These are turbulent times for many companies in the manufacturing sector. With rising prices and a global labor shortage, it is essential for companies to look at how to stay competitive and continue to grow. Especially within the welding sector, this is the order of the day. Technology can help with this. Applications such as cobot welding offer the opportunity to scale up operations while saving costs. Therefore, in this blog, 6 benefits of welding with a cobot!
What is cobot welding?
Welding with a cobot a quick and easy to automate application. A welding torch is connected to the end of the robot, which then moves along the desired path and accurately deposits welds. A robot will always move at the desired speed at 0.1 mm accuracy, time after time. This ensures consistent quality. In addition, a collaborative robot offers several other advantages over a traditional robotic cell. The purchase cost is usually lower, they are quick to install, with simple basic training it is easy to program them yourself, and they can be converted to a new welding task at lightning speed. Cobots can perform a variety of welding tasks, including arc, TIG, laser, MIG, ultrasonic, plasma and spot welding.
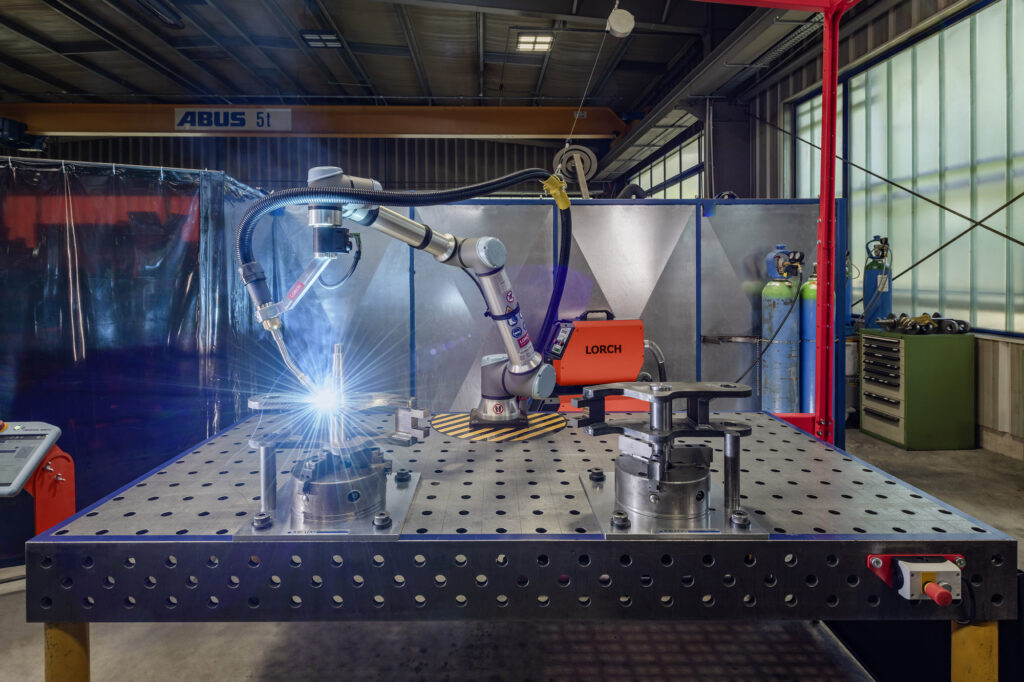
The benefits of cobot welding
A unique feature of a cobot is its flexibility and relative ease of use compared to other industrial robot applications. With the right software solutions, end-effectors and application kits, a robot can be quickly deployed for a wide range of welding tasks. Once operational, a cobot provides the following benefits.
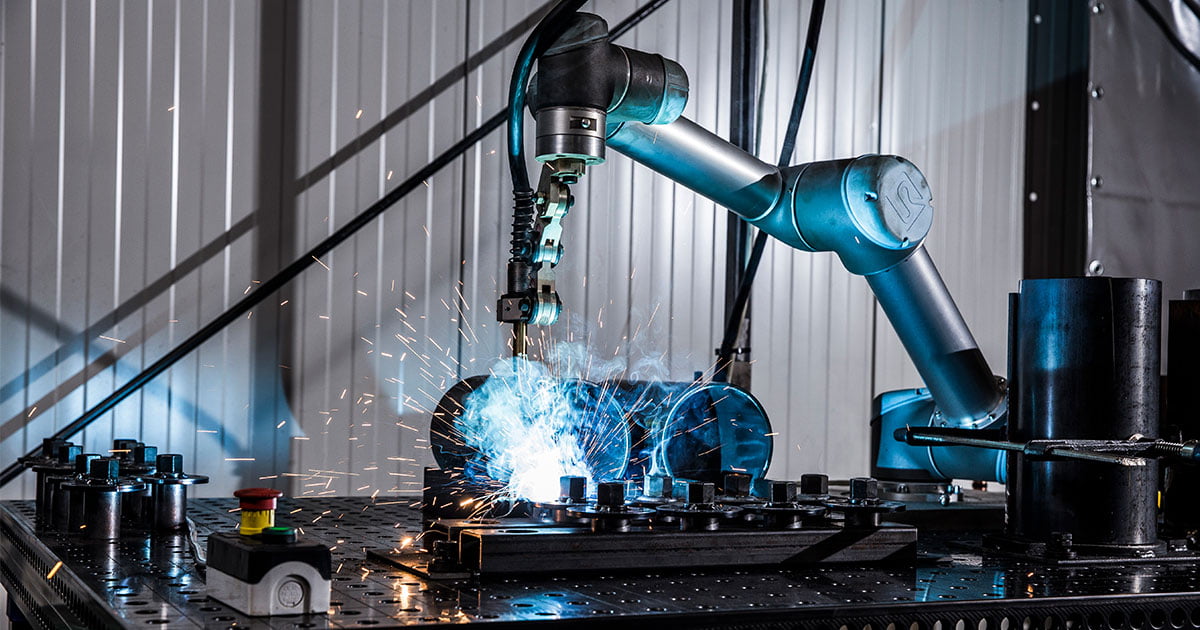
Solving labor shortages
Finding qualified personnel is one of the biggest challenges facing welding companies. In doing so, there is no prospect that this will be solved in a short period of time. Companies that choose to automate the welding process can not only maintain their productivity, but also increase it without having to hire additional staff. In addition, it can also provide an added incentive for current staff to learn about advanced technology and thus be able to do more varied work, which can result in less turnover in the workforce.
Less waste
Although experienced welders can work with surprising accuracy, they still occasionally make mistakes. That means that occasionally products or parts have to be thrown away, and that costs money. With an automated process, errors are minimized and that means less throwing away.
Consistent precision
Cobots can work to the nearest tenth of a millimeter. In a repetitive task such as welding, this means that the robot will always perform the task identically, no matter how many times and for how long. No matter how experienced and skilled an employee is, they will never be able to work as accurately as a robot.
More productive
A collaborative robot needs no breaks and can basically work 24 hours a day. This makes it the perfect tool for scaling up production processes and taking on new customers or for meeting (seasonal) peaks in production demand.
Cost reduction
As production capacity increases, without increasing personnel costs, it becomes possible to produce more cheaply. The ROI of a collaborative robot is usually less than a year, given its low acquisition cost. So after a year, the cobot makes money and the cost per product can be reduced. A great way to maintain a strong position in a competitive market.
Increased safety
Cobot applications can contribute to a safer work environment. Not only do workers no longer have to perform tedious, dirty and potentially dangerous tasks, but the cobot itself has a range of built-in safety features.
Getting started!
In short; automating welding tasks with a cobot is the way to ensure a consistent level of quality. In addition to an improvement in quality, productivity also goes up. Workers who previously performed welding tasks have their hands free to perform other tasks, such as quality inspection or finishing finished products. In addition, unlike industrial robots, cobots are easier to operate and current employees can start working with the robot themselves after a short training session.
WiredWorkers is an expert in the field of automation and has already helped several companies implement welding robots. Contact us or schedule a free cobot consultation!
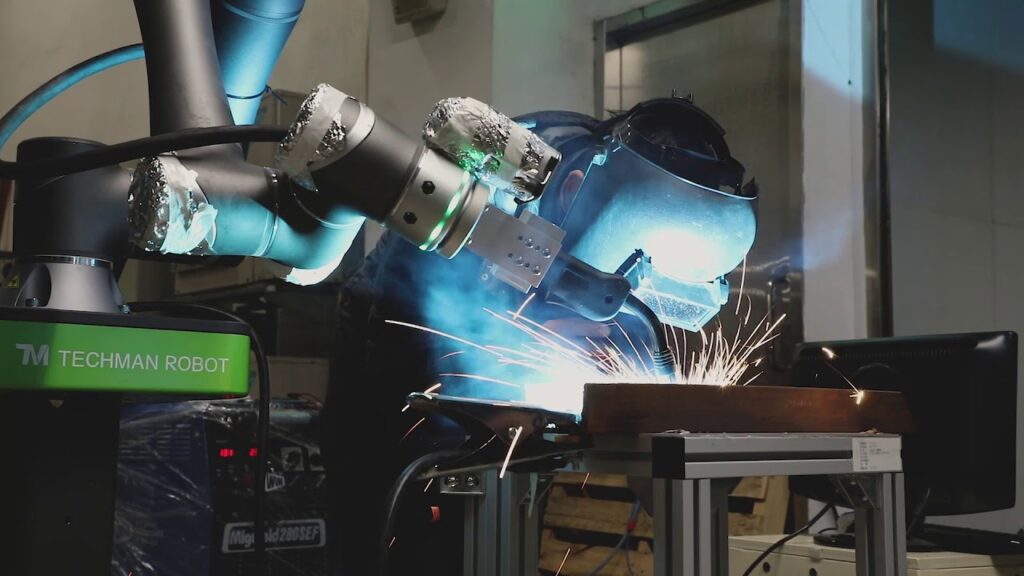