Why production employees benefit from an attractive working environment
Google the word 'production employee' and dozens of pages of vacancies appear where conditions such as 'high concentration and accuracy' and 'hard worker' are used repeatedly. Clearly there is a great demand for capable production workers, but how do you keep them involved in the production process and above all, how do you keep them concentrated and accurate for 40 hours a week?
Driven, passionate employees.
Motivated and committed employees are the driving force behind every organisation. Besides the fact that a motivated employee delivers more work, they will also proactively think along with the organization, solve problems faster and are more innovative. When optimizing a production process, a logical first step is to motivate and connect employees. You can do this by setting personal goals, regularly evaluating, relinquishing responsibility, radiating trust and expressing your appreciation. But an important factor that is often not considered is an attractive working environment.
What is an attractive working environment?
A room with a good temperature, sufficient natural light and decent sanitary facilities may sound like an attractive working environment, but that is not quite what we mean. In our view, an attractive working environment is a place where diversity and flexibility are important pillars. It is precisely these two pillars that are difficult to realise in a production process. Because let's be honest, flexibility and diversity are not the first thing you think of when it comes to packaging, assembly and conveyor work. How do you ensure that the employees of these departments also experience diversity and flexibility in their work?
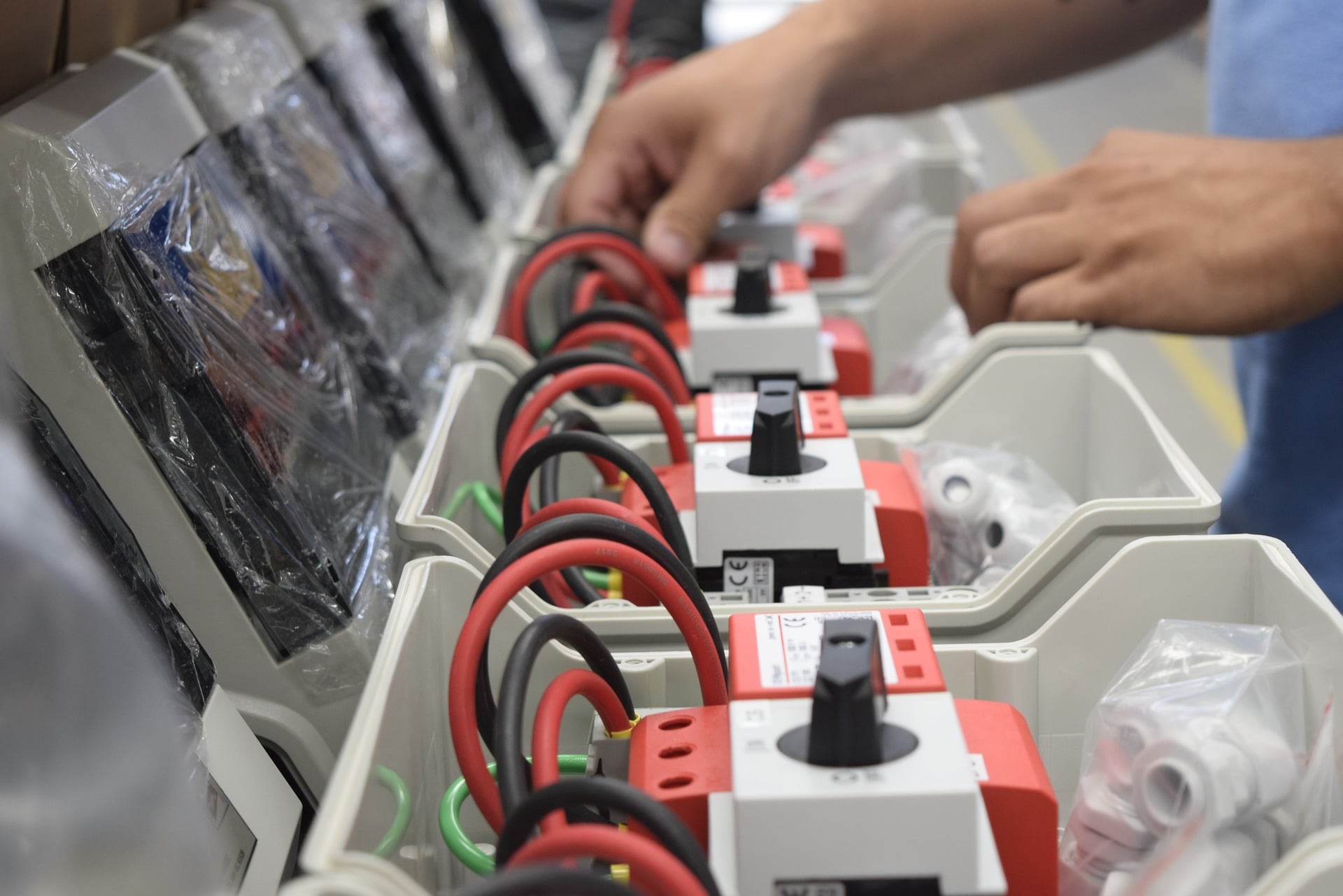
The solution.
As said, one way to involve employees is by giving them responsibility. If an employee only has to pack parcels in a box or place semi-finished products in a machine all day long, an employee will not feel responsible. One way to take this work off the hands of an employee is to use a collaborative robot, or cobot. Cobots can perform tasks that people describe as 'mind-numbing', 'monotonous' or 'boring'. Moreover, monotonous repetitive actions are often the cause of complaints such as RSI (repetitive strain injury).
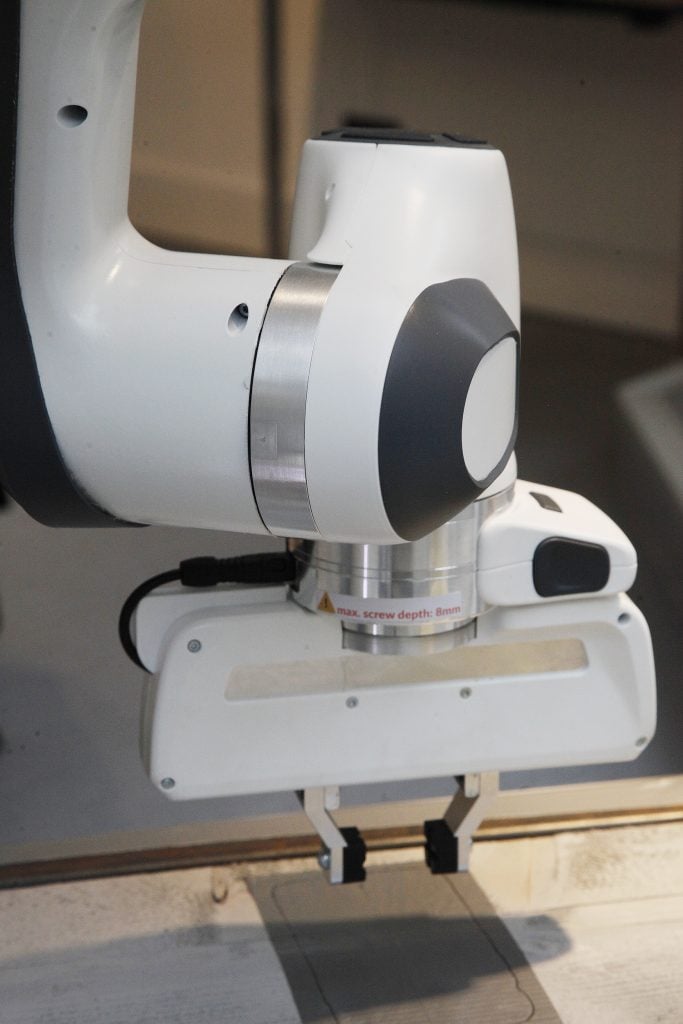
Cobot?
What is the difference with a normal robot? A cobot is specially designed to work with people. They react to touch and it is easy to stop them without too much force. This ensures that they do not have to stand behind large safety screens and there is a minimal risk of accidents. In addition, they are small in size, flexible and programmable for various activities. For example, a robot could perform the same operation for 40 hours a week, but could also be deployed in a different department every day.
The use of a cobot.
This means for employees that they can concentrate on more complex tasks such as inspection, which increases the diversity of their work. In addition, a cobot can contribute to the increase of the production capacity. Imagine that an employee in the assembly department has to screw on a product. The cobot can take on this task, leaving the employee's hands free to further assemble a product.
Do you remember those companies that are looking for production employees, with a high concentration, high accuracy and who can also work tirelessly hard? Doesn't it sound like they are looking for a cobot? Of course robots can't take all the work out of human hands and employees are always needed to make a production process as smooth as possible. Cobots can ensure that people remain satisfied and involved in the same production process. WiredWorkers is happy to help find the right balance and find ways to streamline a production department. Contact us for more information or request a free cobot consultation.