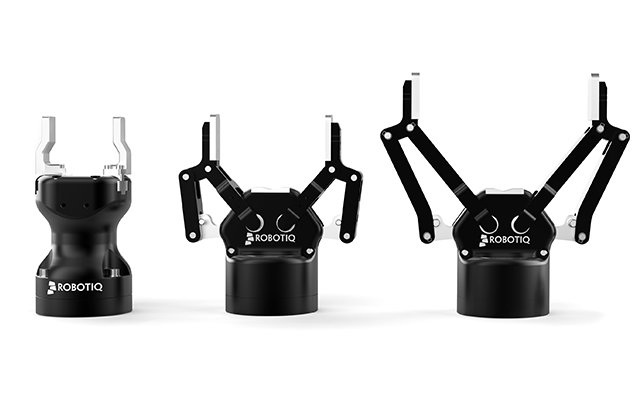
Grippers
The name really says it all. Grippers allow a cobot to pick up and move objects. There are many different types of grippers with their own characteristics. These include finger grippers, vacuum grippers, and magnetic grippers. The choice of gripper depends on the process being automated. Within the food industry, for example, soft grippers are common. Food is often fragile and hard grippers could damage the products. Vacuum grippers, on the other hand, are often used for picking up boxes in, for example, a palletizing task. Grippers also have their own specifications that need to be considered such as load capacity, gripping width and gripping force.
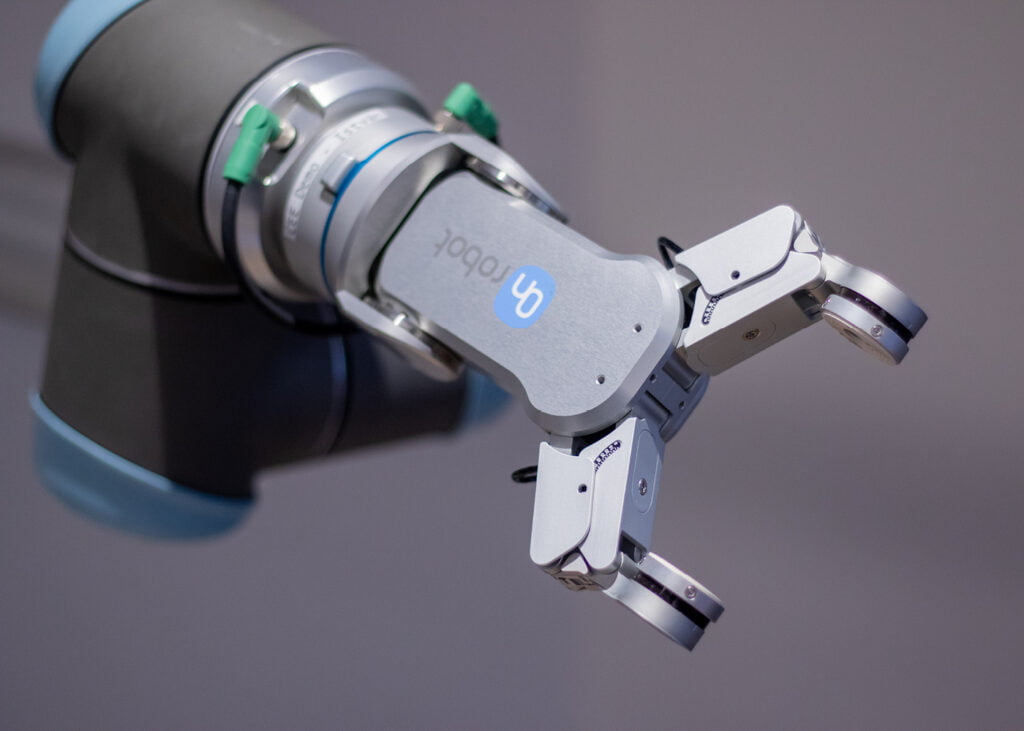
End of Arm Tooling
End of Arm Tooling (EOAT) stands for all kinds of tools that can be mounted on the end of a cobot (arm). Think of glue dispensers, screw machines, sanders, tool changers, sensors and welding and soldering irons. More and more companies have started to focus on developing EOAT in recent years, and the possibilities are growing. In addition, the tooling is easy to assemble and disassemble. This makes it very easy to have the cobot perform different tasks instead of doing the same job for longer periods of time. For flexible production environments, this means that a cobot is also a good investment in the long term.
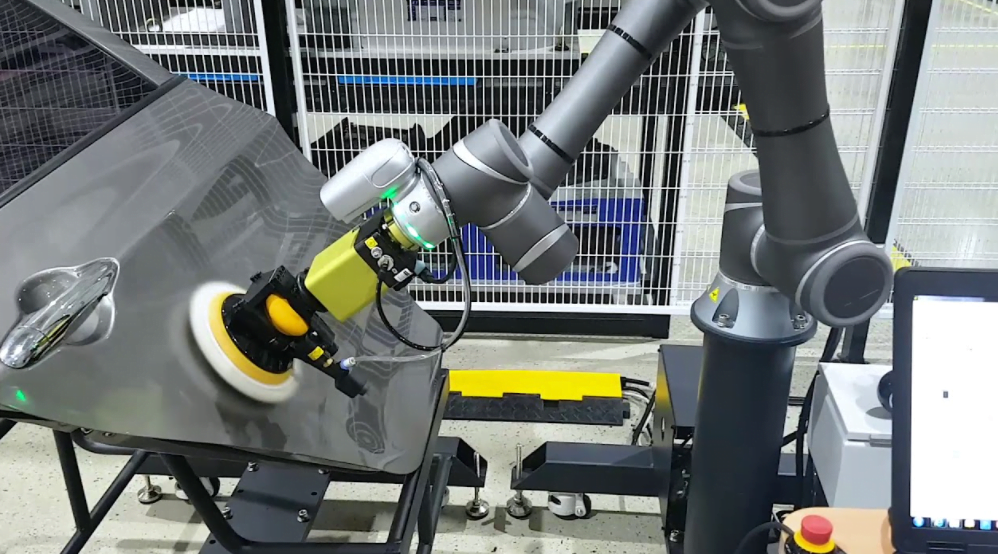
Tool changers
To make a cobot extra flexible, there are various automatic tool changers on the market. These tools make it possible for a cobot to change tools completely autonomously, allowing it to perform multiple operations. For example, within an assembly application, one cobot would first use a gripper to place all the parts in the right place, and then use a screwdriver to attach the whole thing. Ultimately, this increases the robot's productivity, generates more output and shortens its ROI.
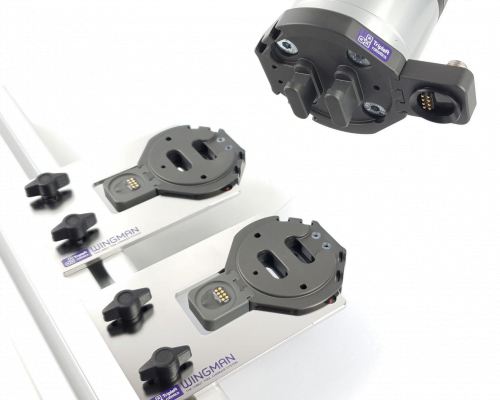
Vision
Vision systems give the cobot visibility. Thanks to 2D or 3D cameras, it becomes possible for collaborative robots to locate objects, recognize patterns or scan barcodes. Vision can make the integration process of a cobot much easier. Normally, robots need a structured supply of objects to be able to pick them up correctly. If a cobot can recognize and locate the objects, this is no longer necessary. In addition, vision systems enable optical control. So, you can check products for abnormalities. With the advent of Artificial Intelligence, the possibilities in this are increasing.
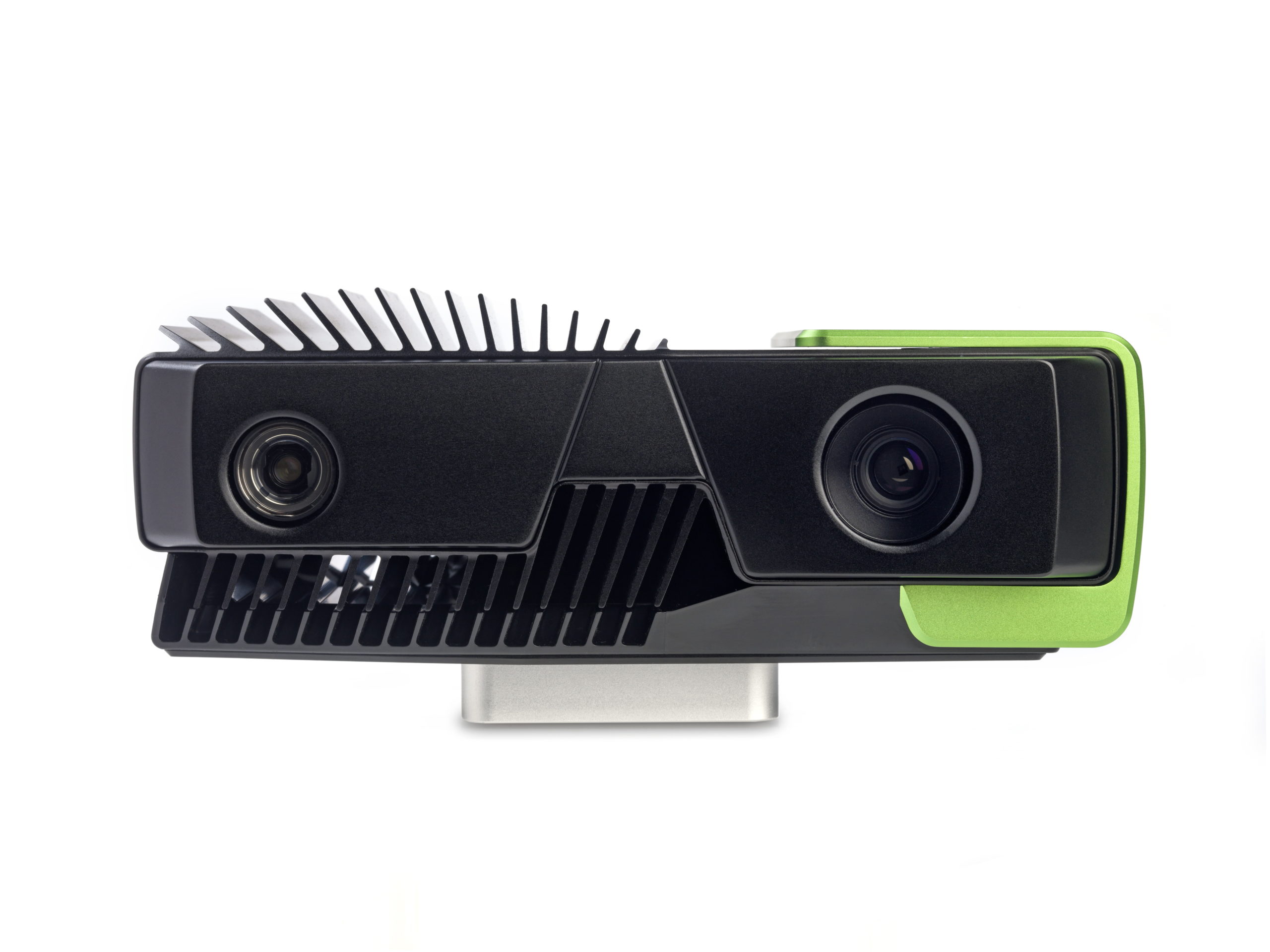
Software
A variety of software is available for programming and designing a collaborative robot application. Each cobot has its own intuitive, user-friendly programming software that allows the robot to learn new tasks easily and quickly. In addition, simulator software is available that can be used to design a solid robot integration before proceeding to the realization of the project.
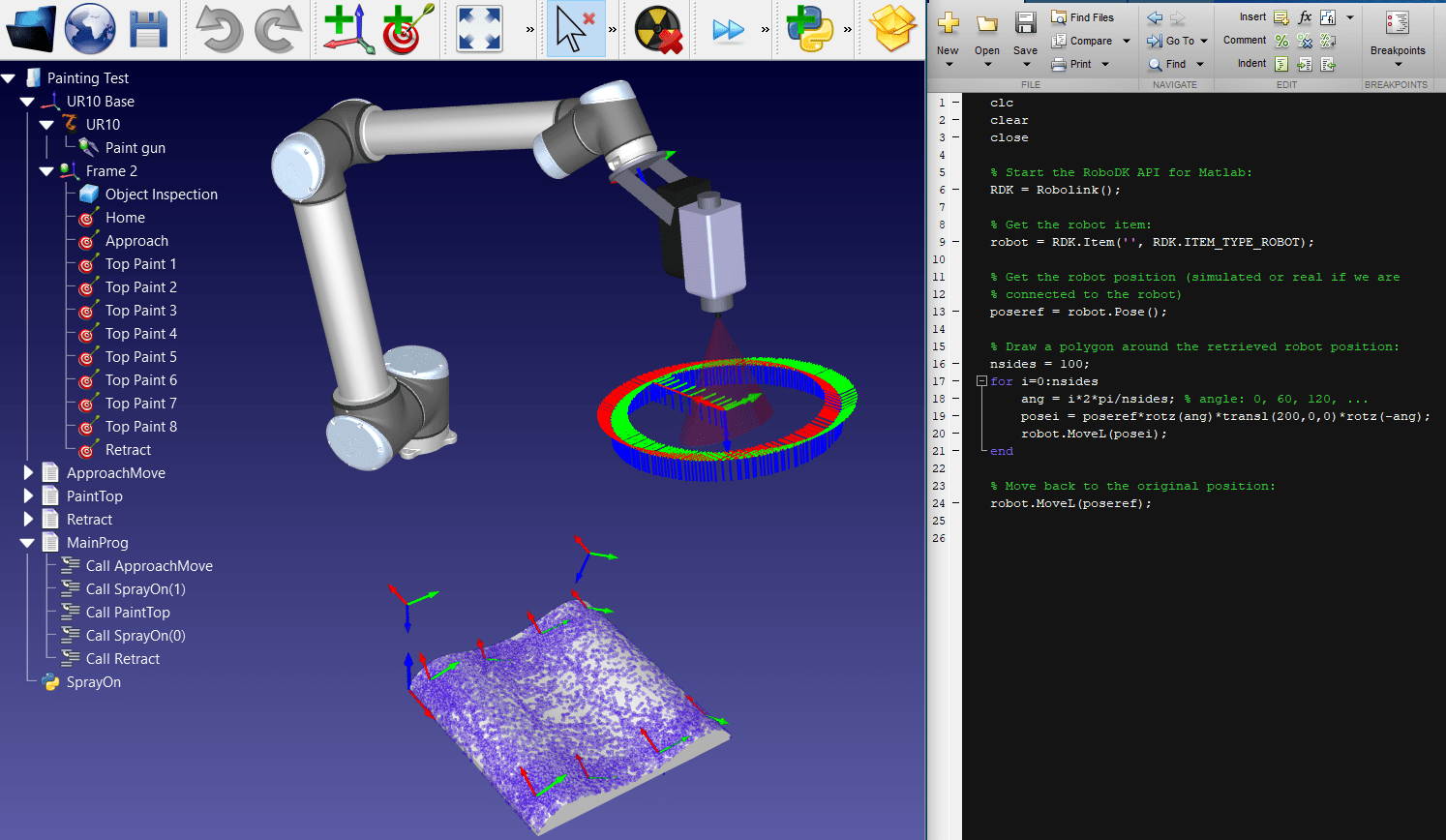
Range Extenders
Range Extenders provide the robot with an extra axis and more range. Where a cobots working area is normally only around its own axis, this can be extended with a range extender. The cobot is placed on a vertical or horizontal axis that can move in width or in height. The working area of the robot is thus considerably upgraded in height and/or width which provides more automation possibilities and higher productivity.
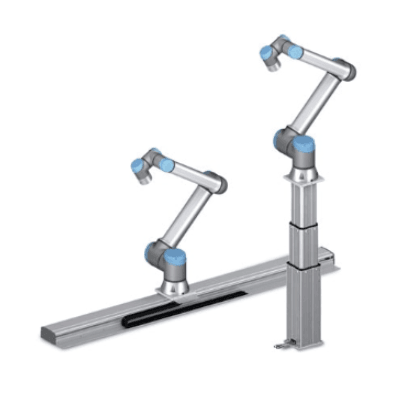
Safety
Safety includes all tools that contribute to the safety of the human-cobot collaboration. Think of sensors or screens that detect when someone gets too close to the robot.
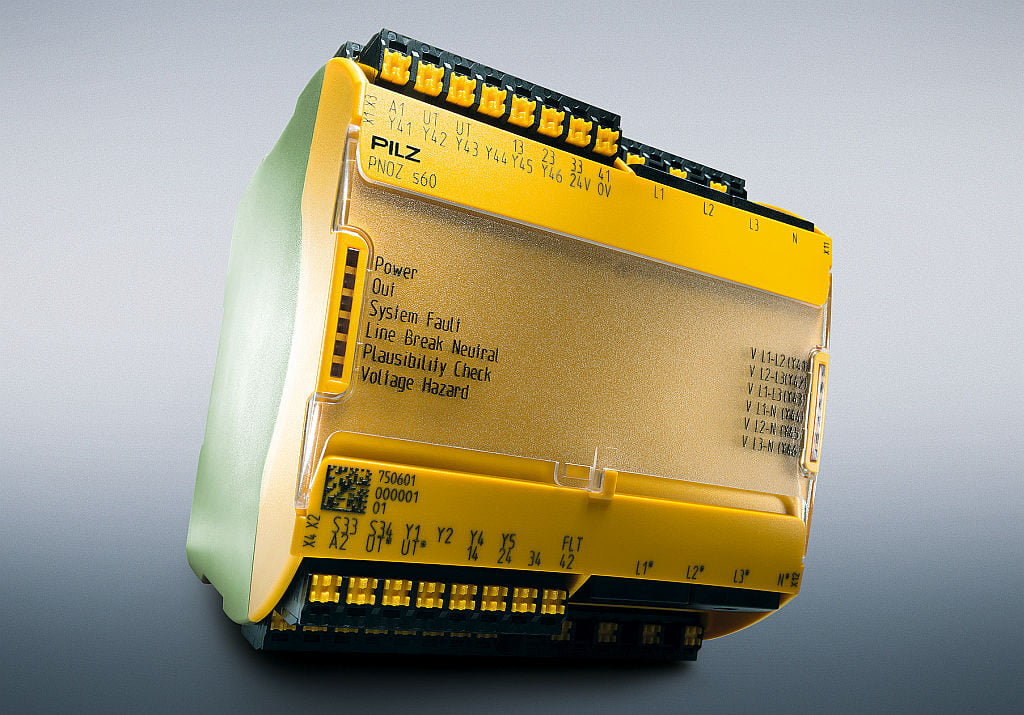
Feeding systems
Feeding systems involve machines that offer the objects to be processed to the robot. For example, a tool that always puts screws in the same place, ready for the robot (and screw machine) to pick up the screws and assemble them into the final product. But also vibrating plates that ensure that accumulated (bulk) parts are separated again so that a robot can easily pick them up.
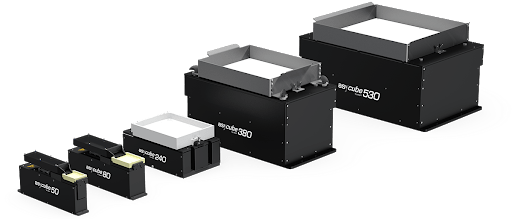