For many SMEs, it is difficult to automate screwing within their production process. It is difficult to determine in advance whether the benefits of automation outweigh the investments involved. In addition, production within SMEs is characterized by small series with a lot of variation, which makes automation more difficult. The advent of collaborative robots has changed this dramatically and made automation feasible in multiple situations. This also applies to automating a screw process. What are the benefits of a collaborative screw robot?
How does this differ from traditional screw automation?
The difference from the traditional way of screw automation is in the accessibility. The machines used for this purpose are often large and expensive, while their use is limited. This makes sense, as they are developed for mass production environments with high volumes and little variation.
Traditional screw solutions are therefore not as flexible. Each machine can only handle one type of screw. In addition, reprogramming a program is complicated and it takes an automation specialist to carry it out. Also, the turnaround time for an implementation is a time-consuming task. It takes several weeks to implement such a screw application. Collaborative robots, on the other hand, provide a new approach to automation that is characterized precisely by flexibility and accessibility.
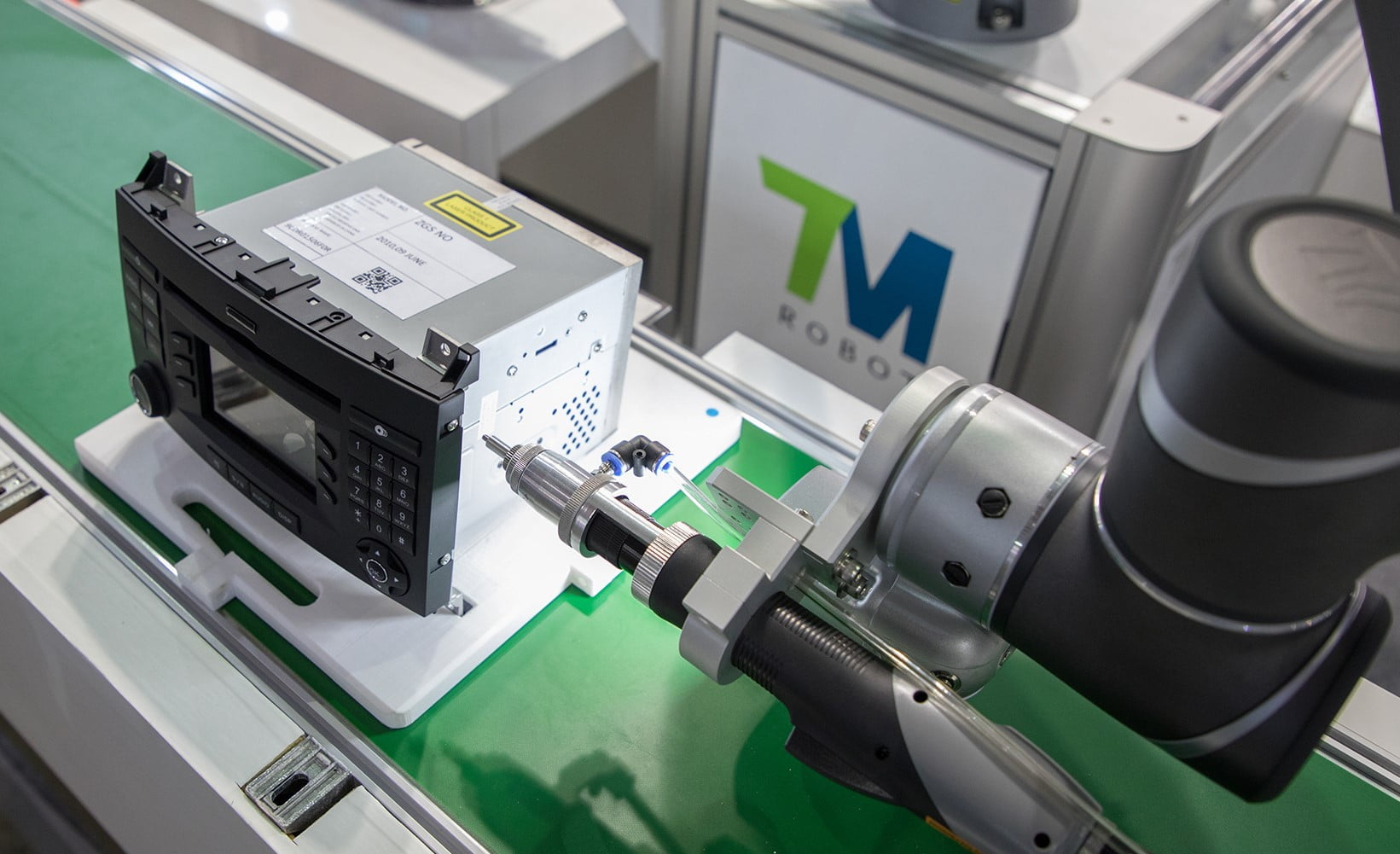
Benefits of a collaborative screw application
Thanks to collaborative robots, automation has become accessible to a wider audience. Companies that did not have the ability to automate in the past have many new opportunities to increase production and remain competitive with the advent of cobots. As such, automating screwing operations with a cobot has a number of advantages over manual screwing, or automation with a traditional robot.
Easy programming
As mentioned, programming a traditional screw solution is a time-consuming task that often requires hiring outside robotics expertise. Cobots come with a simple programming interface that anyone can operate with a laptop, tablet or smartphone. In addition, it is no longer a matter of days to program a robot, but a matter of minutes. A saving of time and money!
More flexibility
Unlike traditional robots, a cobot is flexible. It is easy to convert them to other tasks and, in addition, they can perform multiple types of screw operations. Screwing operations can therefore be automated almost anywhere in the production process.
Improved quality
People are not very good at repetitive work, such as screwdriving. With such a boring task, over time a worker's concentration will weaken and this affects the quality of the work. A robot will always perform its action in the same way, with the same force. Therefore, the quality of your product will always remain constant.
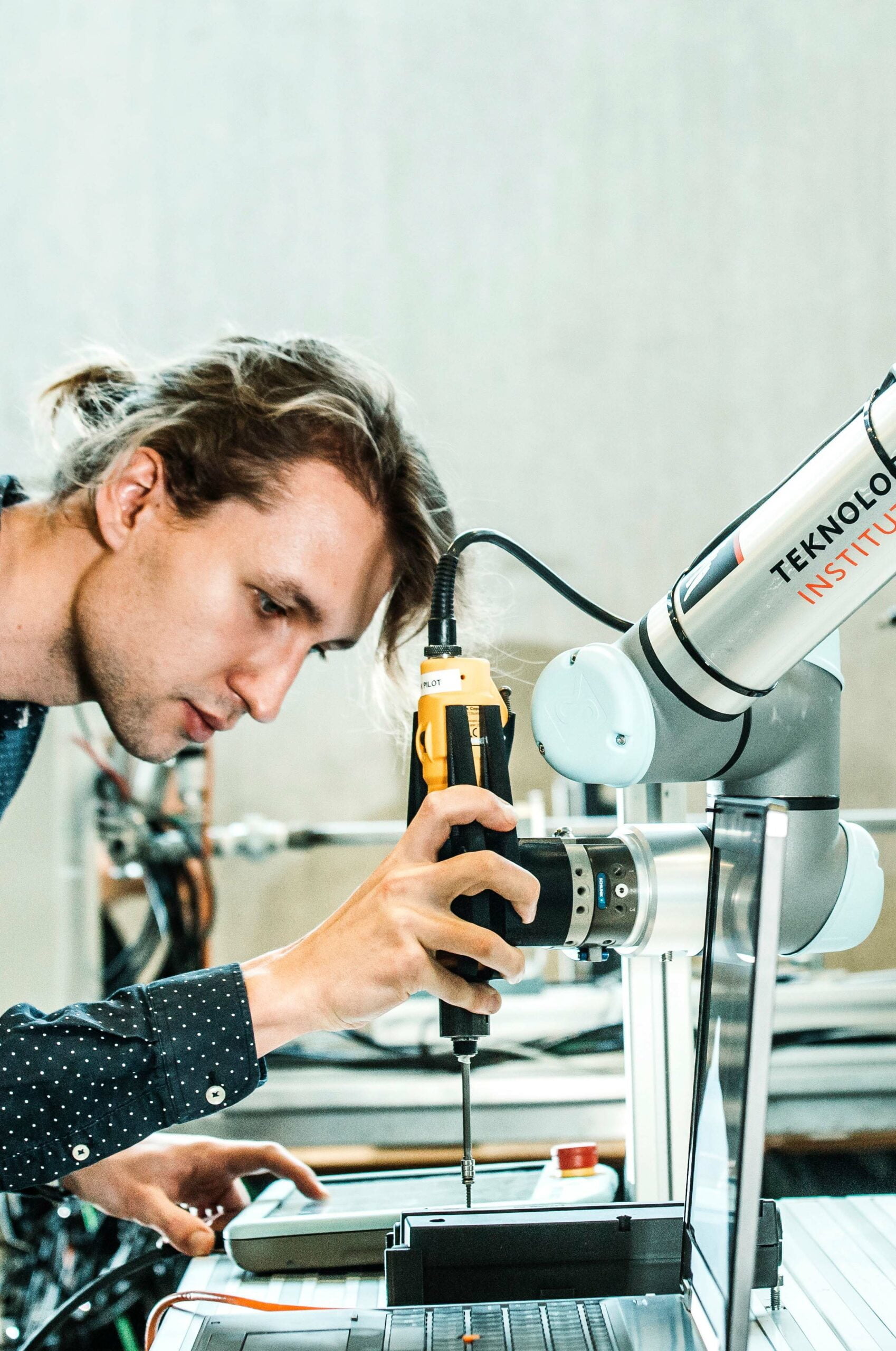
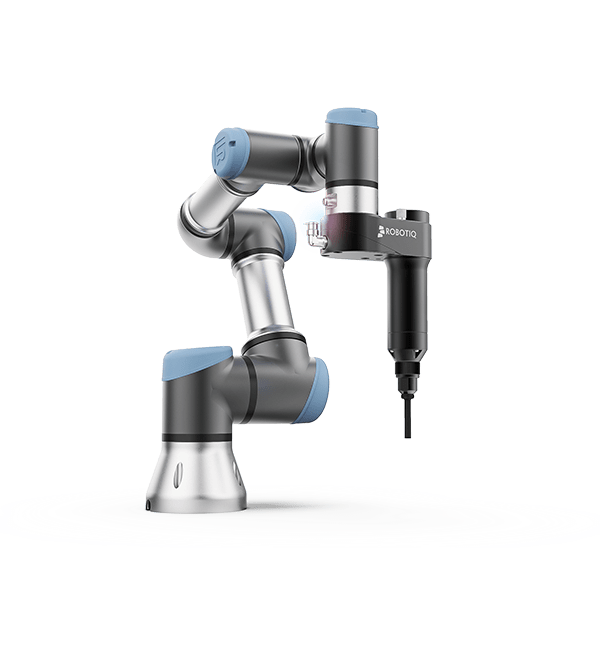
Reliability
Manual screwing brings a certain inconsistency and it is difficult to rely on it 100%. Other steps in the production process can get into trouble as a result, for example because the cycle time varies depending on the person performing the task. A robot is more reliable and works constantly.
Rapid deployment
Whereas the implementation of a traditional robot often takes months, a cobot can be deployed within a few days. This makes the payback period a lot shorter and limits downtime for other activities.
Fewer injuries
One major problem that manual screwing presents is that over time it can impact a worker's body. Musculoskeletal disorders, such as carpal tunnel syndrome, can occur over time due to screwing. Robots take over the harmful work from the worker leading to less sick leave and better quality work.
Little space required
Compared to traditional robots, collaborative robots take up little space because they are compact lightweight robots. In addition, a collaborative robot is suitable to be in the same work space as humans and does not need to be shielded with large fences.
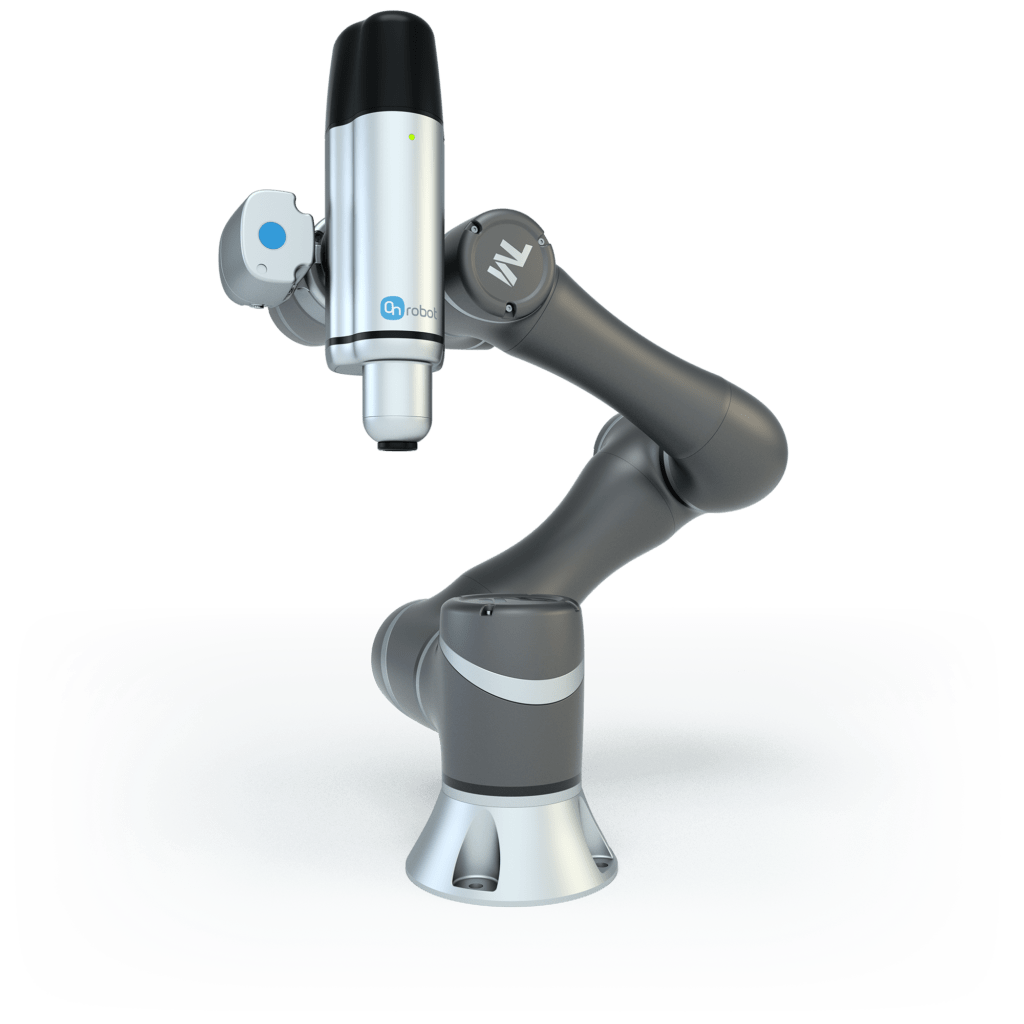
Fast ROI
Unlike a traditional robot, the Return On Investment is incredibly fast. This is partly due to the low investment costs, cobots are generally a lot cheaper. Whereas with a traditional robot system it can take several years before it pays for itself. With collaborative robots, depending on the application, this can be reduced to a few months.
Extremely accurate
Not only is a robot more constant than a human, it is also more precise. Whereas humans are good at dealing with variability, robots are extremely precise. For example, collaborative robots have a position replicability of less than a millimeter. For screws, this characteristic is more than suitable and it reduces the margin of error.
Get to work!
WiredWorkers specializes in automation and can help make the right choices. We strive to create a world where the qualities of workers are fully utilized, so we are happy to help make implementing robotic applications as successful as possible. Would you like more information? Are you curious about how a robot can be used as effectively as possible in your company? Then contact us or register for a free cobot consultation.