The Netherlands is facing a major productivity challenge. A shortage of technicians and a persistently high market demand are the causes of this. If you regularly read our blog articles, you probably already knew this. Probably (and hopefully) you are also familiar with the solution we specialise in, namely collaborative robots. Robot arms that have the potential to increase worker productivity and the flexibility of the production process. Milan Wolffgramm, PhD student human-cobot collaboration at Saxion and TechYourFuture did research on 'the robot arm as colleague' in collaboration with professors Stephan Corporaal and Maarten van Riemsdijk. The conclusion? According to them there are many opportunities for HR professionals to optimise the qualities of both people and technology.
Based on interviews, the researchers analysed how cobots are used and what that means for the skills and quality of work of production workers. The main question; 'What does the human-cobot collaboration look like and how is it achieved?' Before they could get started, they did an extensive study on how to best describe the human-cobot collaboration. A combination of knowledge from production management, work design research, socio-technology and psychology yielded five terms that are important for organising human-cobot cooperation. These are a mutually dependent division of labour, skills for interdependent cooperation, quality of work, control capabilities and support.
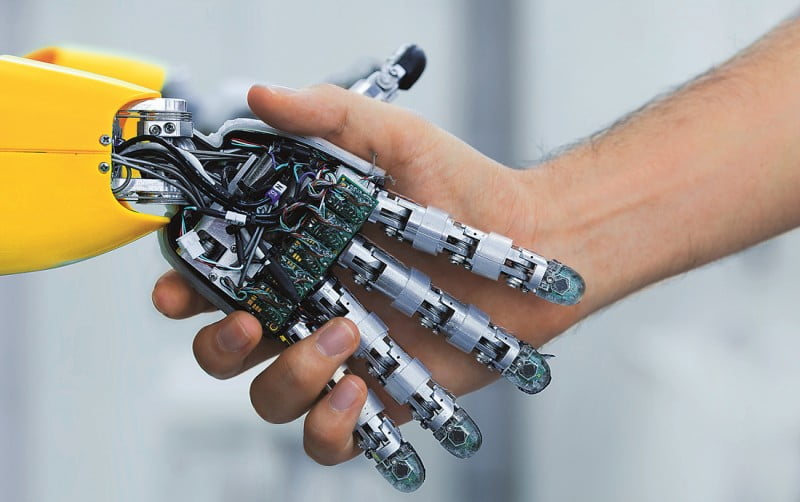
Interdependent division of labour
Interdependence is about the extent to which a cobot is dependent on a human when performing various actions and vice versa. Different levels can be distinguished in this. For example, humans and cobots can work on different sub-products in complete isolation from each other. But it can also be the case that the cobot first does its work and passes it on to the human, who then finishes it off. However, research shows that the more cobot and human work together (and are interdependent), the more they benefit from each other's qualities.
Skills for interdependent cooperation
There are three skills that the cobot and human must possess to work well together. First, perceptiveness. The human must be able to perceive and interpret signals from the cobot. On the other hand, the cobot must be able to perceive humans (using sensors). The second skill is predictability. The human must be able to predict the behaviour of the cobot and must also show predictable behaviour, for example by placing or indicating products in the right way. Thirdly, there must be mutual controllability. Humans must be able to control the cobot with a control panel, for example. On the other hand, a cobot must be able to influence people, for example by sending signals.
Quality of work
A cooperation between humans and cobots that can be maintained by humans requires work that is experienced by humans as being of good quality. This prevents problems such as reduced situational awareness and over-reliance on technology. In addition, there are a number of work characteristics that make people perform better, are more satisfied and show health complaints. Work must be sufficiently complex, varied and autonomous. In addition, physical load is an important component.
Control capacity and support
Productive cooperation with technology is only possible if people can organise their own work. If employees are given a say in how the human-cobot cooperation is organised, they will more readily accept the technology and it contributes to the quality and manoeuvrability of the production system. However, it is not self-evident that every employee is able to set up such a cooperation. Therefore, it is important to make the necessary resources available, such as support, learning opportunities, sources of knowledge and assistance that can be called upon.
The research and the results
A total of 60 interviews were conducted with 21 companies in the East of the Netherlands that had set up human-cobot collaborations. The manufacturing companies had the cobot in production for at least a month and produced both large and small series. In addition, all the cobots were used for assembly work such as screwing, inserting and assembling (sub) products and loading CNC machines, for example. Each interview was conducted with someone directly involved in the implementation and execution of the human-cobot collaboration. These were production managers, engineers and production employees.
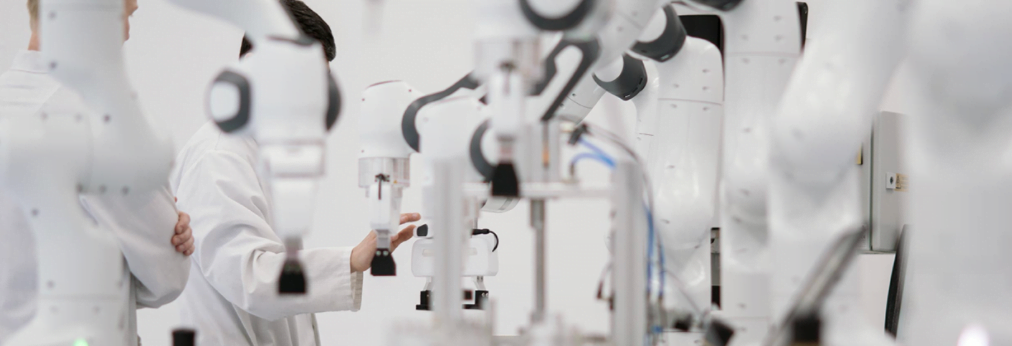
During each interview, the above described facets of a human-cobot collaboration were taken as a starting point. For each of these facets, interesting results emerged. For instance, it appears that in practice, humans and cobots hardly ever work together (and are therefore interdependent). In most cases, they are limited to monitoring and controlling the cobot, which carries out production activities independently. This also limits the skills that an employee must have in order to work together with a cobot. An employee must be familiar with loading and unloading the application correctly, he must be able to start up the cobot, sometimes choose the right programme and if necessary restart the system. In addition, one must be able to monitor progress in order to ensure proper execution.
The effects on the quality of work are variable and strongly depend on how the cobot is used and how it is organised. If the effects on the work content of employees are taken into account during the design phase, it can lead to less heavy, less hectic, more varied and more autonomous work. If it is not taken into account, the opposite results. Another striking result from the study is that production employees are hardly involved in the implementation. In almost all cases, management and engineers decide on the type and process in which the cobot will be implemented. In addition, worker involvement seems to have an effect on the perceived quality of work. The more workers are involved, the higher the quality of work. When it comes to supporting workers, every company pays attention to this. However, each company does this in its own way and there are no companies that have a structured approach.
The most striking result that emerges from the study is the role of HR professionals. In short, there is no role for HR. At no company is HR involved in the implementation of a cobot and in some cases there is even a definite lack of need.
"I don't think that has much added value. Look, you're actually talking about something totally technical here.”
Respondent about HR involvement
Conclusions
The research clearly shows that there is little intensive cooperation between a cobot and an employee. This is not entirely surprising, as it offers the companies surveyed a significant advantage. By letting the cobot do simple routine work, production employees become more productive and there is more room for more complex, changing tasks. Depending on the choices made by management and production engineers, the executive work becomes better. However, the true potential of a cobot is not yet being exploited anywhere. The cobot has specific properties to enter into a direct, mutually attuned cooperation with a human, in which they help each other out. A production unit consisting of man and machine that can produce complex and constantly changing products entirely independently, at mass production costs and with high precision and quality. The Dutch manufacturing industry does not yet seem to have reached that stage.
Another conclusion from the study is that production workers have no input. Engineers investigate what the technology can do and devise a possible application in existing production. When optimising the possible application, they pay minimal attention to the tasks of the production employee. They are instructed and supported where necessary, but that is as far as it goes. This is a point of concern, because it means that cobots, with all their unique characteristics, are used in the same way as the 'old' industrial robots in the car industry and logistics. The human being is not the central focus here, but the final piece of the technology. Something that has regularly been warned about in the past, including by the Borstlap Committee (Committee for the Regulation of Work, 2020).
The above could be prevented by asking engineers and production managers to design systems that take the qualities and work preferences of production workers into account from the outset. This means a system with mutual cooperation between people and technology, and with workers participating in the decision-making process. These systems would also be more robust, flexible and productive in practice. HR could play a very important role in this, as they have the knowledge. But, as the study shows, they are ignored everywhere.
Recommendations
The researchers therefore come up with five recommendations for HR professionals to contribute to a human-cobot collaboration that employees can and want to sustain.
Get involved with technology implementation
The first recommendation is to get involved as early as possible in the implementation of new machines. Taking into account the purpose for which the technology was purchased, HR professionals can help bring out the unique qualities of employee and technology. In addition, HR can help clarify where the quality of work will be affected, which employee skills need to change and ensure that employees are involved in the process. In other words, creating a multidisciplinary group with knowledge from various disciplines at an early stage.
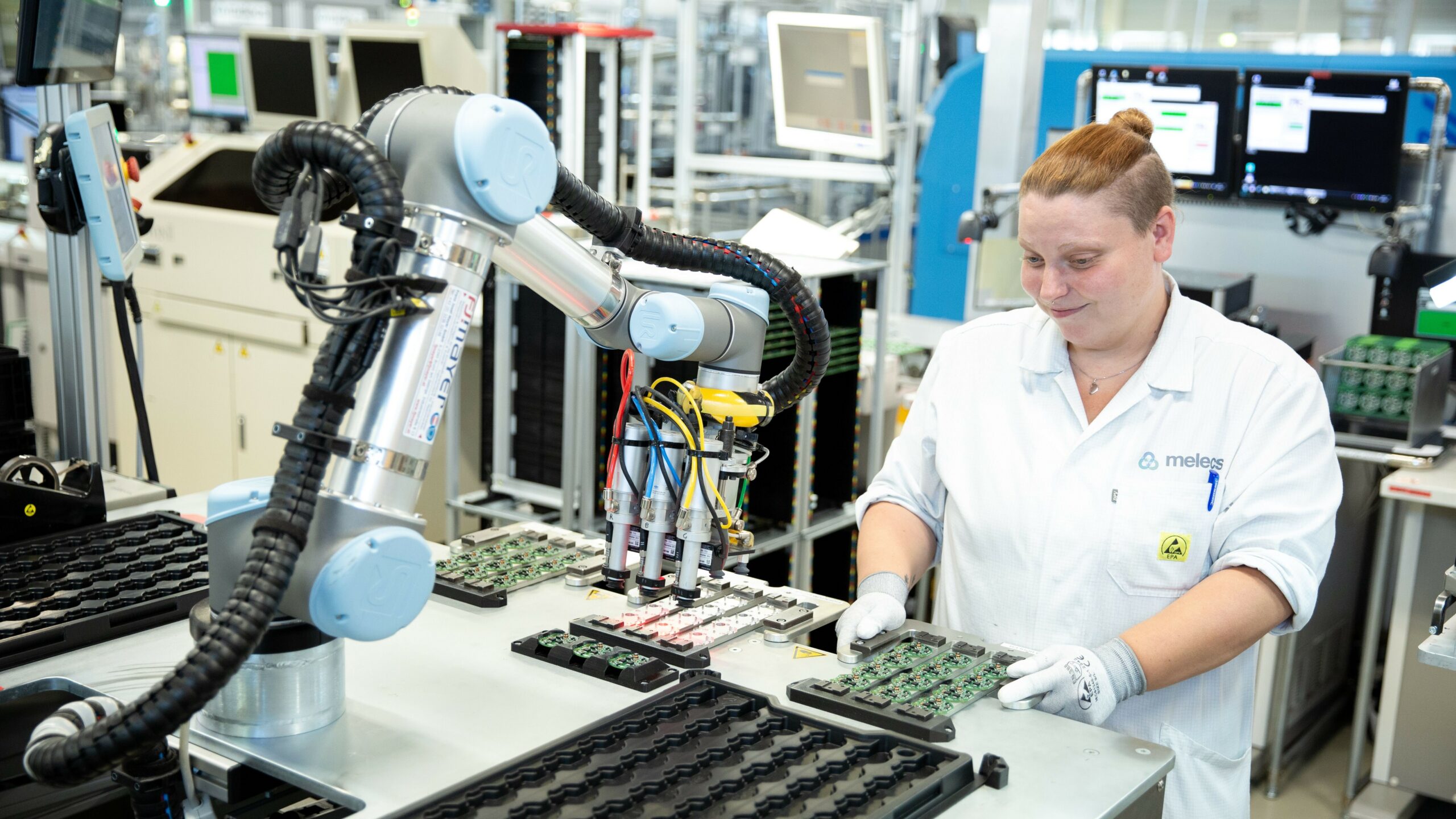
Know what is going on in the primary process
In order to implement good human-cobot cooperation, the primary process is obviously the starting point. For an HR professional it is therefore important that they know what is happening on the work floor. What is being made? How is it made step-by-step? In which series size? How often does it have to be changed? What skills are needed?
Know the technical possibilities and limitations
Besides the process, it is also important that the HR professional has knowledge of the technology to be implemented. This means not only doing research in their own department, but also at product level. Look at user experiences, talk to production managers and engineers or visit external parties who supply the technology.
Organise support and involvement
Make sure that employees are not taken by surprise, but are informed at an early stage and also involved in the implementation of new technologies. In addition, offer on-the-job development programmes for employees to master new techniques. This way, they get to know new techniques step by step and uncertainty and resistance are prevented.
Monitor the developments
Finally, as an HR professional, it is important to monitor the human-cobot cooperation after implementation. This will help monitor the effects experienced on the quality of work and, in the long term, determine whether the collaboration is sustainable for the worker. It is also important to collect data on technology-related incidents and performance declines. These are indications that the human-cobot cooperation is not working well and that an appropriate redesign may be required.
Get to work!
In short, cobots are a promising way to overcome the productivity challenge facing the Netherlands. But precisely that which makes these cobots so unique, the ability to work with people, is often not fully exploited. In addition, production workers, the ones who will be working with the cobot the most, are not fully taken into account in the run-up to the implementation.
At WiredWorkers, we strive to create a world where the qualities of employees are fully utilised, and are happy to help make the implementation of human-cobot collaboration as successful as possible. Want more information? Are you curious about how a cobot can be used as effectively as possible in your company? Or are you the HR professional who wants to know more about collaborative robots? Then contact us or register for a free cobot consultation.