The problem: no qualified personnel
As mentioned, Signify supplies lighting in all shapes and sizes to businesses and consumers. One of the products made are metal light boxes that are hung in subway tunnels, for example. The quality of these boxes is very important. For example, the welds must be dust and water tight.
In the old situation, the process consisted entirely of manual work. An operator grabbed the part, checked if the corners were connected enough to weld. A weld seam was applied to all four corners, which was then finished manually.
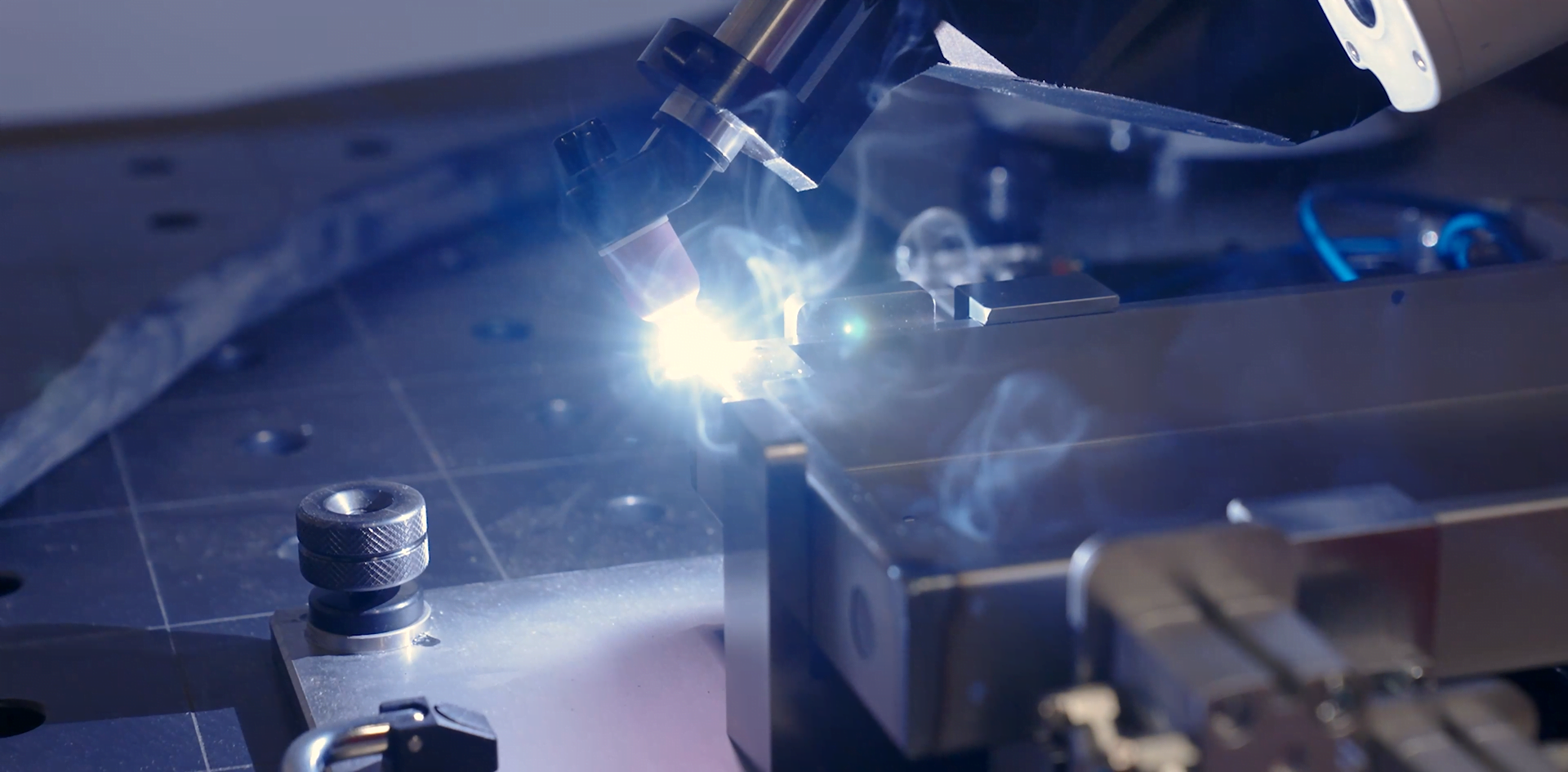
The problem that is common in the industry is the lack of the right personnel. Within the Dutch labor market there is a great shortage of welders, so it was difficult for Signify to find the right people for this job. In addition, the process is fairly heavy and monotonous, making it increasingly difficult to continuously deliver the desired quality. To avoid this, Signify opted for a welding robot to automate the process.
The solution: an automated welding cobot
In the new situation, the operator places the light box in the welding jig. There, that presses a two-hand control with which the welding jig clamps the light box. Visually, the operator checks that the light box is properly positioned in the mold. Then the operator walks outside the safety zone to start the welding process on the touch screen. To protect the environment from the harmful UV radiation of welding, the cell automatically closes a safety screen before the robot starts welding. Watch the video below to see how the process works!
Yield: Continuous high quality and improved productivity
The deployment of the welding cobot has brought a number of benefits to Signify's welding process. For example, unlike a human welder, the cobot can continuously lay welds of the same high quality. This is because the cobot always performs the process at the same speed and with the same accuracy.
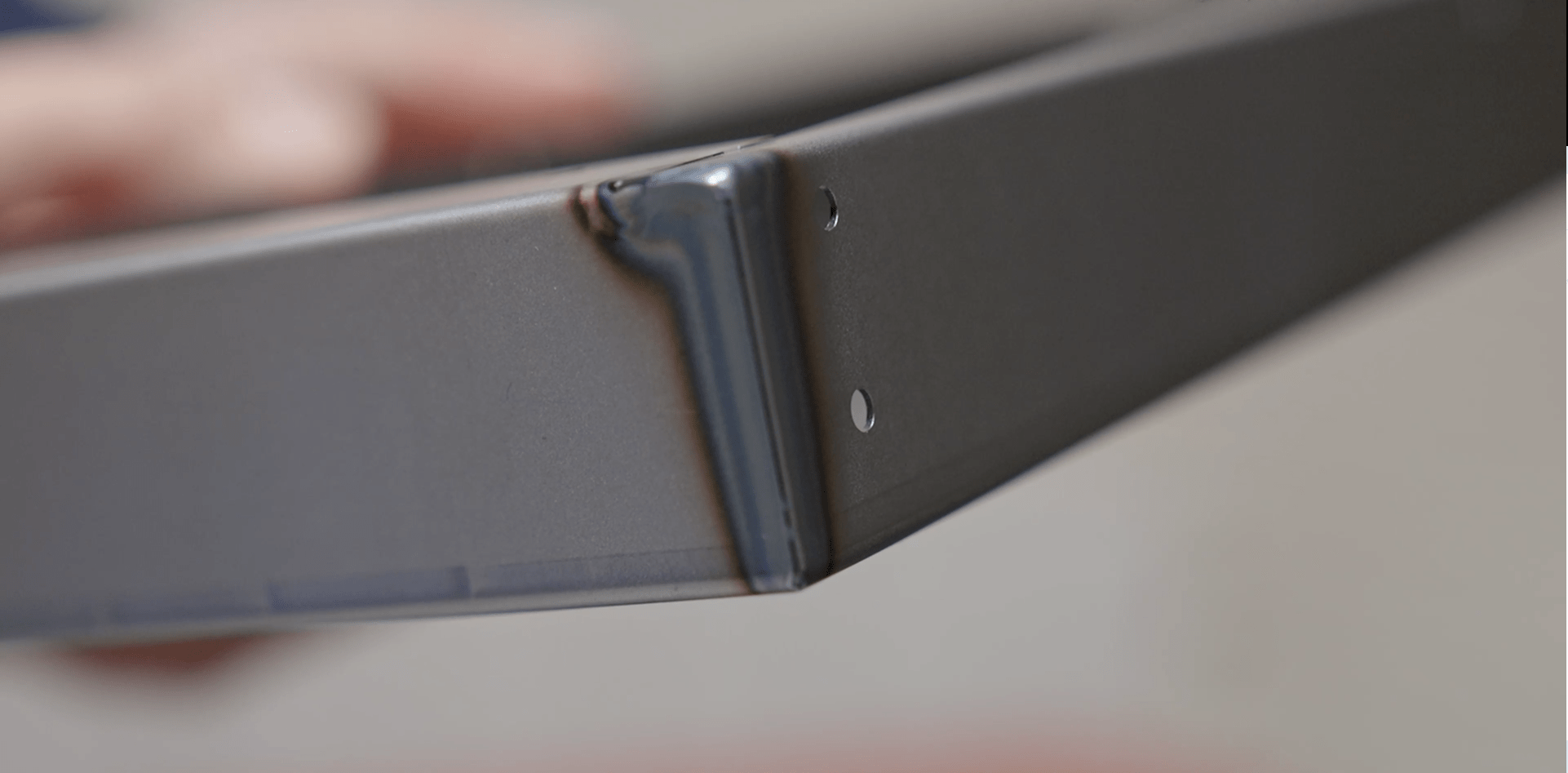
Another advantage is that the operator supervising the welding process does not have to be a qualified welder. As mentioned earlier, there is a great shortage of welders in the Netherlands. By automating the welding process, it is easier to find personnel for the job, without the welding process losing quality. In addition, thanks to the robot, productivity has also increased. The welding robot lays down a perfect weld seam, which requires no post-processing. After the robot has completed the process, the product can proceed directly to the next department.