Automation as an answer to labour shortage
As an established name in the food industry, Boermarke values quality and efficiency, both in its product range and in its internal processes. However, as in many manufacturing companies, Boermarke is facing challenges due to labour market shortages. This creates an increasing need to automate repetitive tasks and relieve employees. A crucial step in this was the implementation of a custom-developed palletizer in collaboration with WiredWorkers.
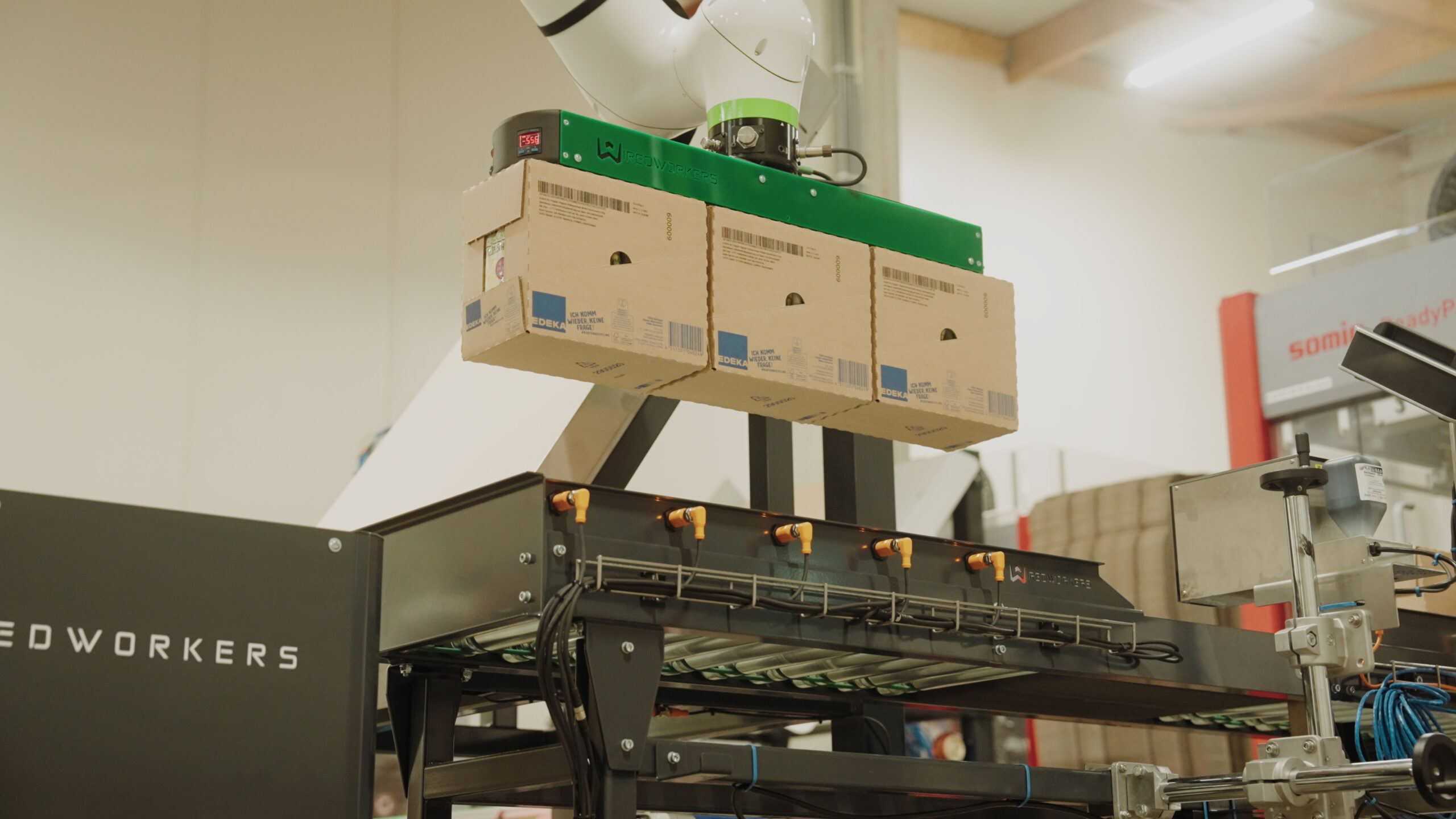
A reliable, cost-effective and simple system
At the end of Boermarke's production line, operators were responsible for stacking boxes on pallets. Quite repetitive work that took up a significant amount of their time. With labour market shortages and a desire to increase productivity, it became clear that automation of this process would not only improve efficiency, but also the work experience for employees. So the challenge was to find a system that was reliable, cost-effective, and simple, without the complexity and rigidity of large, unwieldy installations.
The solution: an efficient Cobot Palletizer
The final solution was an automated cobot palletizer with a Fanuc CRX25iA and a customised gripper capable of picking up all types of box variations. A roller conveyor was built in front of the palletizer with a printer from de Koningh providing each box with a unique barcode. The robot is controlled by Boermarke's MES system, reducing operator errors.
Thanks to the palletizer, operators no longer have to manually stack boxes, making these repetitive tasks a thing of the past. Thanks to the cobot's accuracy, boxes are always stacked the same way, exactly as the customer wants them. Watch the video below to see the Palletizer in action.
The implementation process
The implementation process of the palletizer went smoothly. From kick-off to final installation, the two teams worked closely together, with WiredWorkers continuously suggesting improvements and innovative solutions. Instead of highlighting potential obstacles, the focus was on finding practical solutions. This led to an efficient, trouble-free installation.
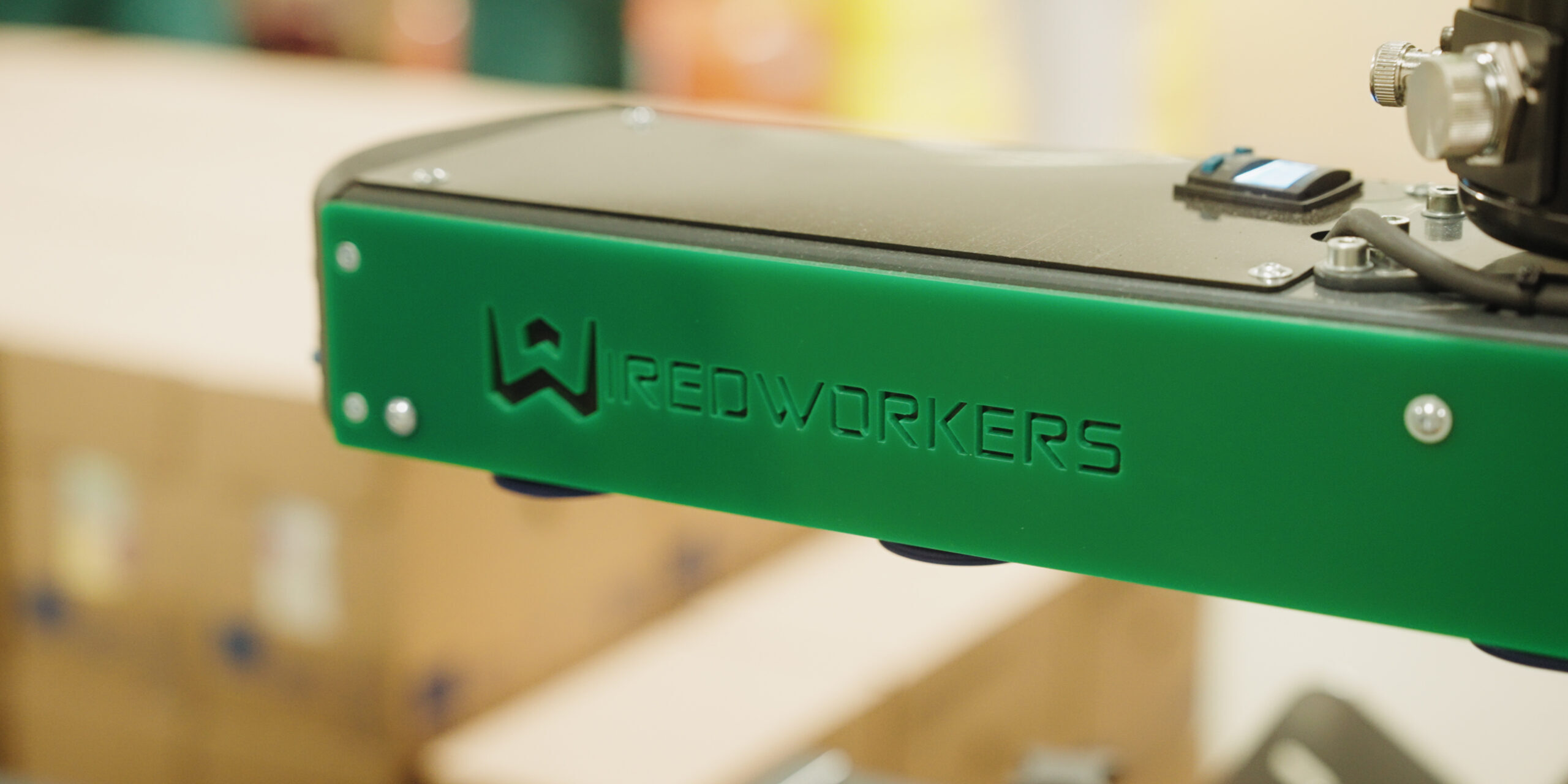
A great result of a pleasant cooperation. Marcel Olde Olthof, production manager at Boermarke describes WiredWorkers as true problem solvers who think beyond the basics. 'WiredWorkers truly solves customer problems by thinking beyond what is written on paper,’ says Marcel.
Cost savings and improved working conditions
Automation has brought tangible benefits to Boermarke. First, it has reduced staff costs: where previously four employees were needed to manage palletising on two lines, now one employee is sufficient to put away pallets and put back empty pallets. This has led to significant cost savings and additional capacity within the team. In addition, the palletizer has improved employees' working conditions by reducing the number of repetitive operations, thereby improving ergnomy, motivation and satisfaction.
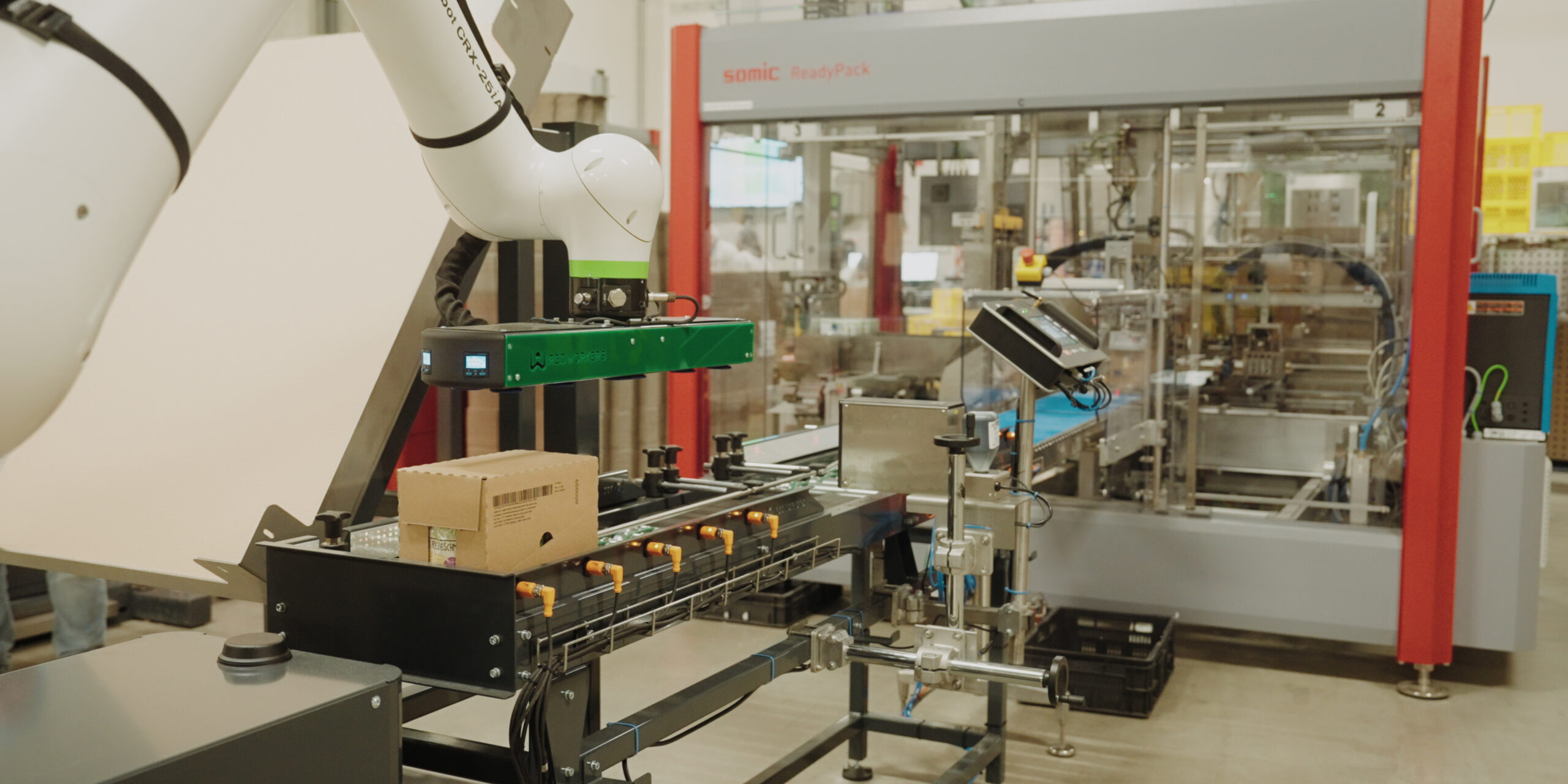
Where previously four employees were needed, one employee is now sufficient to put pallets away and put empty pallets back.
The collaboration between Boermarke and WiredWorkers shows how automated solutions can contribute to productivity improvements, cost savings and higher employee satisfaction. Implementing the palletizer proves to be a good solution for companies looking to respond to labour market shortages and optimise production efficiency. Wondering how we can maximise your production? Contact us or book a free consultation.