How do you optimise the layout of a palletiser?
The benefits of cobots are not going unnoticed by many companies and palletising, in particular, is gaining popularity. When designing a palletising application, there are a number of factors that can significantly affect cycle time. In this blog, we take a closer look at these factors and how to design a palletising solution in the best possible way.
The layout of a palletiser
With the right palletiser layout, space is optimised, faster cycle times are achieved and doer feed is increased. Factors that influence this include the placement of the robot, the position and orientation of the conveyors and the size of the pallets. Small changes here can already yield huge gains. For example, a robot placed further away from the conveyor belt can take two seconds longer to pick up a box. Two seconds may not seem like much, but over an entire working day, this can add up to a difference of hours.
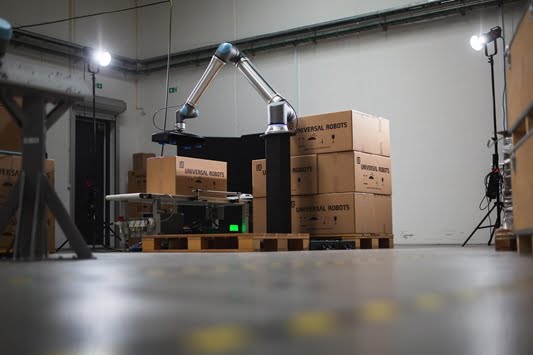
7 factors to consider when designing a palletiser
1. Positions of robot relative to conveyor belt
The position of the robot and conveyor is probably the most important consideration in any cell layout. The conveyor should be positioned so that boxes are delivered as close to the robot as possible.
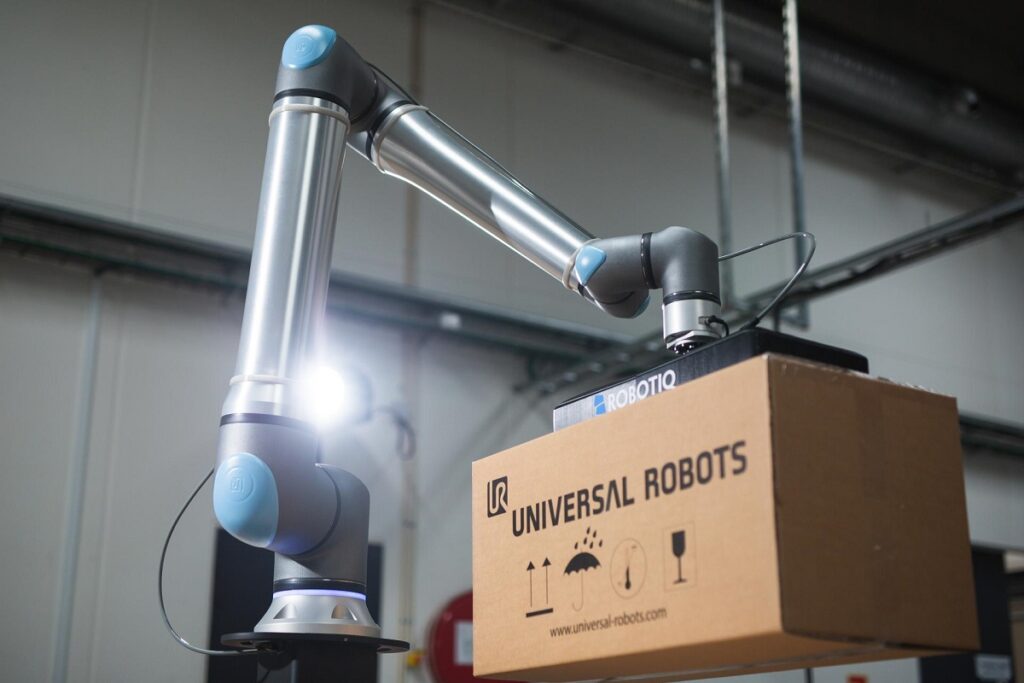
2. Safety zone
Although cobots work together, safety measures are needed for a palletiser to do its job. It is important that there is enough space within the safety zone for everything to work, including operators going in to feed and remove pallets. By carrying out a proper risk analysis, the major hazards are identified in advance. In this way, a palletiser is designed that is both safe but can also do its job in the most efficient way possible.
3. Distances between components
The distances between all parts of the palletiser directly affects the cycle time. The greater the distances, the more time the robot needs to bridge them, the more unproductive the palletiser becomes. Distances should be reduced as much as possible, obviously without creating opportunities for collisions.
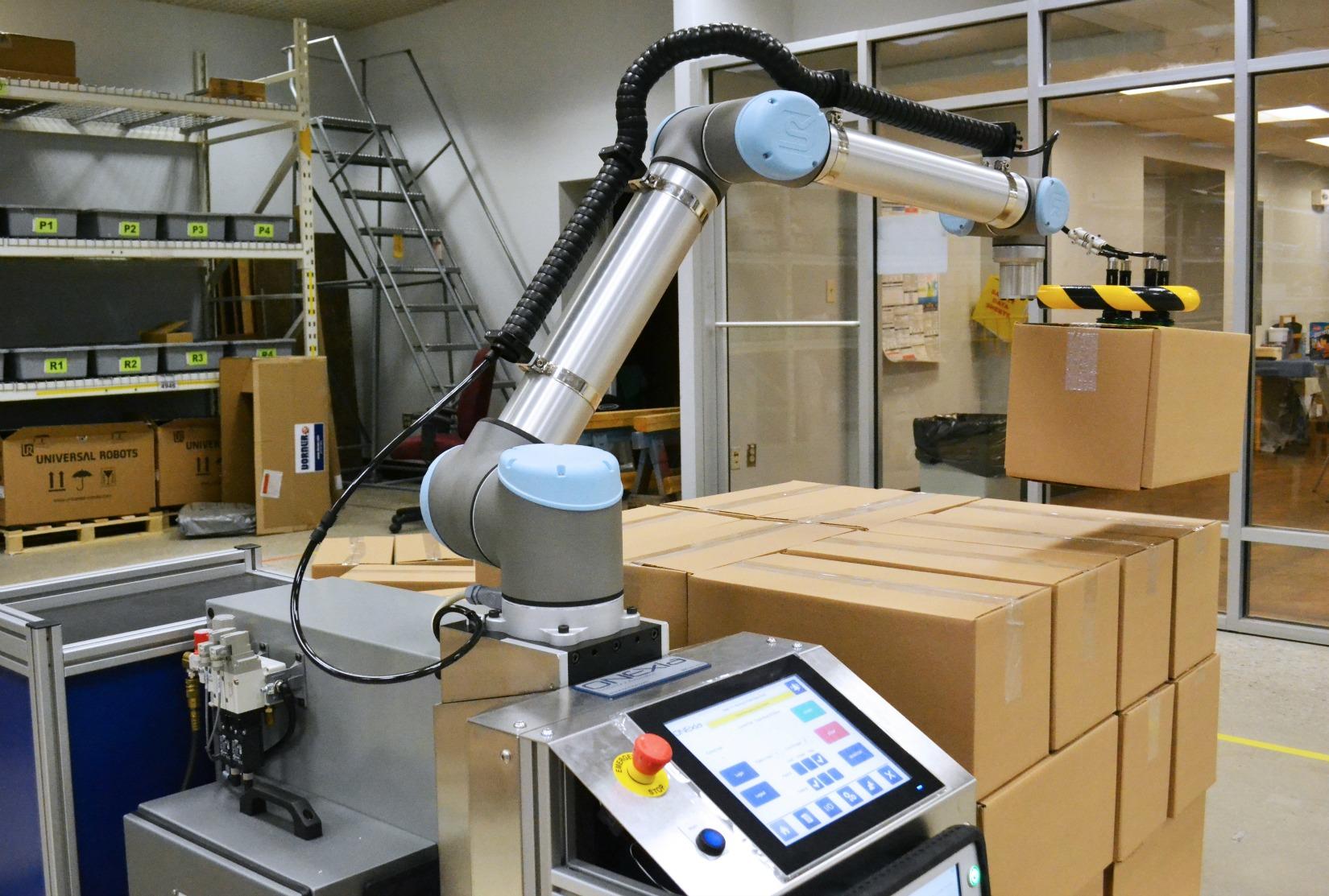
4. Height of conveyor belt
The height of the conveyor in relation to the robot and the pallet has a great influence on cycle time. The ideal height is in the middle between the top and bottom of the loaded pallet. This way, the distance the robot has to travel to place a box is arranged most efficiently.
5. Horizontal distances
Besides distances in height, horizontal distances are also an important factor. Should it be necessary to add an extra step, such as labelling or adding slipsheets, it seems most obvious to place this far from the conveyor belt to avoid collisions. However, this would add extra time to any box placement. Instead, it is better to minimise this distance.
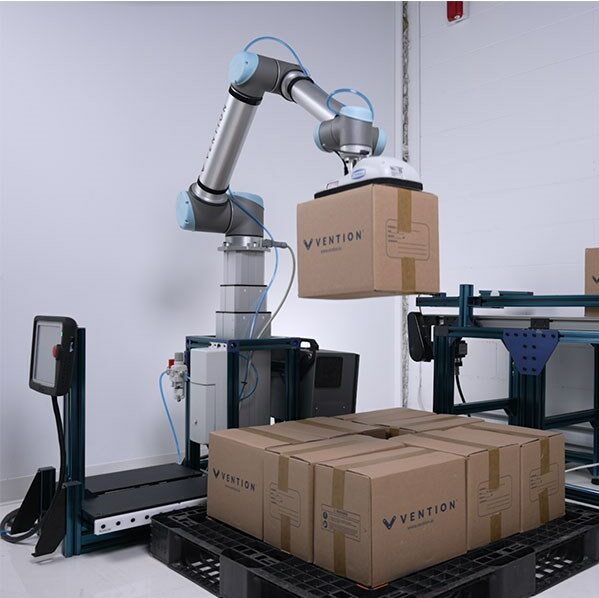
6. Position of external tools
We talked briefly above about slipsheet placement. It is important to consider the placement of these and other external tools. The best place is directly behind the conveyor pick location.
7. Chosen robotic solution
The final factor affecting cycle time is the robot solution chosen. If the palletiser has to change pattern frequently, or the sizes of the boxes change frequently, it is wise to choose a flexible robot solution, such as our WiredWorkers Cobot Palletizer. Thanks to the simple included software, adjusting the cycle is programmed and/or improved in no time.
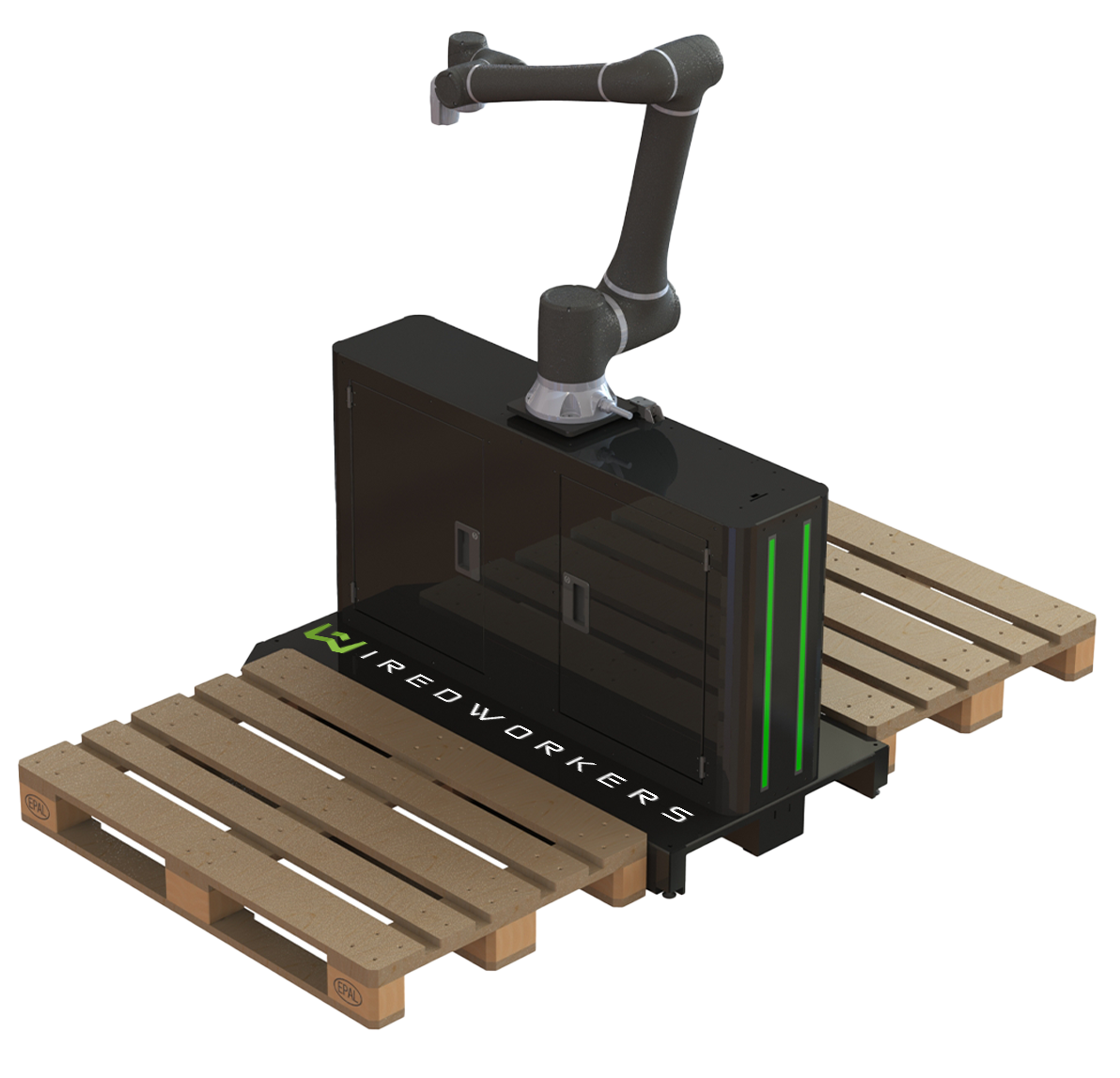
Minimise distance for optimal layout
Many of the above factors have to do with distance. By reducing the distances within the different parts, unnecessary movements are minimised. By planning well and taking a good inventory of the space and products to be handled beforehand, it is quite possible to get the most out of the robot.
WiredWorkers is an expert in automation and has already helped several companies implement palletisers. We can help design an efficient robot cell, including a clear cost estimate and ROI. Contact us or schedule a free cobot consultation!
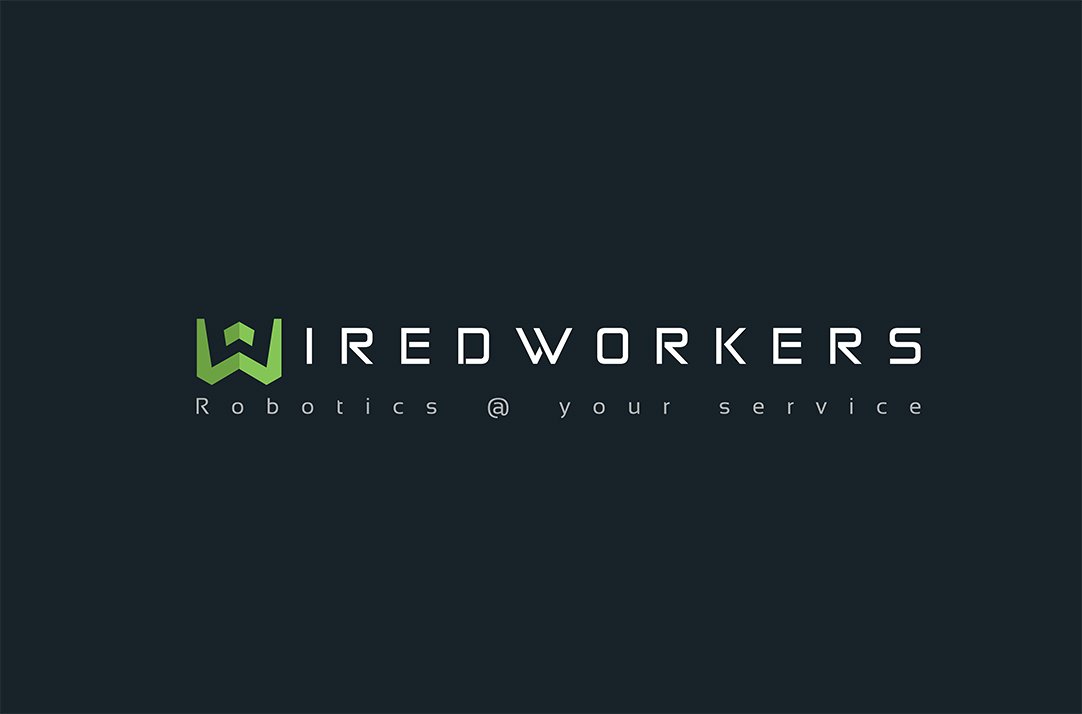