Successfully implementing and integrating collaborative robots into existing manufacturing systems presents challenges. Let's look at some of these challenges and the best ways companies can follow to ensure a smooth transition to using cobots.
System compatibility and infrastructure
One of the biggest challenges in implementing cobots in an existing manufacturing environment is ensuring that they can integrate seamlessly with existing manufacturing systems and infrastructure. This can raise issues related to software compatibility, connectivity and physical space in the factory.
Before implementing cobots, it is essential to conduct a thorough evaluation of your existing systems and infrastructure. Ensure that the IT infrastructure is suitable for communicating with cobots and that the production space is adapted to their physical requirements.
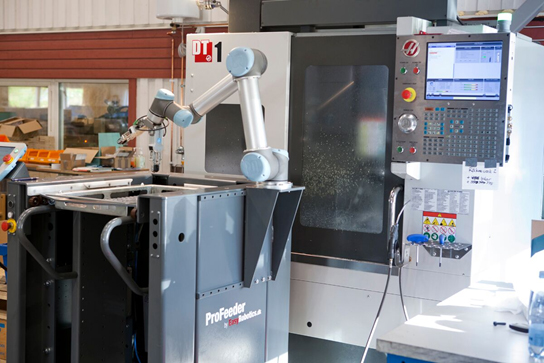
Employee training and education
The success of cobots depends largely on how well human workers can work with them. This typically requires training and education to familiarize workers with the use, programming and maintenance of cobots.
So invest in comprehensive training and education for employees who will work with cobots. This includes not only teaching technical skills, but also emphasizing the importance of safety, cooperation and problem-solving skills.
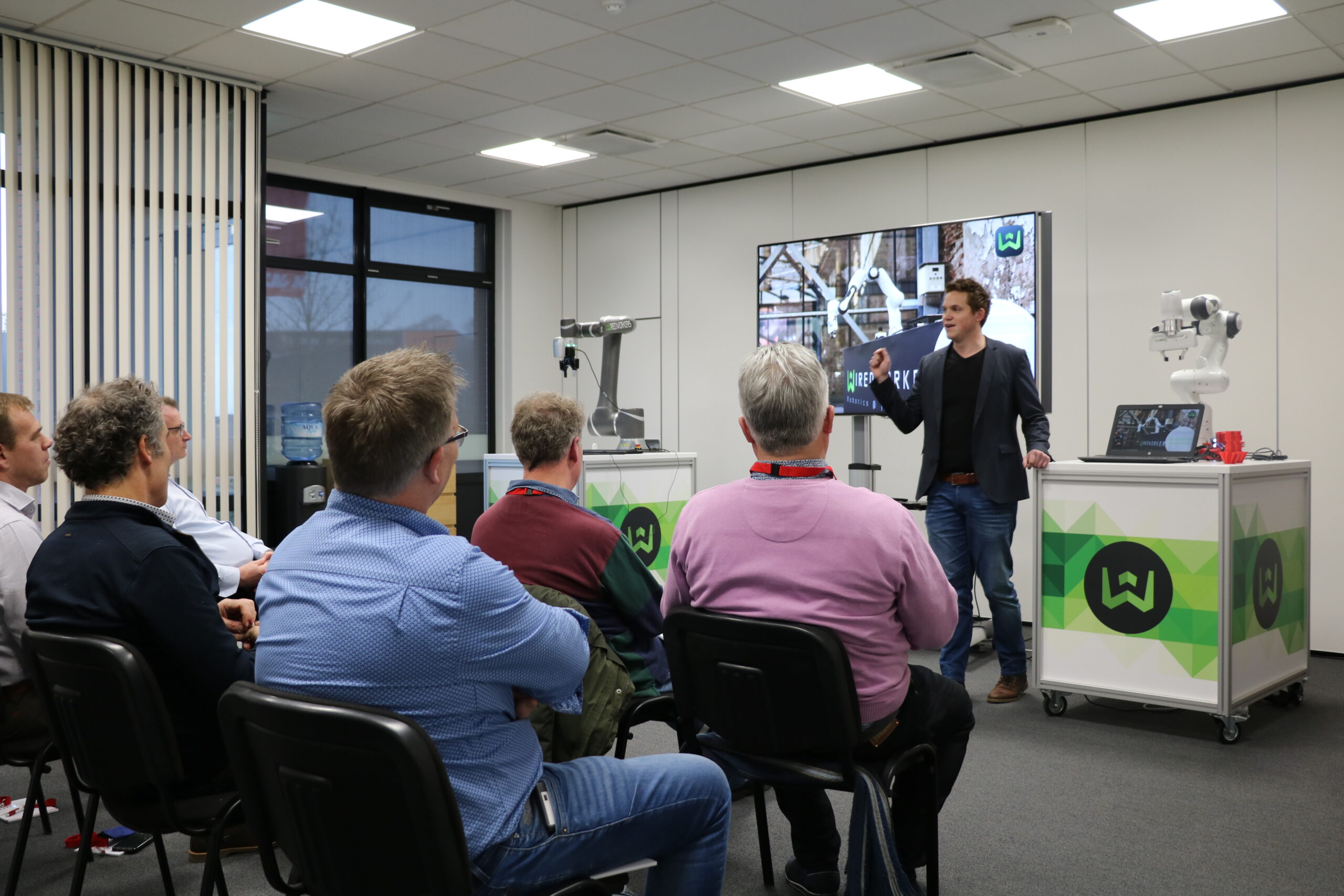
Safety measures and compliance with regulations
Since cobots work side by side with human workers, it is critical to implement strict safety measures to prevent accidents and injuries. In addition, companies must comply with all legal requirements and regulations related to robotics and occupational safety.
Work with safety experts to conduct a thorough risk analysis and implement appropriate safety measures, such as guards, sensors to detect human presence and emergency stops. Also ensure that cobots comply with all relevant standards and regulations.
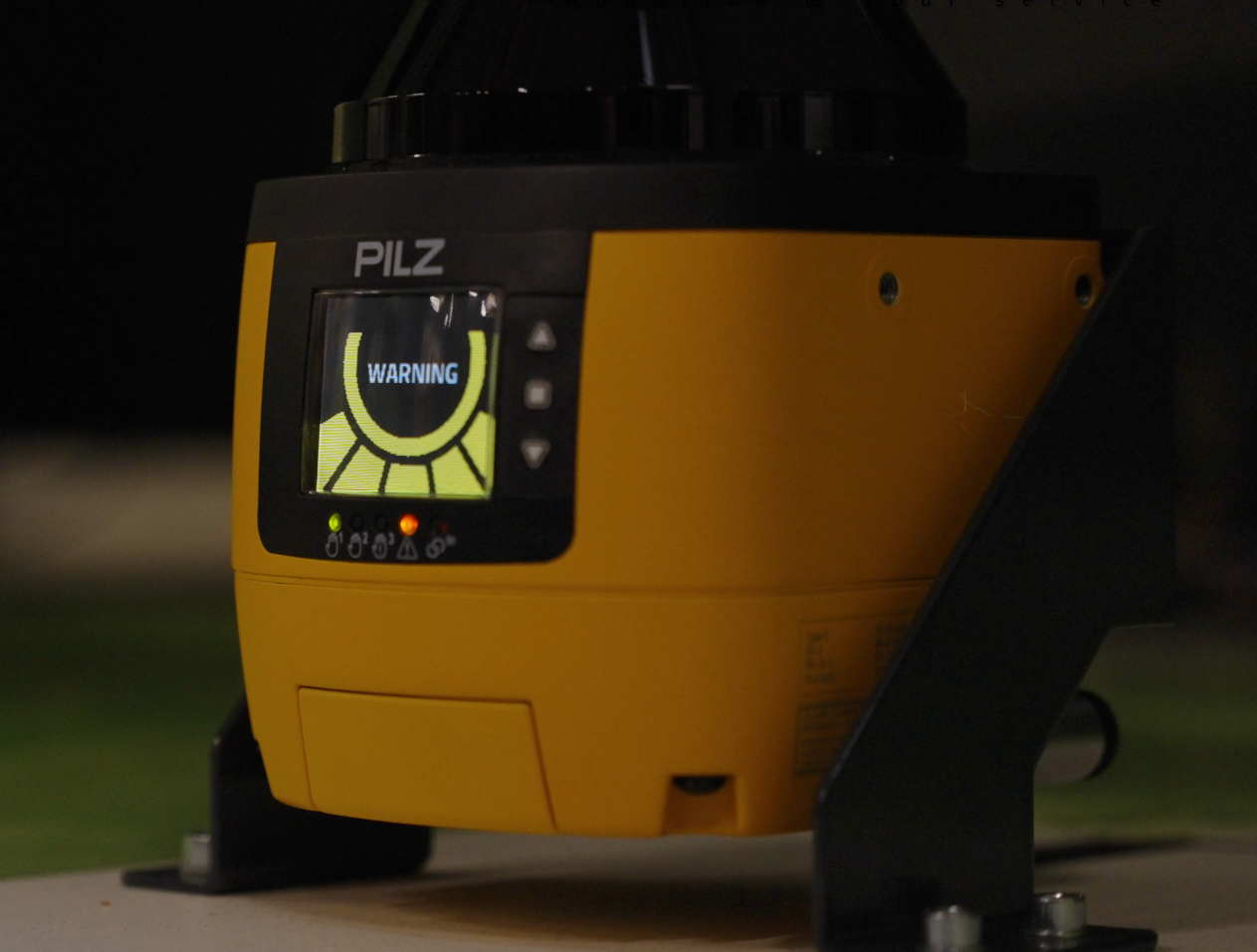
Cost and Return on Investment (ROI).
While cobots can provide significant long-term benefits, such as improved productivity, quality and efficiency, the initial costs of acquisition, installation and training can be significant. It is essential to have a clear picture of the expected ROI before investing in cobot technology.
So conduct a thorough cost-benefit analysis to assess the expected ROI of cobots. Consider not only the immediate costs and savings, but also the long-term effects on productivity, quality and competitiveness.
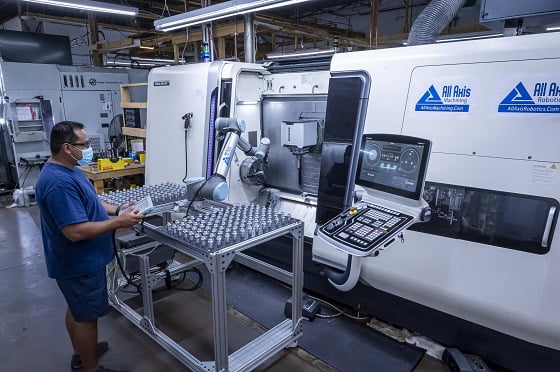
Getting started!
Deploying collaborative robots offers companies significant benefits, but also presents challenges. It is crucial to learn from other companies' experiences and follow proven best practices in successfully integrating cobots into operational environments. By focusing on aspects such as safety, integration, training and flexibility, companies can harness the full potential of cobots and take their operational processes to new heights.
WiredWorkers, an expert in automation, has already helped numerous companies implement collaborative robots. Contact us today or schedule a no-obligation online consultation!