Plastic welding with is a revolutionary technology that is changing the plastics industry. Plastic welding, the fusing together of plastic parts, is a task that can be perfectly performed by cobots. In this blog, we will discuss seven key advantages of plastic welding with cobots.
What is plastic welding?
Simply put, plastic welding is the joining of two plastic objects into one. Using a special welding device, two plastic parts are heated to the point where the material becomes mobile and plastic. As a result, the molecules of the plastic join together, and when they cool, they are fused into one whole. In this way, plastic parts can be joined without using glue or other fasteners. Perfect for situations where glue, for example, does not provide sufficient strength, such as for roof finishes or flooring.
As with normal welding torches, plastic welding equipment can also be attached to the end of a cobot. The cobot moves the end along the desired path to accurately lay down welds. Below are 6 advantages of plastic welding with cobots.
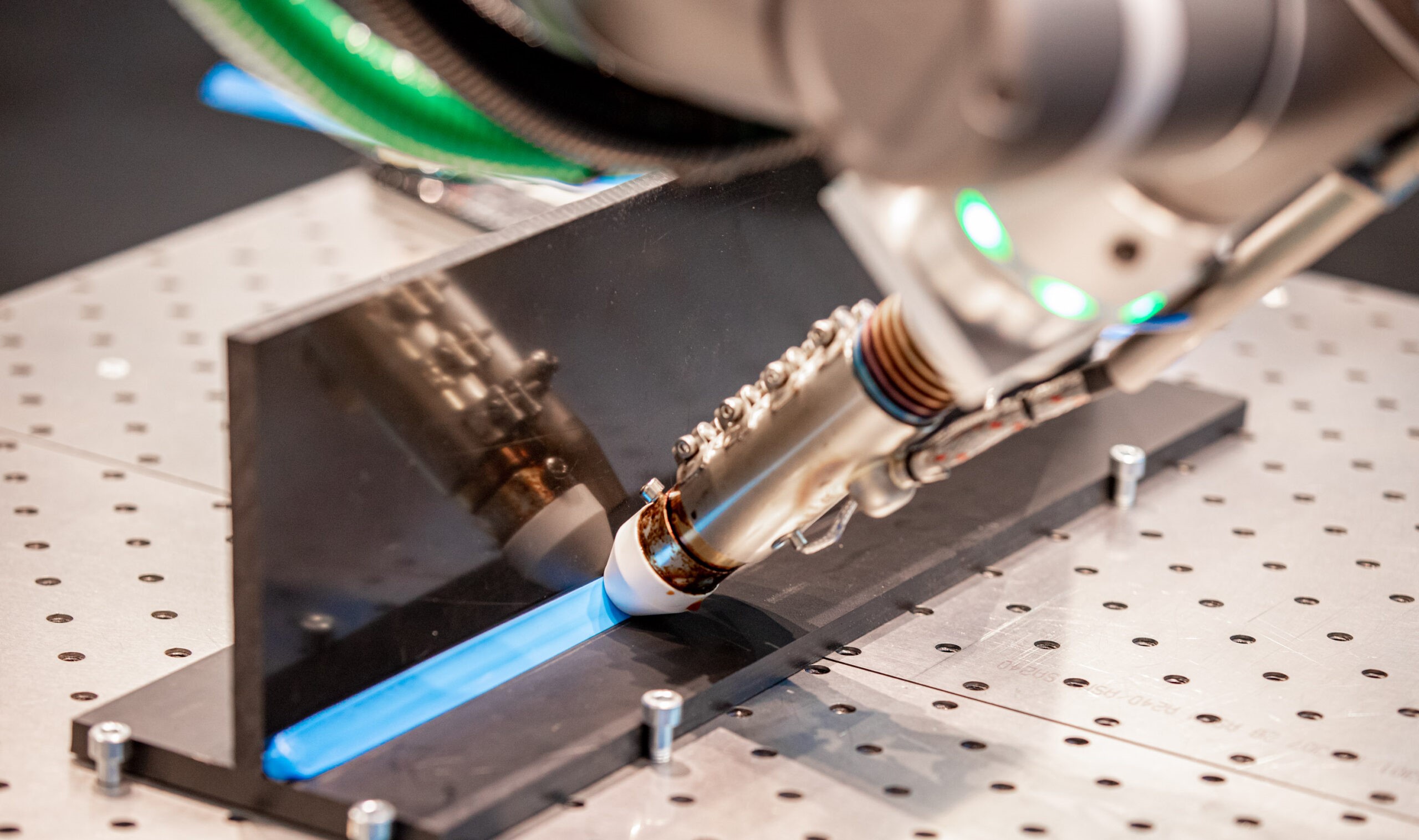
Solving staff shortages
Finding qualified personnel is a major challenge for companies specializing in plastic welding. Unfortunately, there is no quick prospect of a solution to this. Companies that choose to automate the plastic welding process can not only maintain their productivity but also increase it without the need for additional personnel. In addition, welding is often heavy because it is performed with heavy tools. In addition, automating the process can encourage current staff to delve into advanced technologies, allowing them to do more diverse work. This can lead to less staff turnover in the company.
Security and cooperation
Safety is paramount in the manufacturing environment, and cobots are specifically designed to work safely alongside humans. When plastic welding with cobots, operators can stay nearby to supervise and intervene if necessary. This ensures a safe working environment and minimizes the risk of injury.
Improved precision
Cobots are programmed to work with great precision. In plastic welding, accuracy is essential to create strong and consistent welds. By eliminating the human factor, cobots can work with millimeter precision, improving weld quality.
Increased productivity
Cobots can work continuously without the need for breaks, which increases productivity. Moreover, they can be quickly programmed and switched to different tasks, reducing overall production time. This improves efficiency and increases plastic welding output.
Flexibility and adaptability
Traditional welding robots are often programmed specifically for one task. In contrast, cobots are flexible and adaptable. They can be easily programmed for different products, increasing production line versatility. This allows companies to respond quickly to changing production needs and market demands.
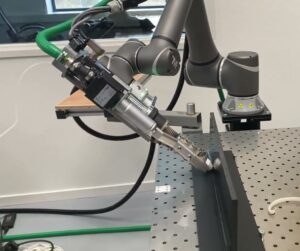
Quality control
Cobots use advanced sensor technologies to monitor weld quality and detect defects. This real-time quality control reduces the risk of errors and ensures product quality. It is even possible to use a camera to check products for unevenness. Constant monitoring allows any problems to be noticed and corrected immediately.
Cost savings
Using cobots for plastic welding can provide significant cost savings. Increased productivity and efficiency reduces production time, resulting in lower labor costs. In addition, improved quality control minimizes the risk of rejects and rework, resulting in further cost savings.
Getting to work!
In short, automating plastic welding operations with a cobot is the ideal way to ensure a consistent level of quality. Using cobots in plastic welding not only improves quality but also increases productivity. Workers previously in charge of welding operations are now given the opportunity to perform other tasks, such as quality inspection or finishing finished products.
WiredWorkers is an expert in automation and has already helped several companies implement welding robots. Contact us or schedule a free cobot consultation!
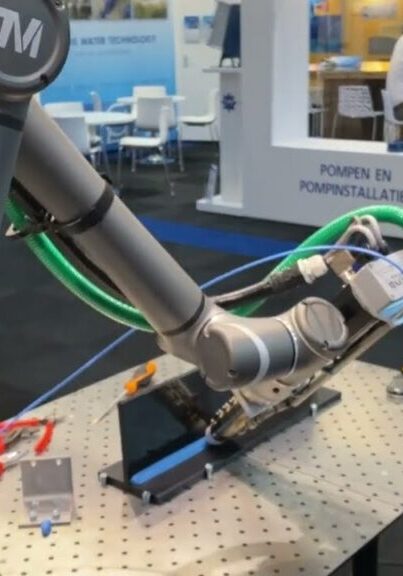