Screwing with a collaborative robot
Cobots are a good solution for automating screw processes. There are various screwdriver tools that a cobot can work with, and thanks to the built-in sensors, screws are tightened very precisely and with the right force. Most collaborative robots are accurate to within 0.1mm, and because the same force is always used, the quality of the final product is always very consistent. In addition, cobots are safe robots and can cooperate with people. If the cobot comes into contact with workers it will automatically stop. If the person leaves the work area, the cobot will resume its work at full speed.
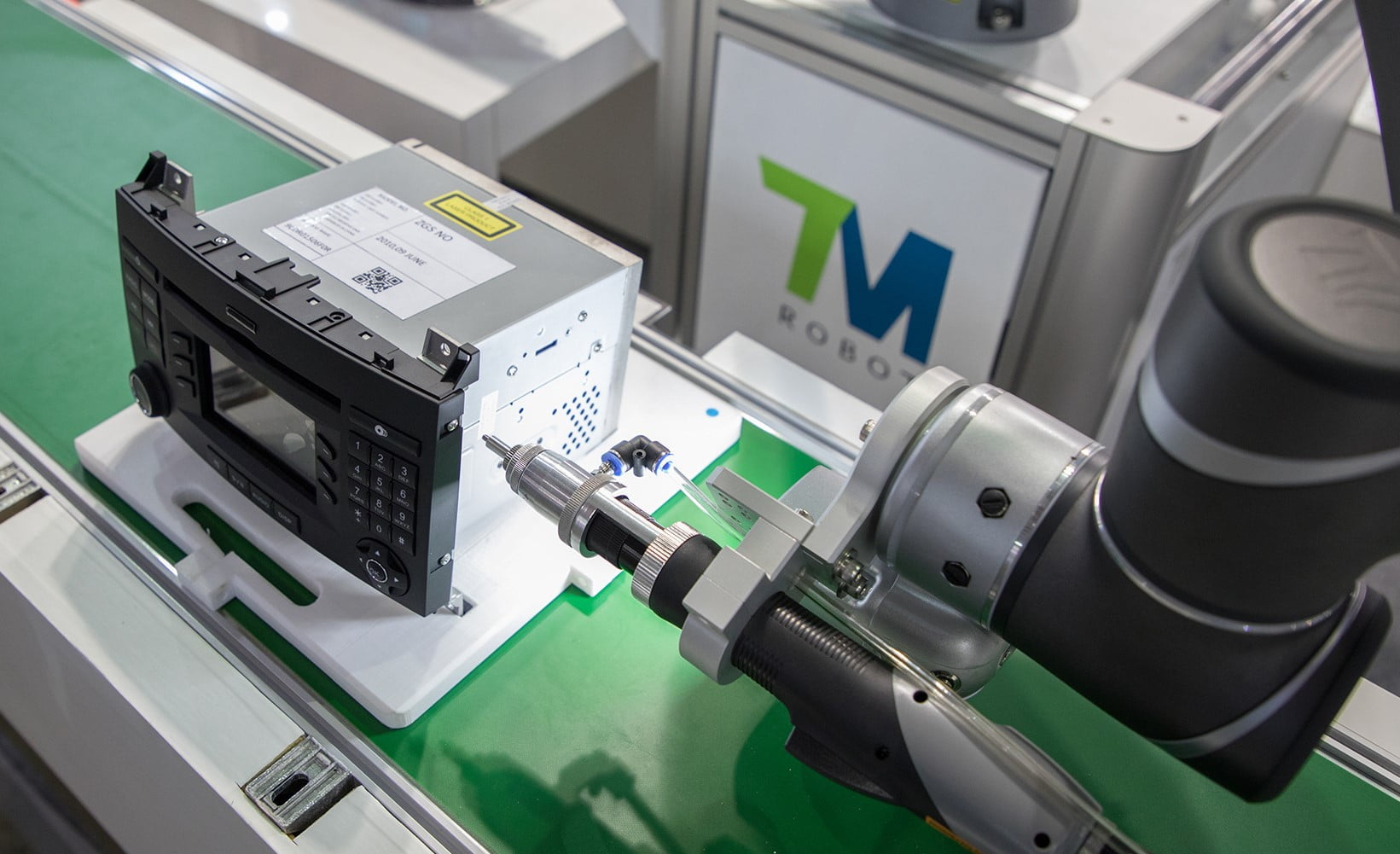
The great thing about a cobot, as opposed to industrial robots, is its flexibility. Thanks to simple programming interfaces and user-friendly software, a screw application is quickly set up and easy to convert. This is ideal in production environments where different products are often produced in small numbers.
Cobot screwdriving benefits
Saving of costs
You will save on personnel costs
Increasing productivity
Staff can do other work
Utilize full capacity
Get more out of your employees
Prevent disorders
Prevent disorders among employees
No loss of concentration
Robots will never lose concentration
Constant quality of output
Robots deliver consitent quality
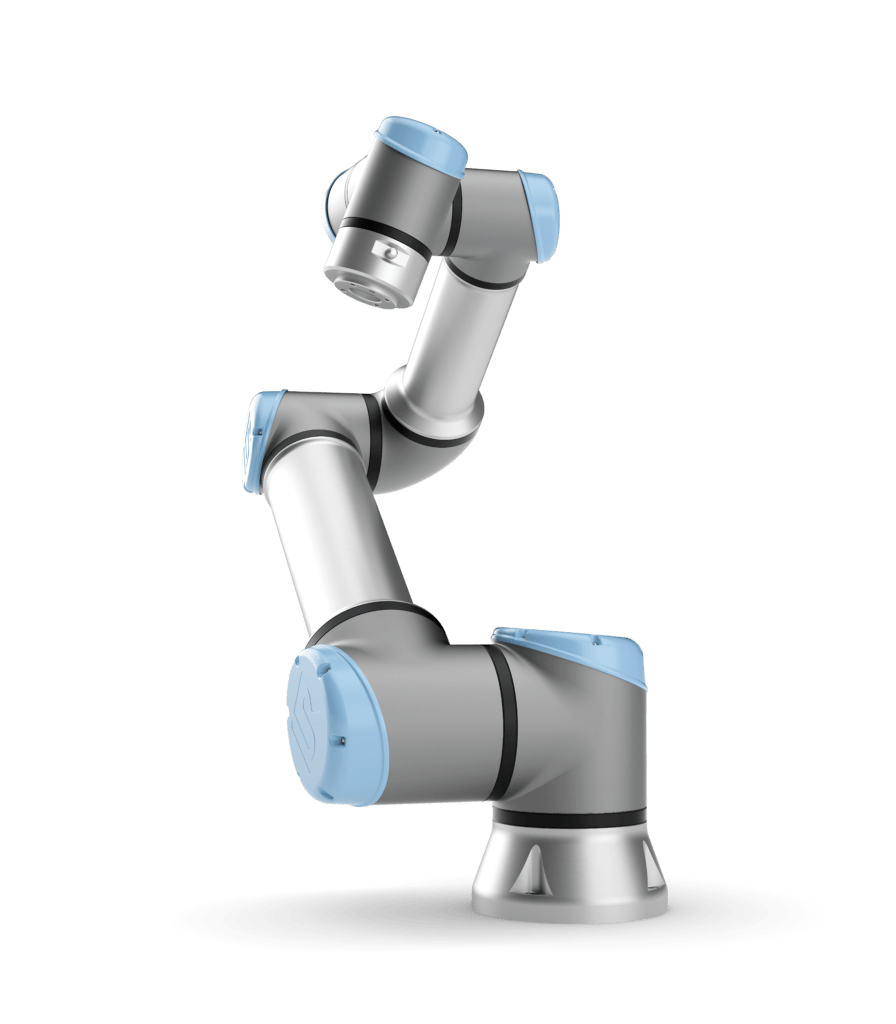
Relieve personnel of boring tasks
For workers, screwing objects is a boring, monotonous repetitive task. Keeping this up for 40 hours a week in a concentrated manner demands a lot from workers. In addition, screwing by hand carries health risks. Musculoskeletal disorders such as carpal tunnel syndrome can occur over time. By letting collaborative robots take over this work, sick leave is reduced and the quality of the final product improves. In addition, workers have their hands free to do other work.
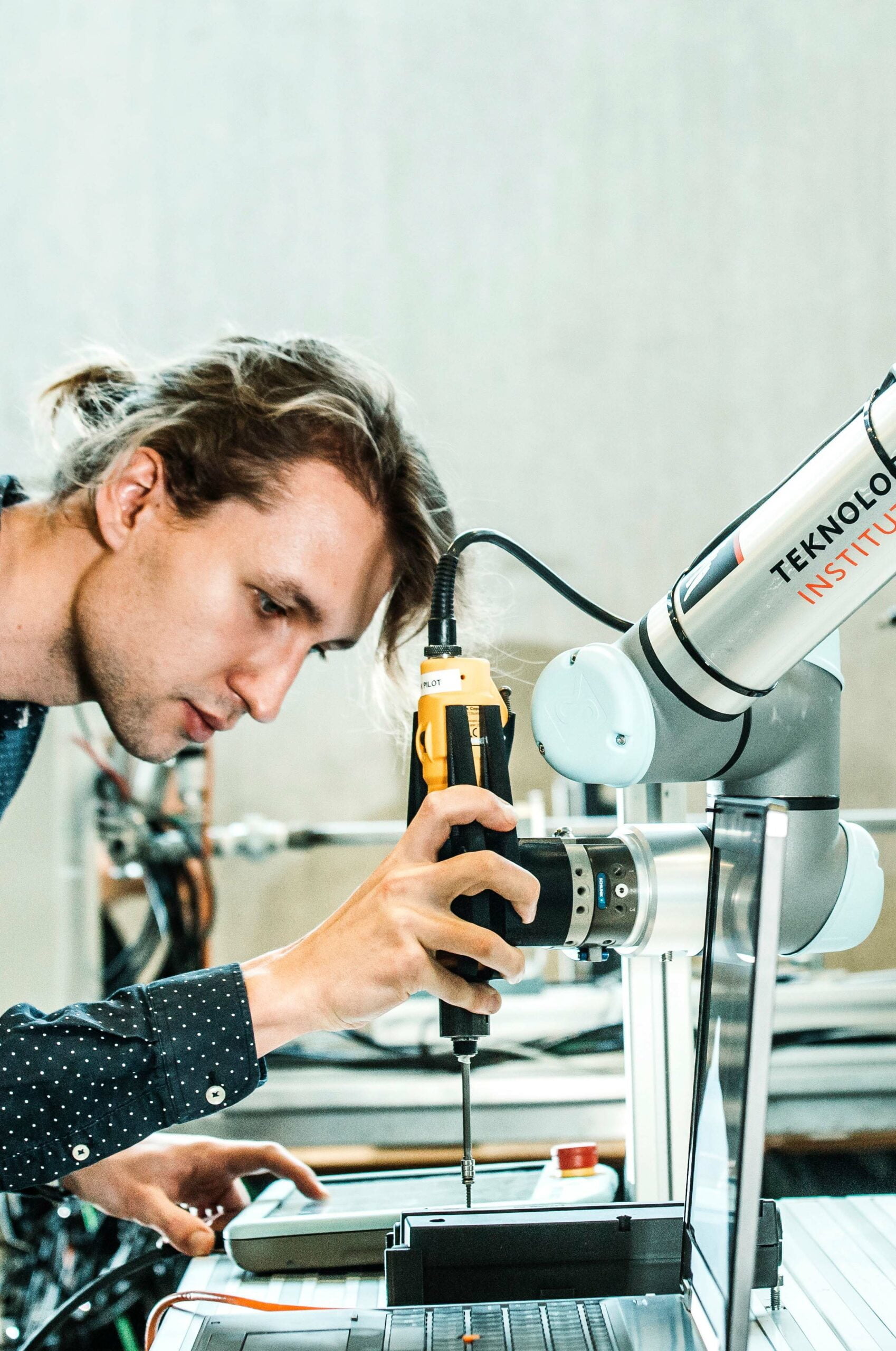
Cobot screwdriving video
Watch the video below in which a Universal Robot is working on a screwing application.