Automating processes within manufacturing can have a lot of impact on overall operations. Not only will production efficiency improve, it can also help reduce costs and improve quality. The big question then is; are the costs commensurate with the value that automation can bring? And how does automation compare to other options such as hiring additional staff or outsourcing tasks. So it is important to weigh the costs and benefits beforehand, but what exactly does cobot automation cost?
What is the cost of automation?
For many companies, cost is the most important factor when choosing an automation solution. To properly consider the actual cost, it is important to consider two categories; start-up costs and maintenance costs.
The start-up cost of an automation system consists of all costs incurred before the system is operational. Consider materials such as the robot, grippers or other tooling, frames, sensors, safety devices, as well as all the hours that go into designing and realizing the system and training the operators.
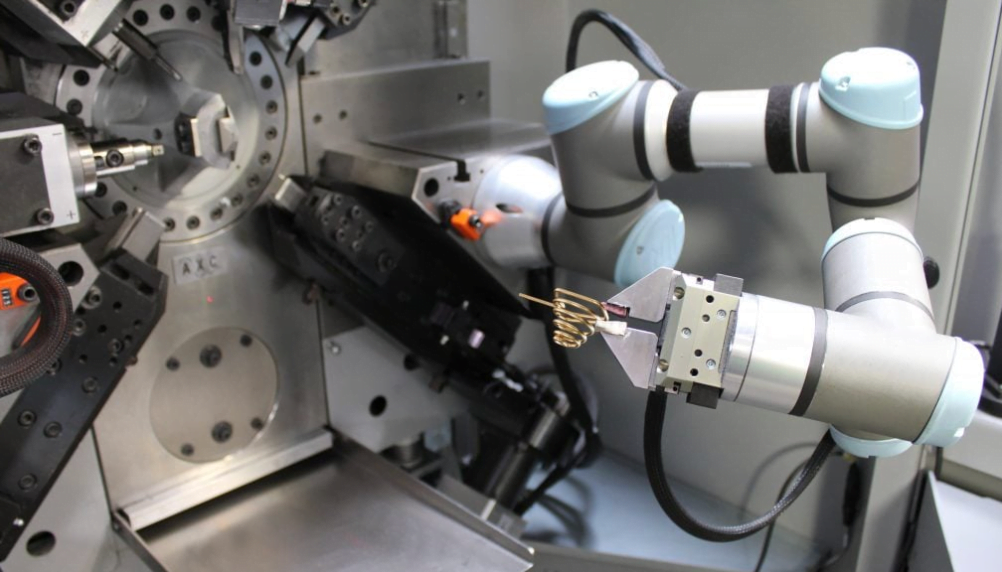
Maintenance costs depend on the type of system. Common maintenance costs include parts replacement, software support and/or upgrades, labor hours for maintenance and repair, electrical or pneumatic power to operate the system and preventive maintenance.
What does automation provide?
As great as the cost of automation is, the idea is that the robotic system provides more value than was invested in it. For many manufacturing companies, the added value is in streamlining production, simplifying quality control and improving consistency. Because robots can work 24/7 without breaks, productivity will also increase.
The simplest and most useful way to determine the value of automation is to calculate the return on investment (ROI). In other words, the time it takes to recover the cost of the investment. Below is an example of an ROI calculation.
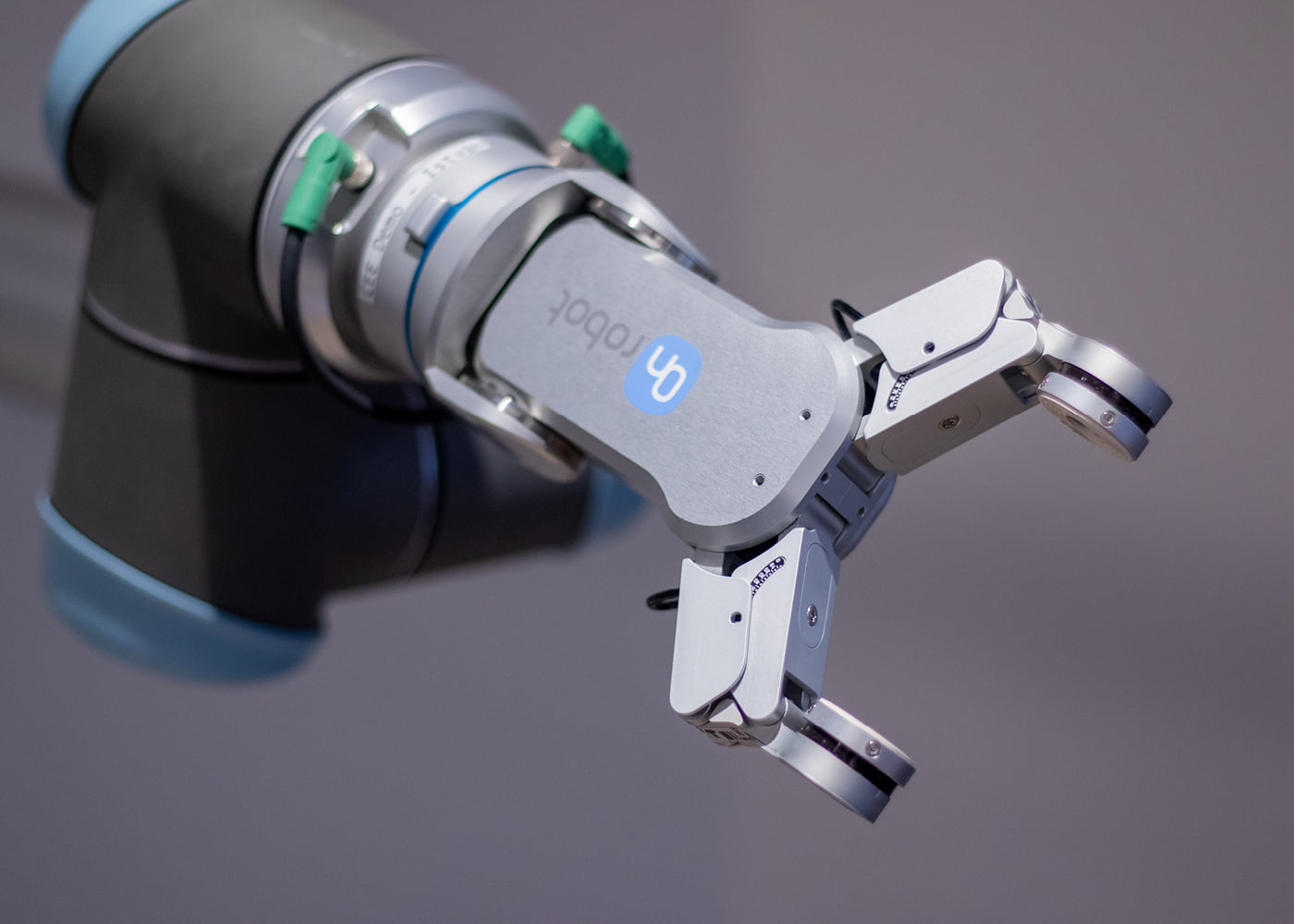
For the calculation example, we calculate with two shifts for loading and unloading a CNC machine. The labor cost of one person is €40,000 per year. Now suppose the employer chooses to automate the loading and unloading of the CNC machine with a €60,000 Machine Tending Solution. To calculate the ROI, we divide the cost of the robotic system (€60,000) by the total labor cost per year (€40,000 per person, total €80,000). The ROI in this case is about three quarters of a year.
Other methods to cut costs
Obviously, automation is not the only way to reduce costs. There are many other methods that save time, money or energy within the organization. Consider reducing overtime (to save hourly wages), streamlining the process, increasing product prices, reorganizing or reducing production quality. All are effective ways to reduce costs, but likely to be problematic for the company in the longer term because it will reduce value for money.
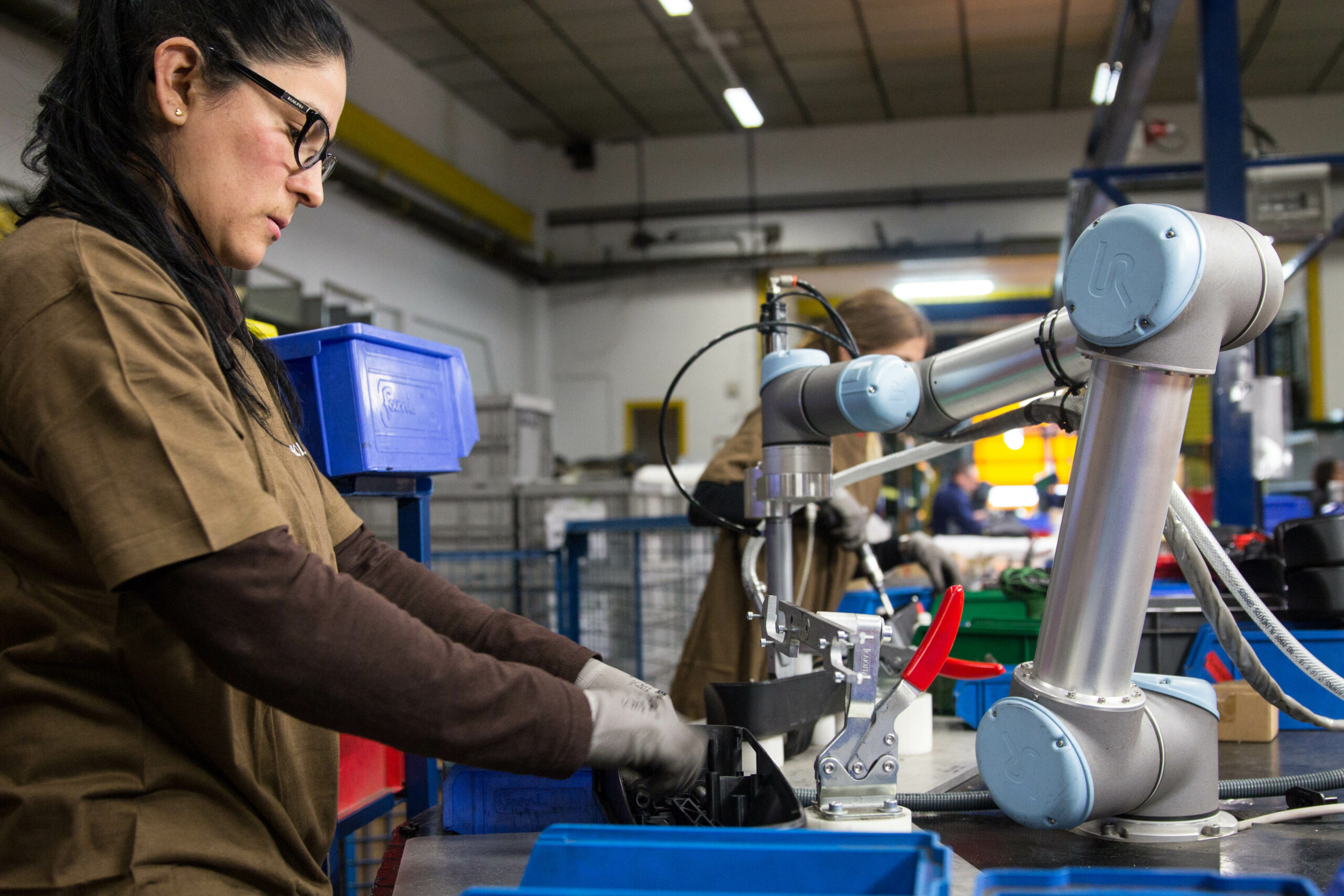
Automation vs. outsourcing
A common alternative of automation is outsourcing or outsourcing. This means that companies choose to have the work done more cheaply by an outside party, such as in a country where wages are somewhat lower. This, on the other hand, comes with some disadvantages.
For example, it is difficult to find reliable suppliers who can deliver good quality for a long period of time. With in-house production, it is easier to control and maintain quality standards. Also, with outsourcing, macroeconomic events (such as the recent pandemic and Suez Canal congestion) can cause problems. Local production is less dependent on this. In addition, there is simply less control over activities and processes that take place away from home.
Robots vs. people
In addition to automation, it is also possible to hire more people and thus increase productivity. This can be a good alternative, were it not for the fact that in most industries there is not a ready supply of workers ready to start immediately. Labor shortages are a major problem for many manufacturing companies around the world. Therefore, hiring will be increasingly expensive and difficult to achieve.
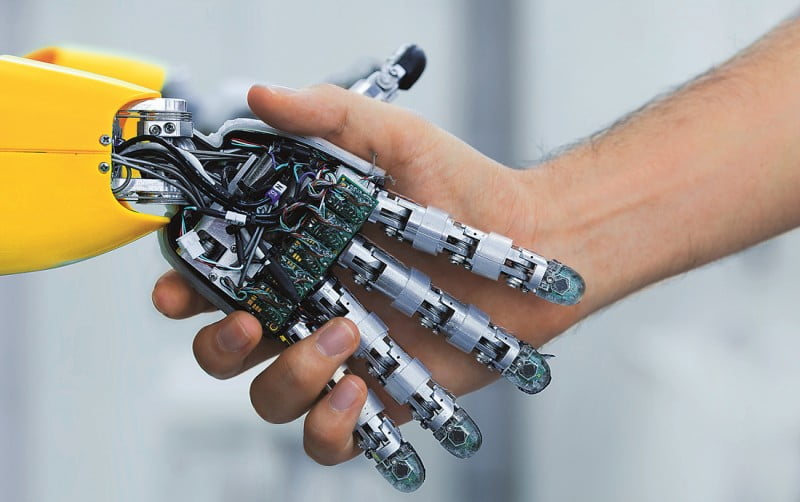
Is the cost of automation really worth it?
Automation can add significant value to businesses. It can help companies reduce costs and maximize the value of their human employees. It is important to consider the costs, benefits, risks and rewards. If all of these are carefully weighed, the chances of success only increase.
WiredWorkers is an expert in automation and has already helped several companies implement automation systems. We can help calculate a clear cost estimate and ROI. Contact us or schedule a free cobot consultation!
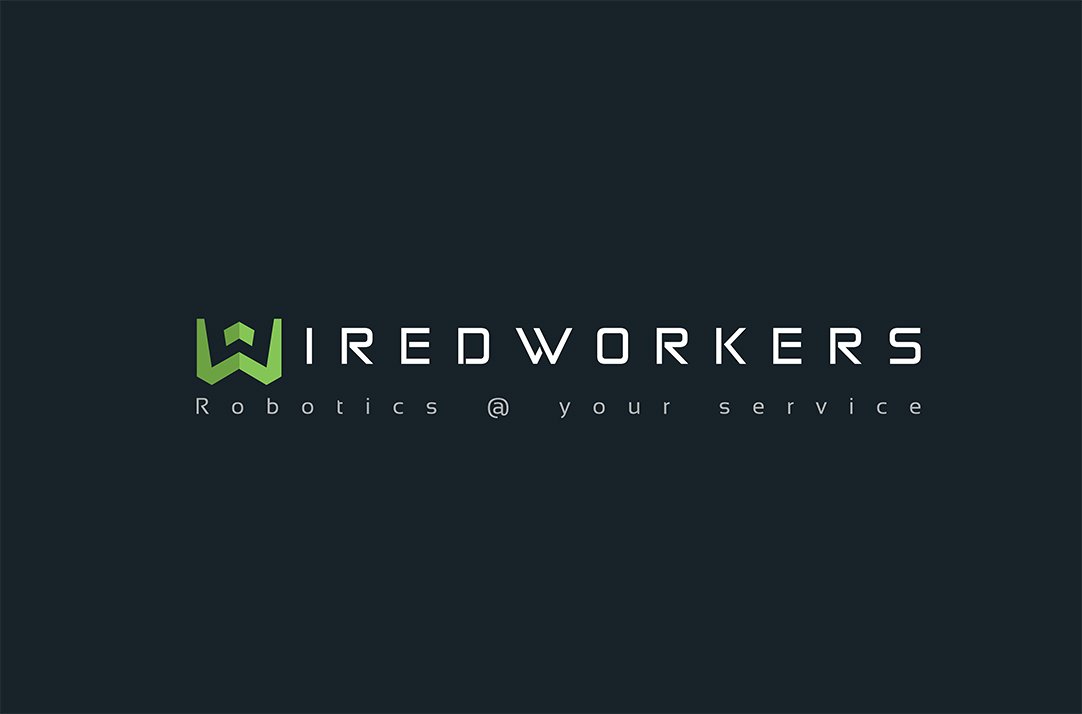
Frequently Asked Questions
What are the specific costs associated with implementing and maintaining an automated system, such as a robotic solution, and how can these costs be optimized?
The specific costs associated with implementing and maintaining an automated system, such as a robotic solution, vary depending on several factors. These costs typically include the purchase cost of the robotic arm and any associated equipment, costs for software, integration and training, as well as ongoing maintenance and energy costs. Optimizing these costs can be achieved through a thorough analysis of the company's needs, choosing the right robotic solution to fit the requirements of the application, and investing in preventive maintenance and training to maximize equipment life and improve operational efficiency.