Collaborative robots, or cobots, are redefining what is possible on the production floor. Unlike traditional industrial robots, cobots are designed to work with people. They are smarter, safer and more flexible. But one of their greatest strengths? Dramatically improving precision and quality within manufacturing processes.
Precision without fatigue
Let's face it: even the most experienced craftsman has a down day from time to time. Fatigue, distraction or simply the natural variation of manual work can lead to errors or rework. Cobots, on the other hand, don't get tired. They don't get distracted. They follow their programmable instructions with micron-level accuracy, day and night.
A study by the International Federation of Robotics found that manufacturers deploying cobots reported up to 90 percent fewer errors in tasks such as gluing, soldering and assembly. That's not just more precision; that's a competitive advantage.
Repeatability you can build on
Precision is not just about hitting the nail on the head. It's about doing it over and over again. Cobots excel at repeatability. Take the Universal Robots UR5e, for example, which has a repeatability of ±0.03 mm. That kind of consistency is hard to match by hand, especially over long shifts or at high volumes.
This level of repeatability is crucial in industries such as electronics and medical devices, where even the slightest deviation can have major consequences.
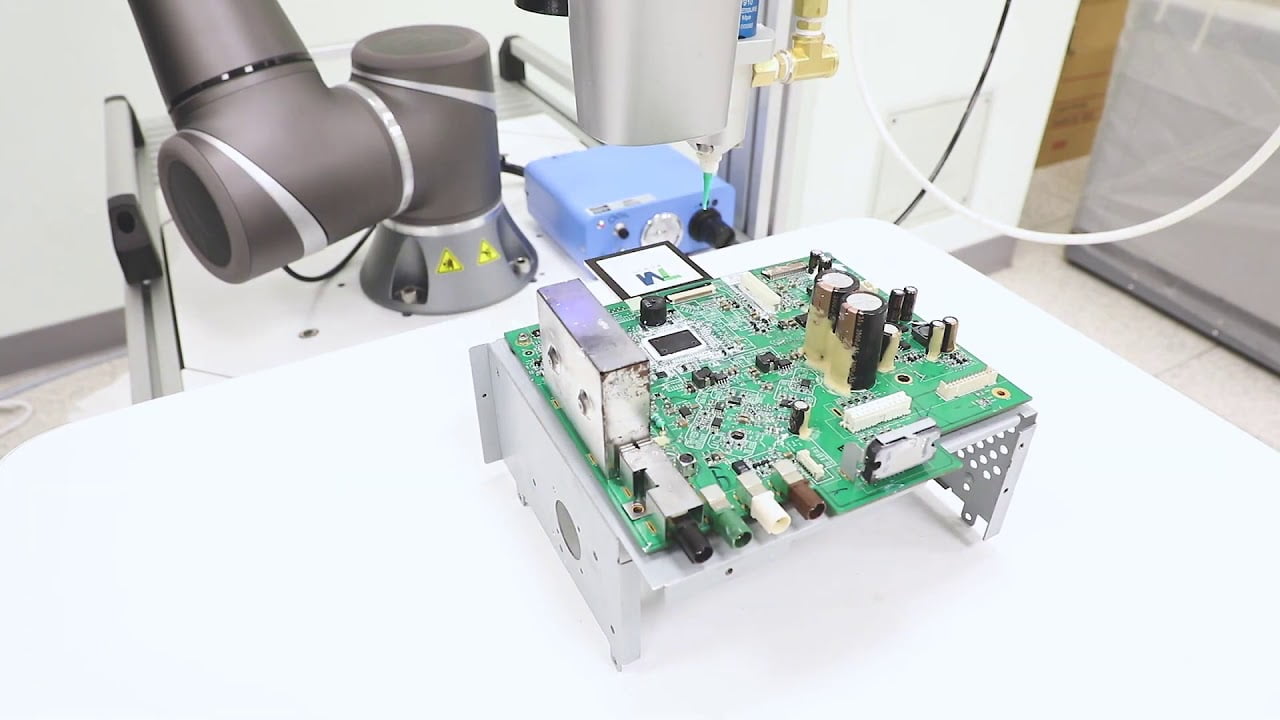
Better quality = less waste
Failures not only cost your reputation, they cost money. Every rejected part means wasted time, material and resources. Cobots reduce these errors, improve first-pass yield and significantly reduce waste.
Take a precision machining customer we worked with. By using a cobot to load and unload CNC machines, they realized a 22% improvement in first-pass yield and a marked reduction in scrap. The result? Satisfied customers and healthier profitability.
Advanced inspection capabilities
Cobots are not limited to performing tasks - they can also check that things have gone well. With vision systems and sensors, cobots can perform quality checks during the process, detecting errors immediately rather than after the fact. This shortens the feedback loop and ensures consistent quality from part to part.
At WiredWorkers, we have implemented inspection systems with cobots that check critical tolerances in real-time on assembled parts. These systems not only detect errors - they prevent them from happening again.
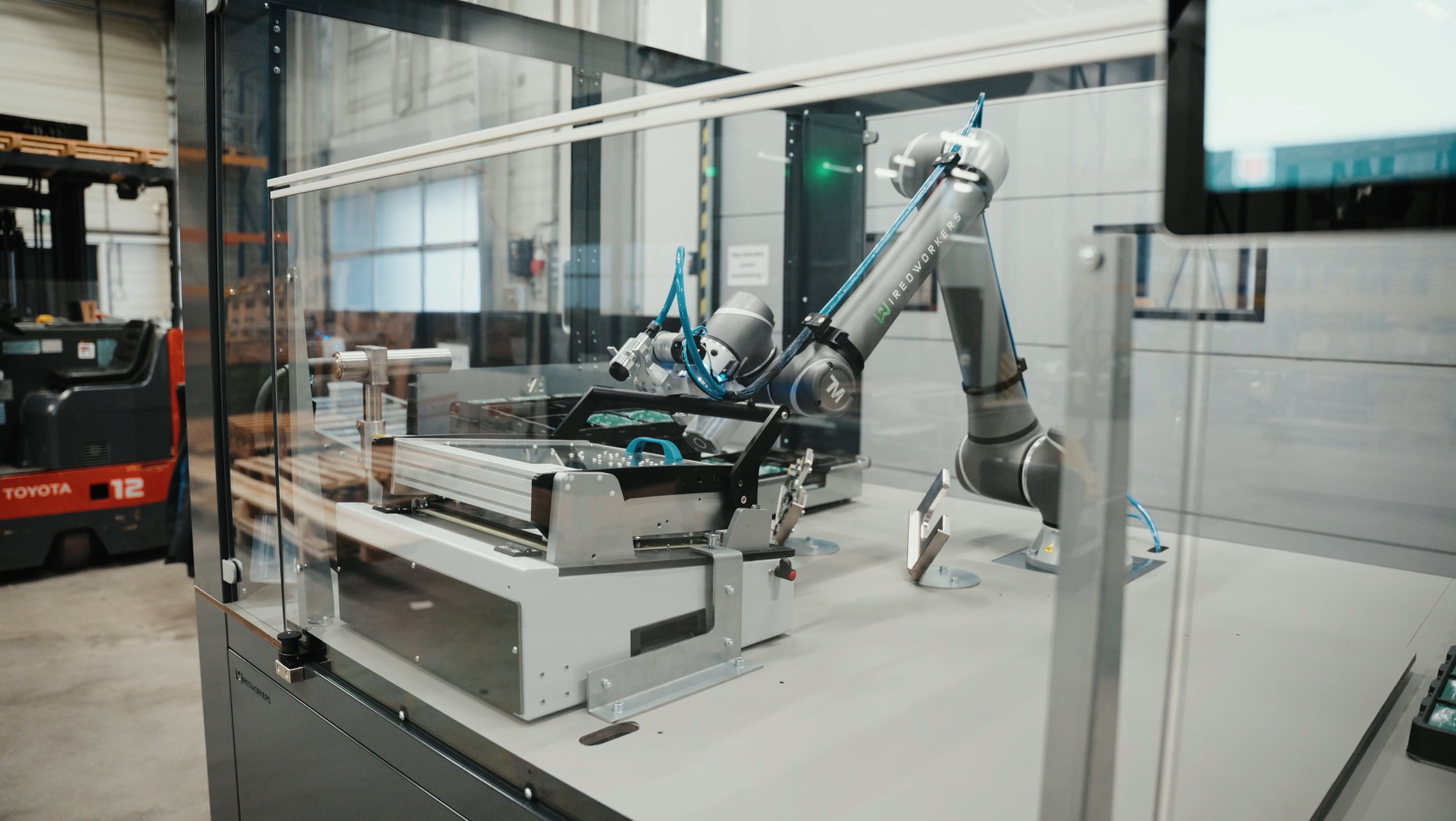
Flexibility with quality
A common myth about automation is that it only works for large batches with little variation. That's a thing of the past. Cobots actually excel in environments with high product variation and smaller quantities, where flexibility is crucial.
Thanks to intuitive programming and fast changeover times, they can easily switch between different tasks or products. That flexibility allows manufacturers to maintain high precision without the cost and complexity of traditional automation.
WiredWorkers: your partner in precision
At WiredWorkers, we don't just provide cobot solutions - we develop them to suit your specific challenges. Whether you want to improve assembly quality, reduce inspection errors or eliminate manual variation, we help you implement systems that increase both precision and productivity.
WiredWorkers is an expert in automation and has already helped several companies implement collaborative robots. Want to learn more about how to integrate cobots safely and efficiently? Contact us or schedule a free cobot consultation!