That automation is an important part of staying competitive and future-proof in the coming years is something most companies know. Yet for many companies it remains difficult to determine exactly what they need and which solution is suitable to make processes run as efficiently as possible. Within the manufacturing industry, robotics is a great way to create a pleasant work environment for employees and increase production. Staff are relieved of heavy, dangerous tasks and companies can also increase their profitability.
Before manufacturers can get started with industrial automation, it is important to look at which robotic solution is suitable. The most important choice is between a collaborative robot (cobot) or an industrial robot. But what is the difference between the two? In this blog, we'll look at the differences.
What is an industrial robot?
Those who are not familiar with collaborative robots will quickly think of an industrial robot when they think of a manufacturing robot. Large machines that are made to work very quickly and very accurately with heavy objects or at great distances. They have a fixed place in the workshop, basically always do the same work and (normally) deliver a fixed level of quality. The purchase price is often high so the ROI is also often several years. All these features make an industrial robot suitable for production processes that will not vary for a long time. In other words, large batches with little variability.
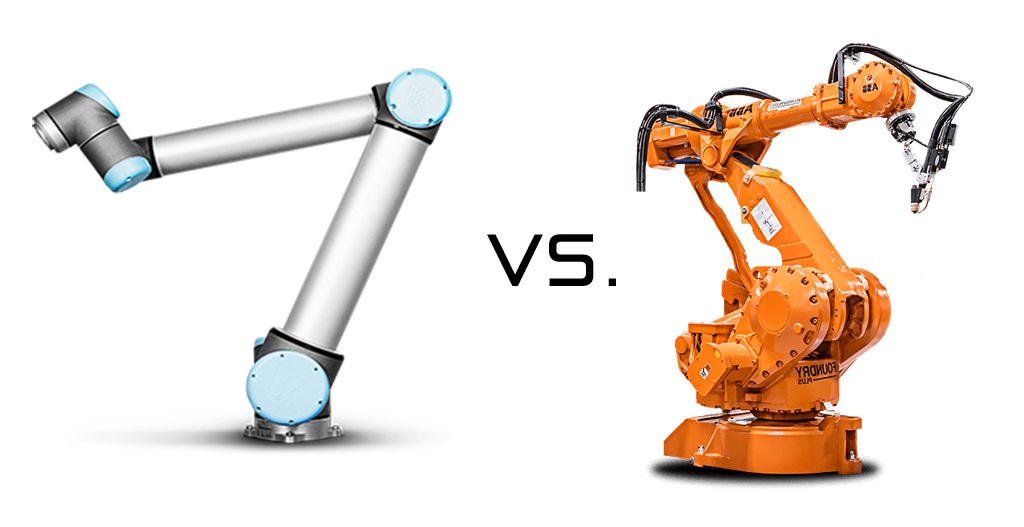
The size and range of industrial robots, on the other hand, do present some problems. Because they are so accurate and powerful, they are perfect for tasks that require heavy lifting. However, this does have the consequence that they are not as accurate when it comes to force control. For tasks where a high or varying degree of sensitivity is required, an industrial robot is not the right option. Industrial robots are a good option when it comes to speed, weight and reach. In addition, they require extensive safety measures so that they are safe to work in a factory with people. For example, people or robots must be shielded by cages. Realizing and designing them takes a lot of time and can also drive up the cost a bit.
What is a cobot?
Cobots can basically perform the same tasks as an industrial robot, only they are a bit smaller and lighter. In addition, (after a risk assessment, of course) a cobot can generally work near people with minimal or no safety fencing. This is because a cobot has built-in force control and sensors, meaning that it will automatically slow down or stop if it is obstructed in its path or if someone approaches.
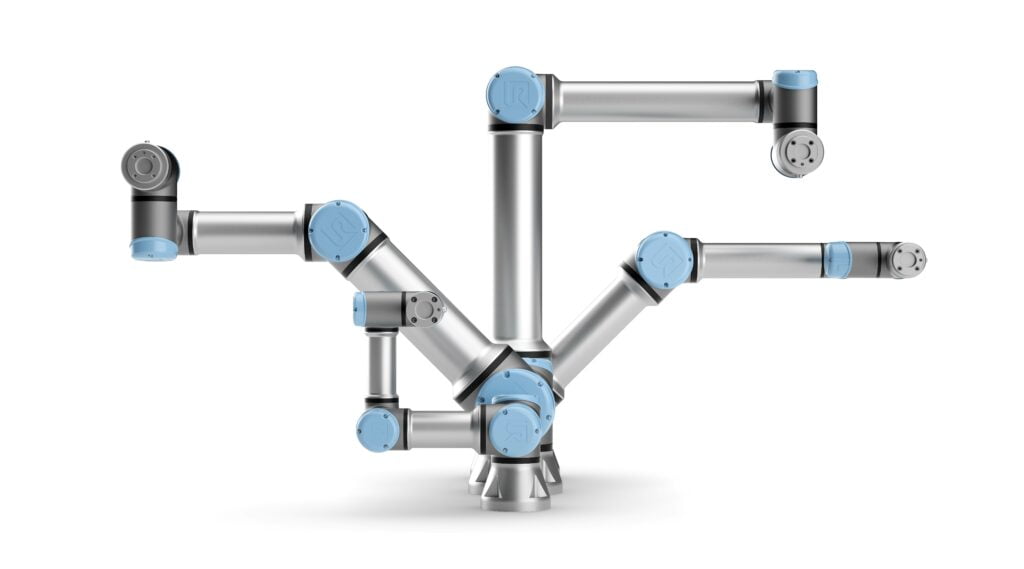
Cobots are suitable for a wide range of industries and sectors and are capable of performing various applications. In contrast to industrial robots, they are simpler and more flexible. They can be attached to a (mobile) workbench or table and are therefore deployable at different places in the production process. Staff can easily convert them to new tasks, thanks to the simple programming software.
Just as the size and heaviness of the industrial robot brings disadvantages, the lightness and adaptability of the cobot also brings some disadvantages. In terms of payload, reach, and speed, cobots have to sacrifice a lot compared to industrial robots. Heavy tasks with large products are therefore quickly a size too big for a cobot. But for small productions, with small series and for facilities where there is little space, a cobot is more than suitable.
What is the right choice?
Cobots and robots do essentially the same thing; enable companies to automate manual processes, speed them up and increase quality. It is and will remain an indispensable factor in maintaining continuity and competitiveness. No company is too small to benefit from automation and where an industrial robot may be out of reach, a cobot usually is not. In fact, they offer some fundamental advantages.
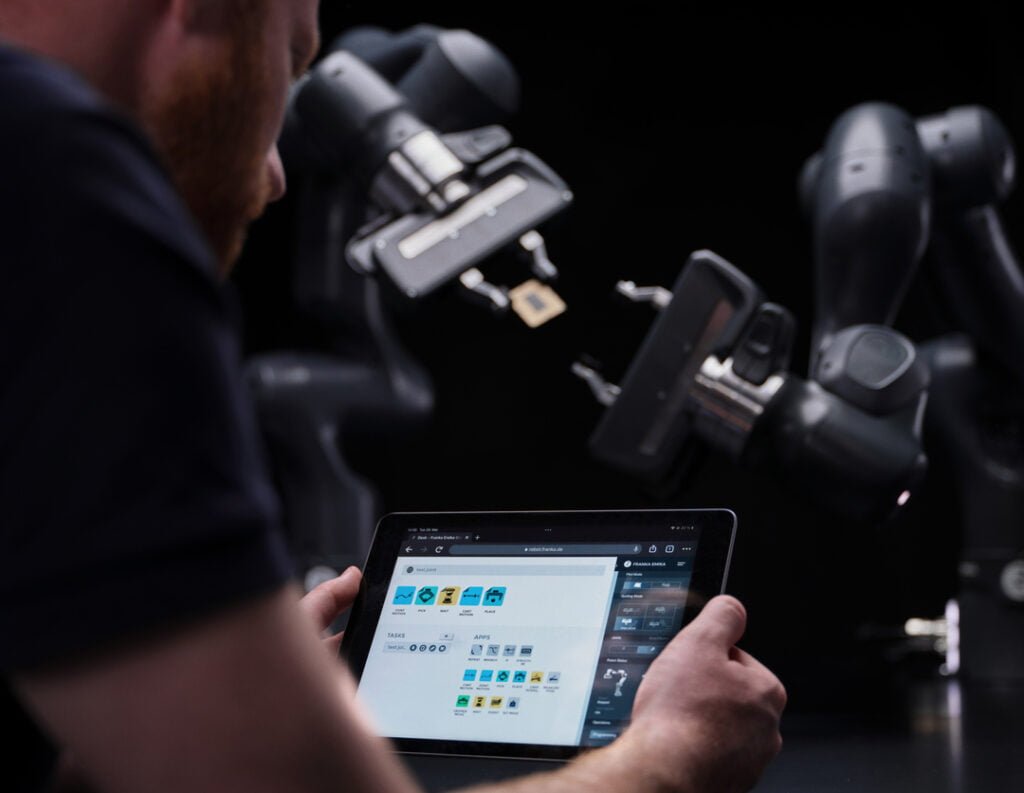
Cost
The biggest difference between industrial robots and cobots is cost. Making a business case to convince management is often easier to justify in the case of a cobot than one in the case of a traditional robot. Not only are purchase costs lower, but maintenance costs and energy consumption also come into play. Collaborative robots have an average ROI of one year.
Flexibility
Choosing an industrial robot also means choosing a fixed production process. When an industrial robot performs a task, it will have to do so for an extended period of time. Reprogramming takes a lot of time and also requires the necessary knowledge. For large companies with large volumes and standardized operations this is not such an issue, but for smaller companies this flexibility is important. With a wide range of grippers, tooling, software and the ability to reprogram the cobot itself, it is possible to have one cobot perform multiple tasks within the company.
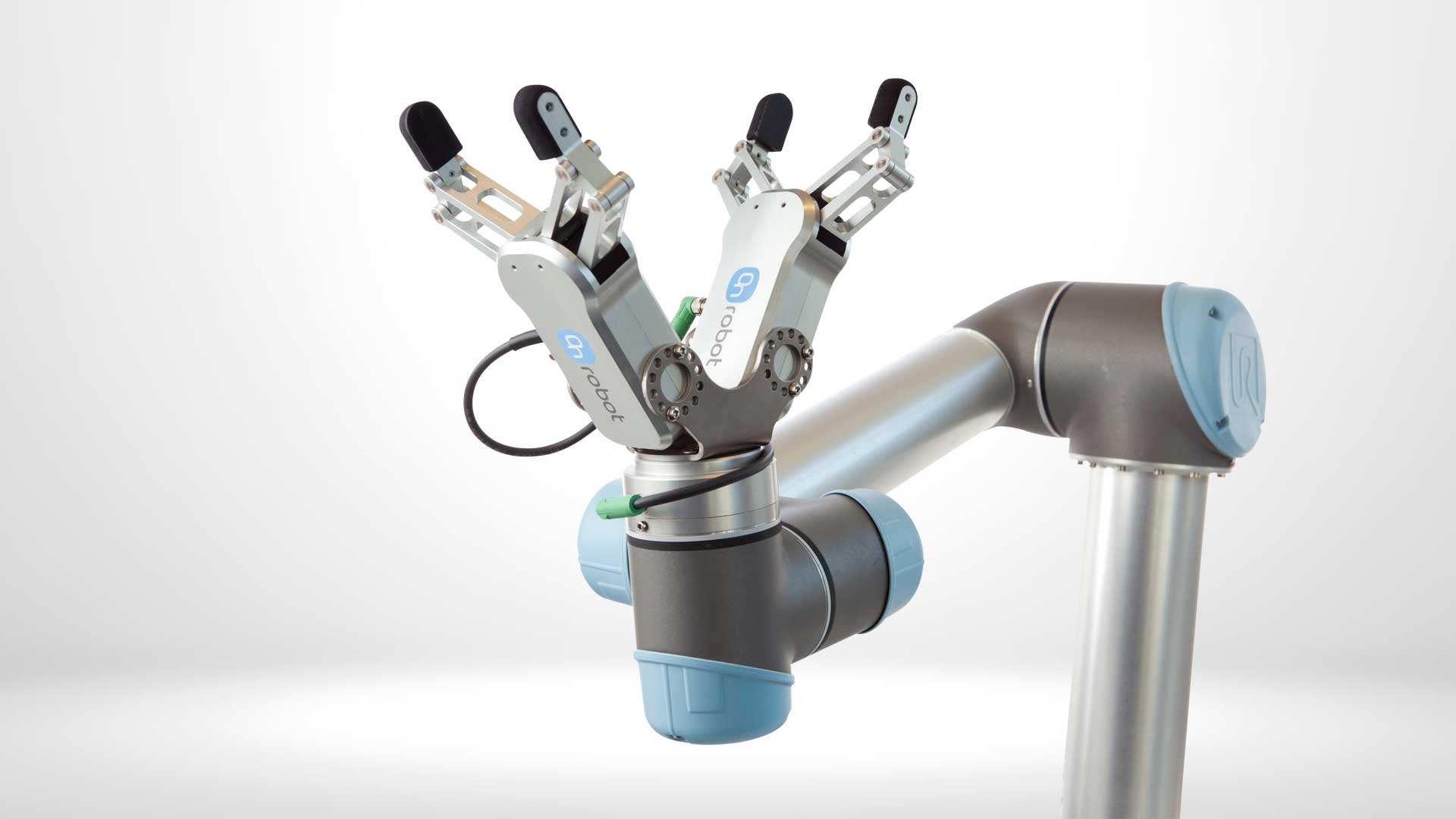
Simplicity
The labor shortage is happening all over the world. The digital transition that is becoming increasingly important in every sector also means a high demand for digital skills. Especially in the areas of automation, machine learning and robot programming. Therefore, an enthusiastic team of programmers dedicated to making the implementation of a robot a success is not easily found. Cobots can help with this because they can basically be programmed by anyone. The end-effectors, hardware and software are quick and simple to set up, which accelerates the implementation of industrial automation.
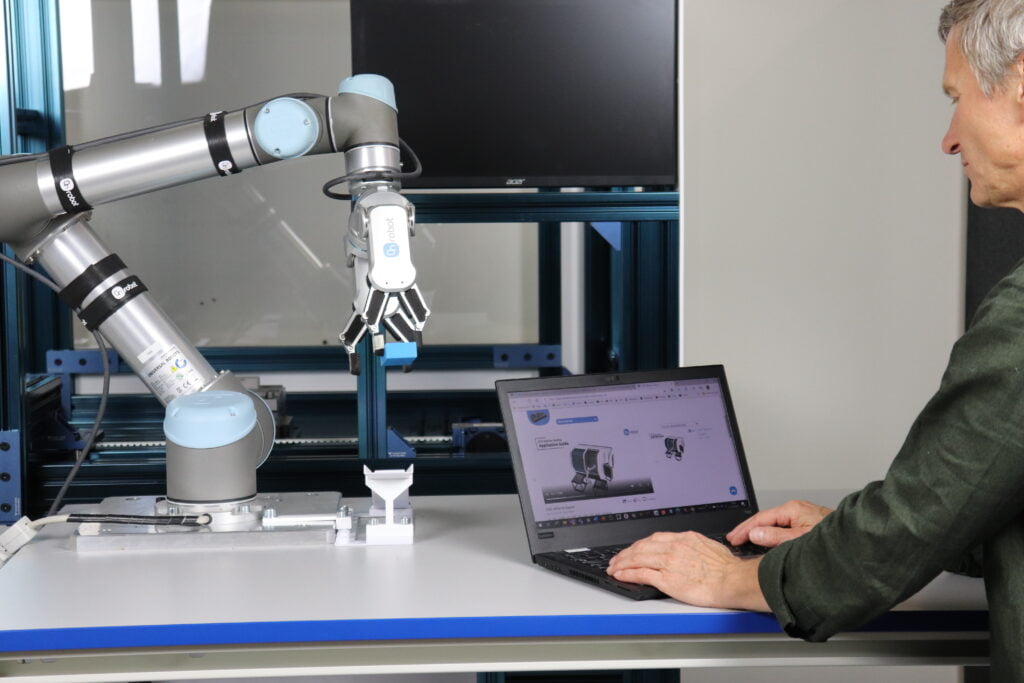
Conclusion
Let's face it. Both robots have their advantages and disadvantages. It depends very much on the task and the products to be automated. Industrial robots are suitable for large companies that produce many pieces in a standardized way. Smaller companies can benefit from the flexibility and cost-effectiveness of a cobot. Yet one does not preclude the other. Large companies can also benefit from the advantages of cobots.
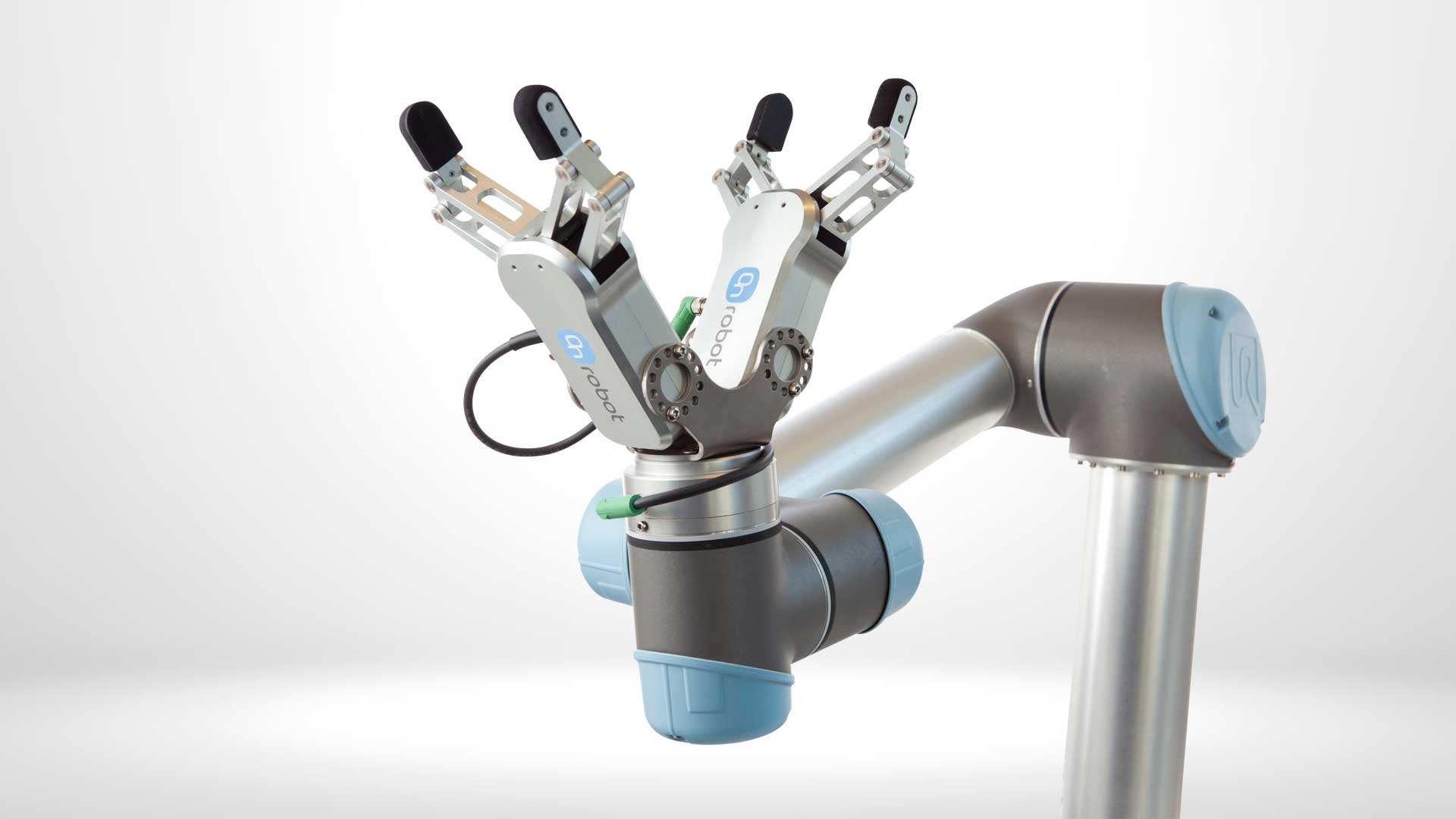
WiredWorkers specializes in collaborative robots and can help optimize the production process. Want to know more about how we do it? Contact us or schedule a free cobot consultation!
Frequently asked questions
What are the main differences between industrial robots and collaborative robots (cobots)?
Industrial robots are large, powerful machines designed for tasks that require heavy lifting and high speed, but they lack force control. They are typically fixed in place and often require safety measures like cages. On the other hand, cobots are smaller and lighter, with built-in force control and sensors. They can work near people with minimal or no safety fencing, making them more adaptable and flexible.