Denmark is the country of choice when it comes to robotics and collaborative robots. It is not without reason that this is the country of the cobot capital Odense, but also of Odense Robotics. A cooperation of about 300 companies and 7 leading knowledge institutions that focuses on robot and drone technology. They recently published a report entitled: "The use of cobots by Danish companies: barriers, advantages and needs". The aim; to inform and educate Danish manufacturers in the possibilities and use of cobots. What can we learn from this?
The report is the result of a series of interviews with various Danish companies in the manufacturing industry. Although the research focuses on Danish industry, the results are interesting for the manufacturing industry in general. This blog looks at barriers that prevent companies from starting with cobots and what they need to make the implementation of a cobot successful.
"Manufacturers want to know how to optimise their production, while distributors of robots and automation want to learn more about their market. This is where the report comes in handy and can be used as a tool for Danish companies everywhere. Endless opportunities await Danish industry once they have decided to implement cobots in their production," says Christina E. Wanscher, Network Manager, Odense Robotics.
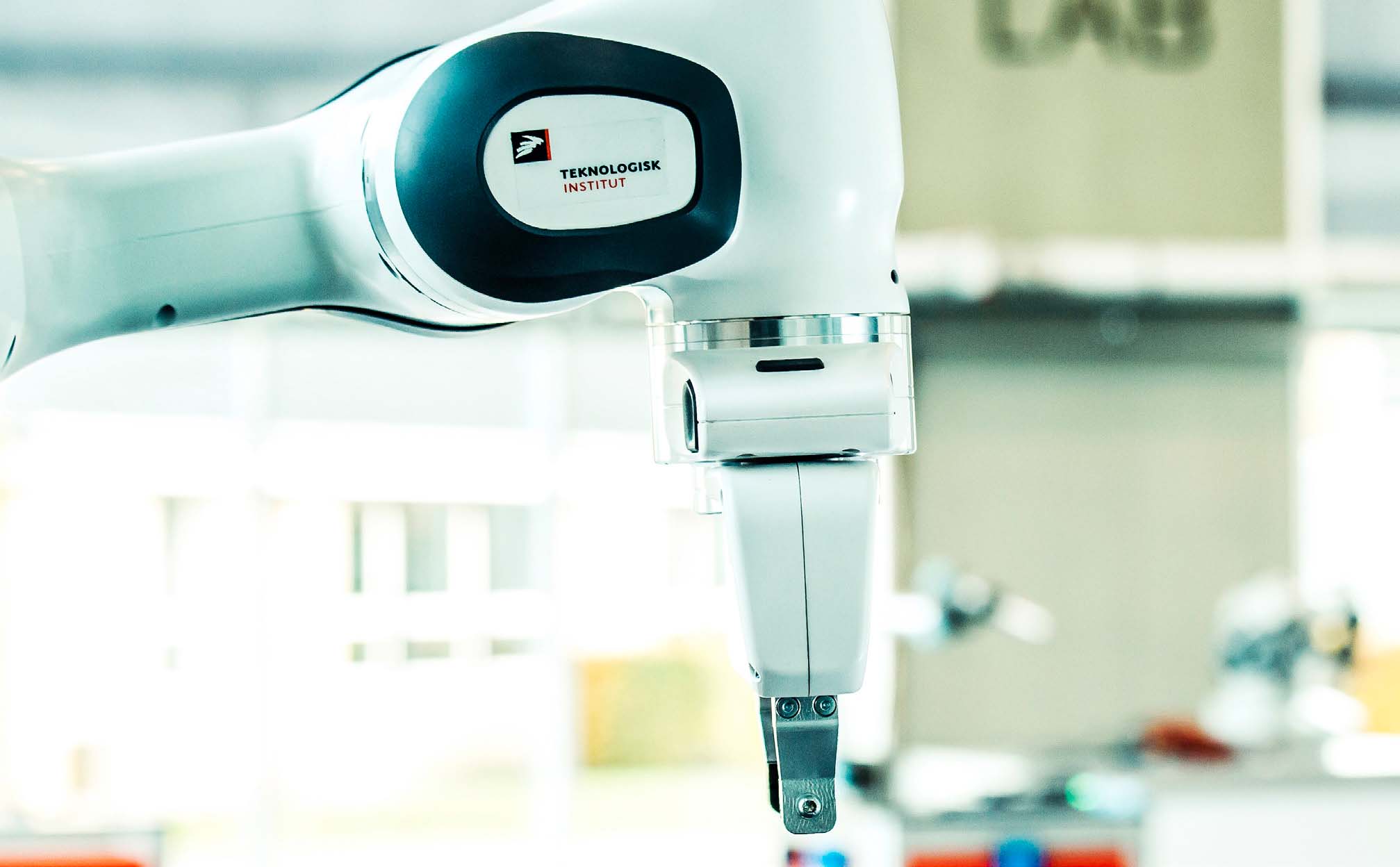
Barriers
First of all, we look at barriers. What reasons are there not to start using cobots? To answer this question, companies that do not use cobots were interviewed, but also companies that do. The most interesting results are presented below.
Knowledge
The lack of knowledge is seen by companies as the main reason why they have not (yet) started using cobots. The companies that have successfully deployed cobots usually had one or more enthusiasts with strong technical insight driving the development. These companies also indicated that in-house expertise is crucial for a successful implementation. It is therefore important to train the staff together with the automation company in order to bring the knowledge level of the staff up to the required level.
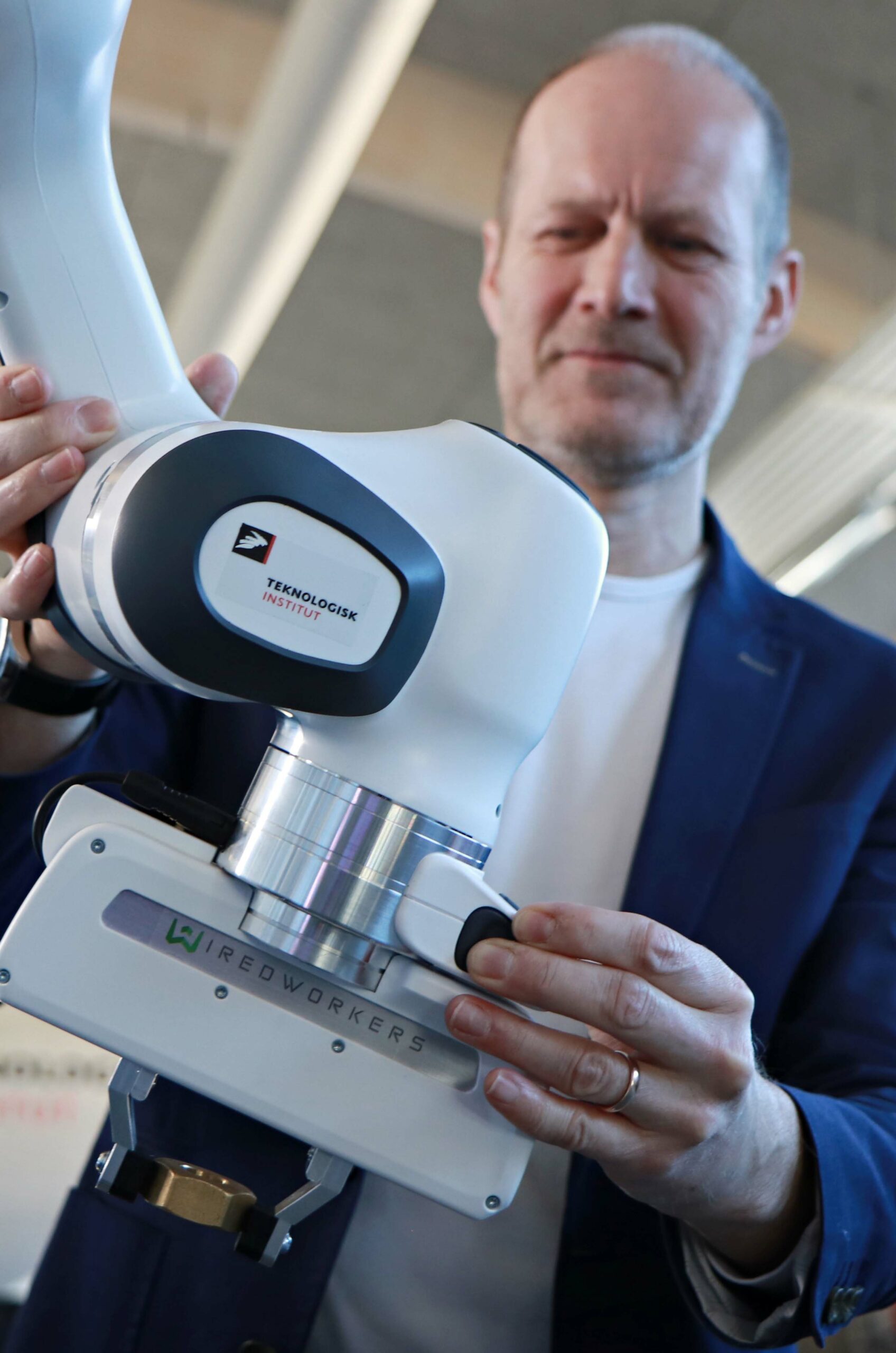
Business cases
Both companies that use cobots and those that do not lack inspiration. "We lack inspiration. We have also considered using cobots for assembly, for example. It would be interesting to see how others have done it," said one of the respondents. As a result of the lack of inspiration, many companies find it difficult to put together an interesting business case. In addition, the purchase of a cobot often involves an investment request with certain payback requirements. For many companies, it is difficult to meet these requirements or to demonstrate them in advance, for example because they produce small batches. An automation expert can help make a good ROI calculation and list all the returns.
Culture
A lack of innovation capacity and challenges in making interesting business cases are not the only reasons for not investing in cobots. In some cases, it is the whole company culture that is challenging to innovate and invest in cobots. This may have to do with a conservative way of thinking and the way innovation is given a place within the company. "We actually only have one person working on innovation and he is also responsible for production." In addition, staff may not want to go along and feel more comfortable with old patterns. Therefore, many companies are concerned about the resistance that the implementation of a robot may cause. Workers often see the arrival of a robot as a replacement and thus the end of their job. There are also employees who say they do not want to work with robots. "The day I have to operate a robot, I will no longer be here," said a welder from a small manufacturing company. Communication with the staff is essential here.
Time
Finding the time to start testing new technologies is a problem for almost all companies. Large companies often have a department separate from production to set up this type of innovation, but for small companies this is often not the case. Several companies also point out that the time and support they receive from management is not enough to make implementation successful.
Experiences of cobot users
A number of companies that are now using a cobot find that the technology is more complex than expected. They have encountered problems with the integration, which has taken longer than expected. This is mainly because the cobot is integrated into existing production. The cobot must be linked to other machines, which increases the complexity.
The regulations surrounding safety also make it complex. When companies start integrating, the biggest challenge is to make a cobot work profitably and at the same time comply with safety legislation and regulations. Speed is also a challenge. The speed of a cobot is less than that of traditional industrial robots.
We, WiredWorkers, often come across the above experiences when we embark on an automation project with a customer. Yet these challenges can be overcome. Before we start implementation, an extensive feasibility study is carried out. In this study, we look at all aspects concerning communication with other machines, safety and what automation will ultimately yield in terms of money, but also in terms of quality and employee satisfaction.
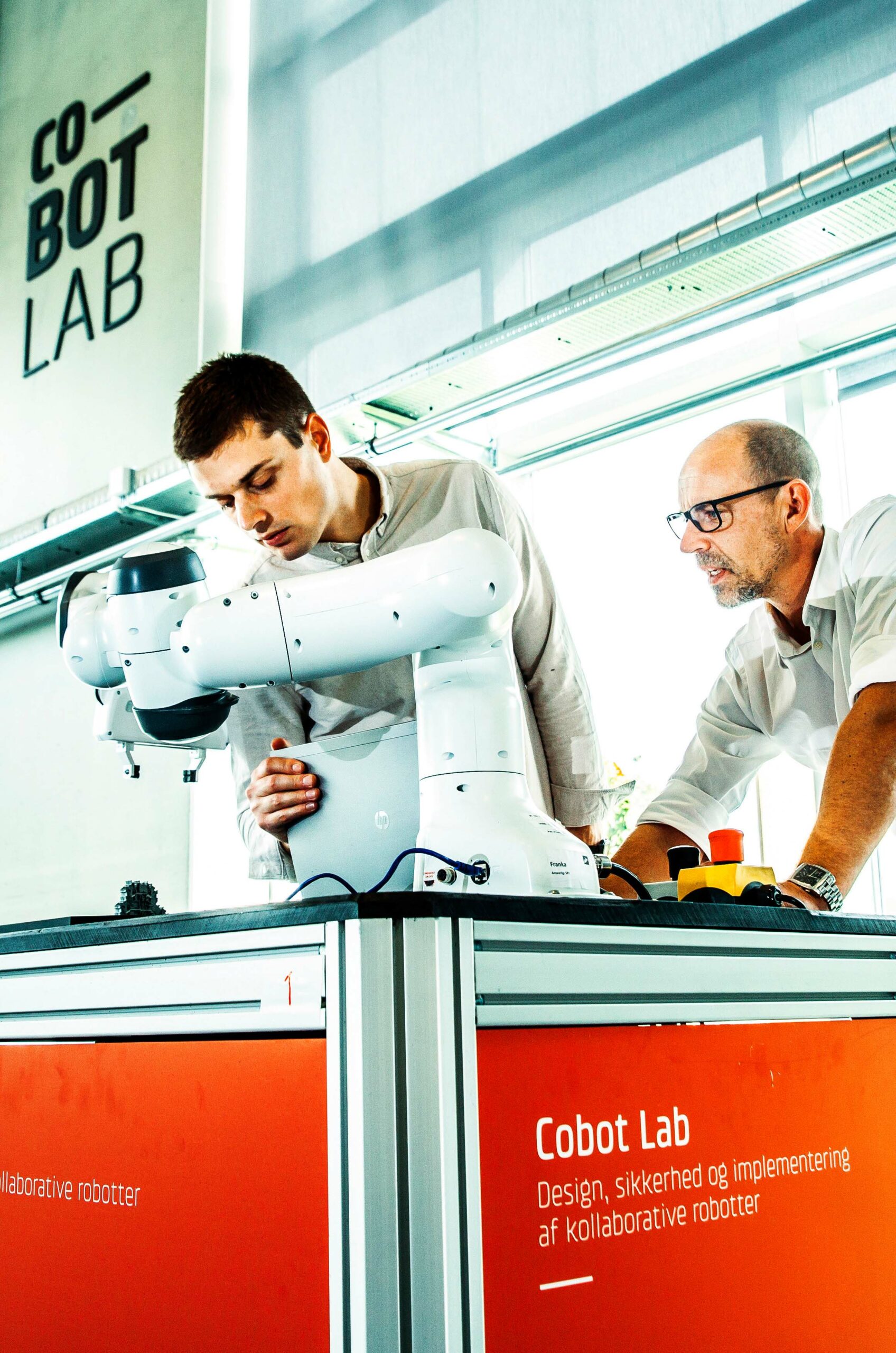
Points of attention for businesses
It is quite clear. The implementation of a cobot involves many aspects that make successful cobot automation a challenge. Yet this doesn't have to mean that you should give up beforehand. Companies that have already started have realised the first benefits in terms of improved throughput, better working environment, higher quality, financial gains or valuable lessons about automation. What also became clear is that for some companies it is the way to stay competitive. Doing nothing may be worse for the future of the company. Below are a number of important lessons from the study that both the manufacturing and the automation industry should pay close attention to before starting an automation project.
New partnerships essential for success
It became clear from the research that a successful cobot implementation involves existing knowledge, experience and resources in the company. It is therefore important to look closely at the resources you have and to what extent external help is needed. As companies build skills internally, the need to bring in external partners becomes less or can increase the complexity of projects. In addition to external partnerships, it is also important to look at internal collaboration. A cobot implementation has multiple stakeholders, from production and maintenance to safety and HR. Make sure they are all involved in the process up front.
Dedicated staff can show the way
Successful cobot implementation requires dedicated staff. However, they also need the input and recognition of a number of other employees for their hard work to result in success for the company. Often, the project team working on cobots is staff with other responsibilities. As a result, the cobot project quickly gets put on the back burner. The internal project management of cobot projects is crucial to achieving a successful result. It is also important to involve staff in the process. Communicate a common goal so that employees know why an automation project has been chosen, for example to save production from mind-numbing work.
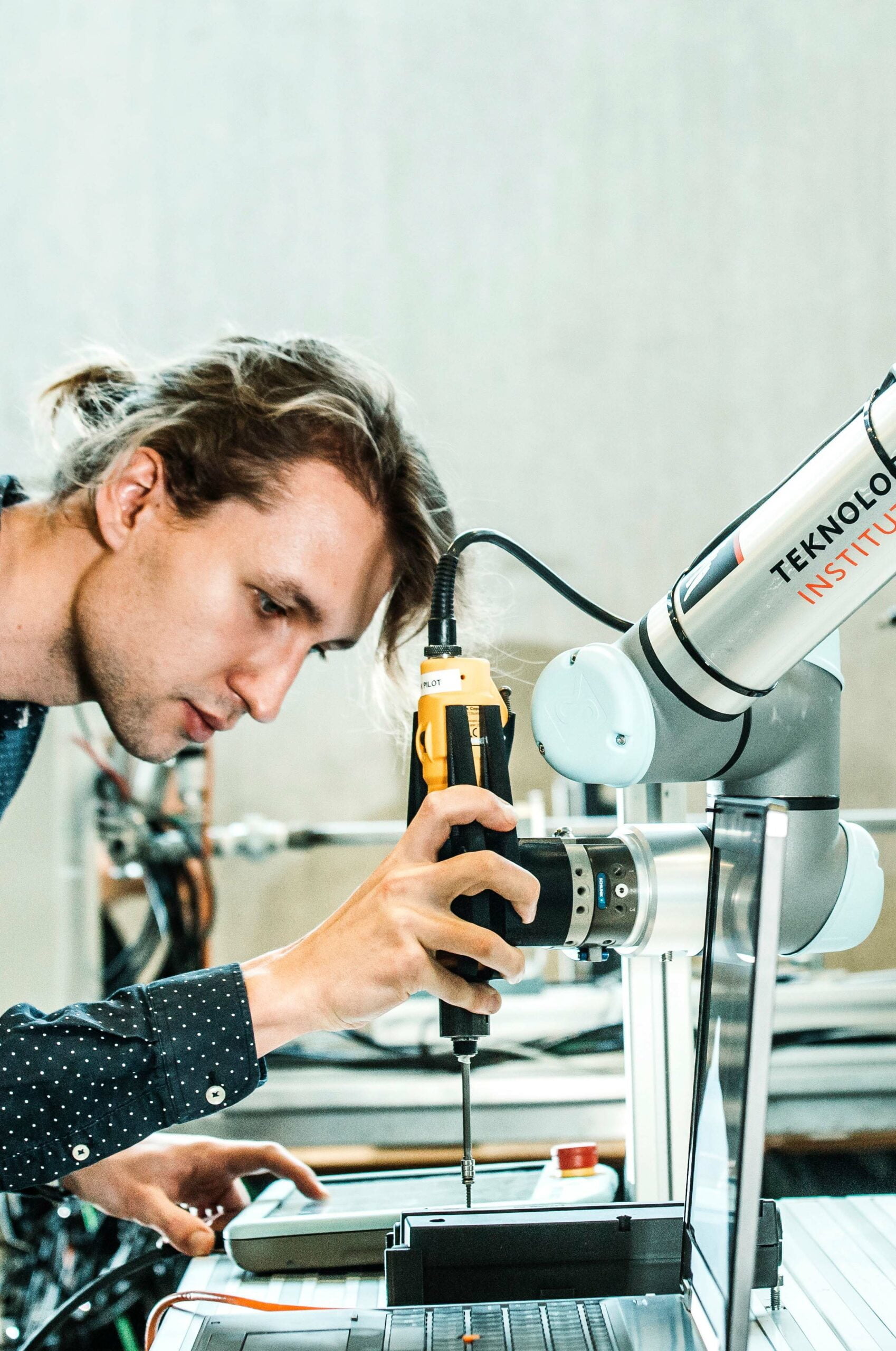
Not just plug-and-play
Since the complexity of each company's production systems varies greatly, the complexity of integration also varies. During this process, new uncertainties and unknown factors constantly arise, which the project team has to deal with. The automation of seemingly simple processes that were once carried out by people may require relatively technical solutions, tests and evaluations . So, take your time for an automation project and try to map out everything in advance to avoid surprises.
Cooperation between humans and cobots
Cobots differ from traditional industrial robots in that they can be integrated into production systems in close proximity to workers. In general, cobots are seen as a means of improving the quality of workers' jobs, as they can help reduce the amount of one-sided repetitive work. So, in addition to the technical aspects of cobots, there is also a human aspect to the functions and well-being of workers. Think carefully about how a cobot can help increase employee motivation and job satisfaction.
New skills, training and courses
Cobots are a new technology that places new demands on the skills of employees. The acquisition of new skills often takes place informally during the implementation process, but companies can often benefit from external training. The introduction of cobots almost always involves a change in existing processes and the need for employees to acquire new skills. It is important to determine in advance what skills employees need to acquire and what is the best method for doing so.
Get to work!
In short, make sure that clear, well-defined considerations are made prior to an implementation project. Does it have to be financially profitable or is the goal to be ready for future changes? Clearly defined and delineated projects facilitate the learning process and can count on a faster ROI.
At WiredWorkers, we strive to create a world where the qualities of employees are fully utilised, and are happy to help make the implementation of cobots as successful as possible. Want more information? Are you curious about how a cobot can be used as effectively as possible in your company? Contact us!