Low Cost Intelligent Automation
Ubbink has been replacing its lean lines with LCIA (Low Cost Intelligent Automation) lines since early 2020. LCIA serves as an optimal combination between man and machine. The strengths of machines are that they can perform a repetitive task accurately without getting tired. Humans are able to observe the process, detect errors, and it can be more cost-effective to have humans perform individual handling tasks. Human performance is central to the design of LCIA lines.
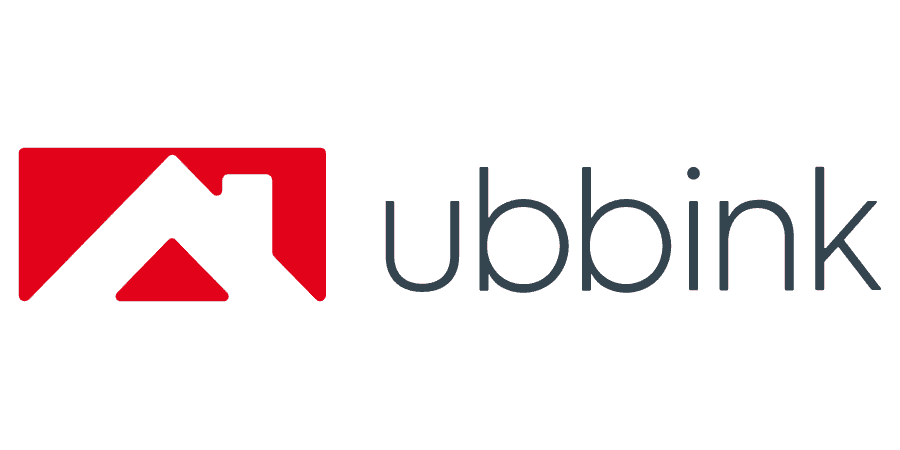
P&P Box Erector Solution
One of those LCIA lines includes our Plug&Produce Box Erector. The focus of this solution is in its flexibility. It is designed to handle both large and small box sizes, it is movable, and thanks to its sensor, it sets up boxes on-demand. As a result, the box erector functions as a modular block in the LCIA cell.
Ubbink had used box erectors in the past, but these were unable to set up both standard small boxes and new large boxes, which WiredWorkers' box erector can do. The box erector was also needed because the large boxes at Ubbink are not manageable according to health and safety regulations, especially in the large numbers in which Ubbink produces.
The Automatic Box Erector is an in-house developed Plug & Produce solution. With a self-designed gripper, he grabs the boxes from the storage bin. He then folds the box with his gripper and the folding track developed for this purpose. He then slides the boxes over a tape module to the end platform, where they can then be removed and filled. Watch the video below to see how our box erector works.
Increased productivity and employee satisfaction
The implementation of LCIA and the box erector resulted in a significant increase in productivity in the department. For example, 1 to 1,5 FTEs have been saved. This shift has not only the employees from a monotonous task, but has also allowed them to tackle more complex responsibilities, such as quality control and analysis. Consequently, this shift in responsibilities has led to greater employee satisfaction and contributed significantly to their overall well-being.
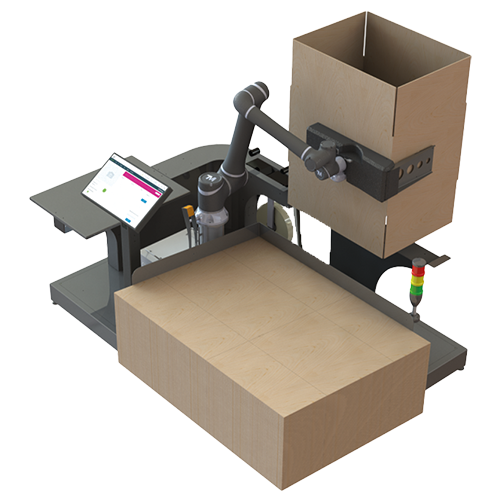