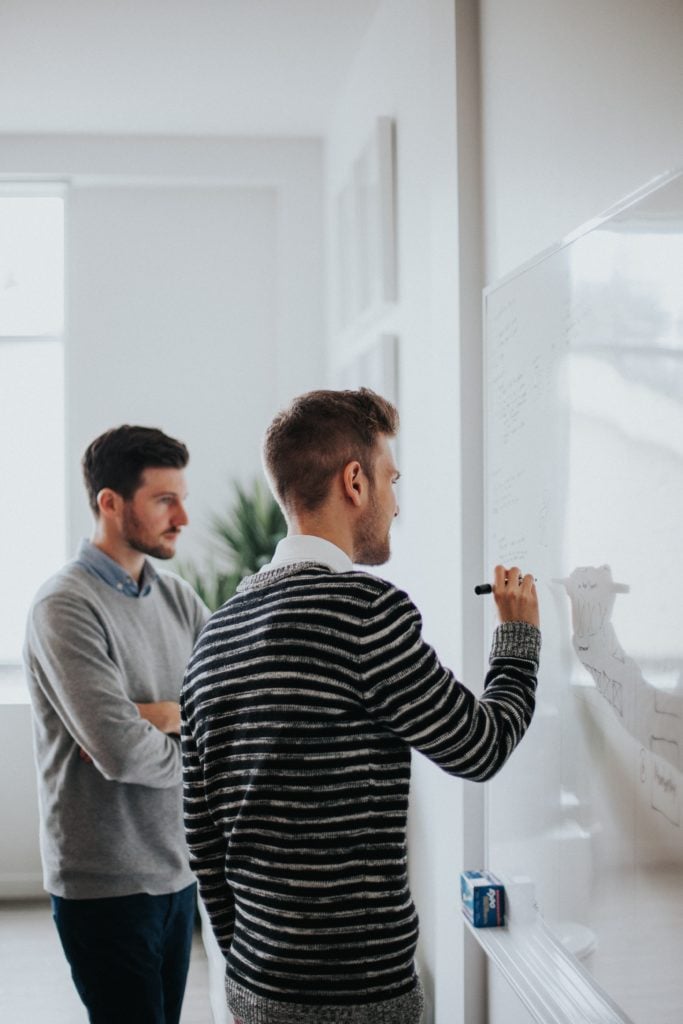
Conclusion
The successful integration of cobots into your business processes can yield significant benefits, from increased productivity to improved safety. By taking a structured approach, from initial implementation to continuous improvement, you can ensure that implementation runs smoothly and maximizes returns. With proper planning and execution, cobots can be a valuable addition to your business, helping you remain competitive and innovative in a rapidly changing marketplace.
We, WiredWorkers, have helped countless companies get the most out of their production. Contact us today or schedule a no-obligation online consultation!
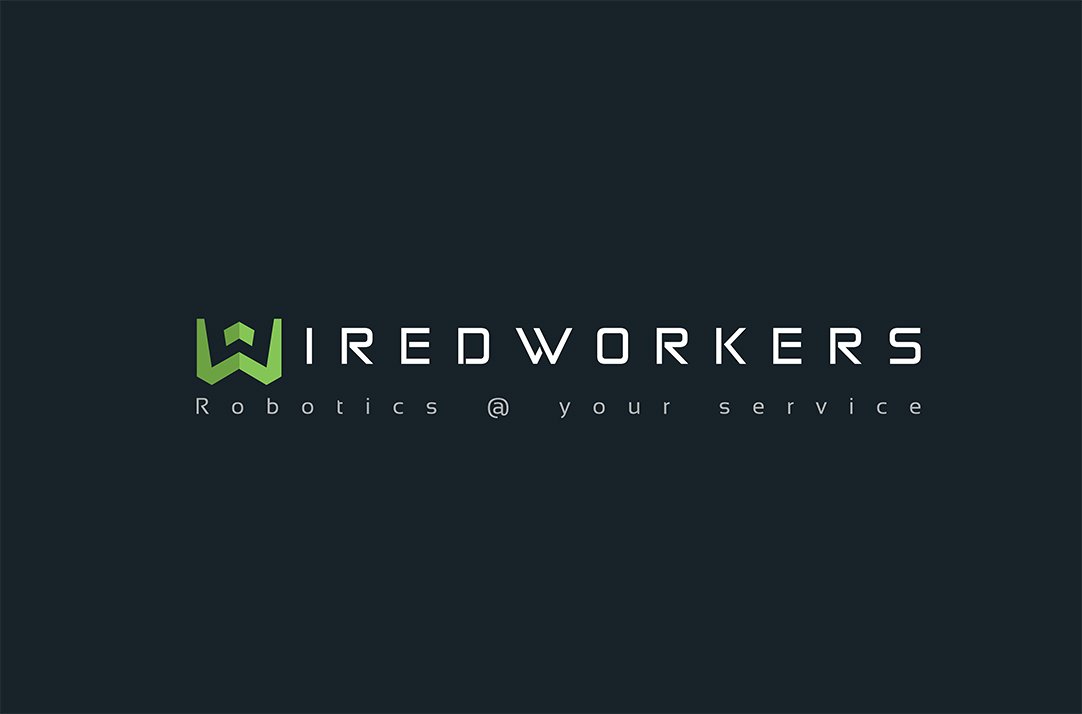