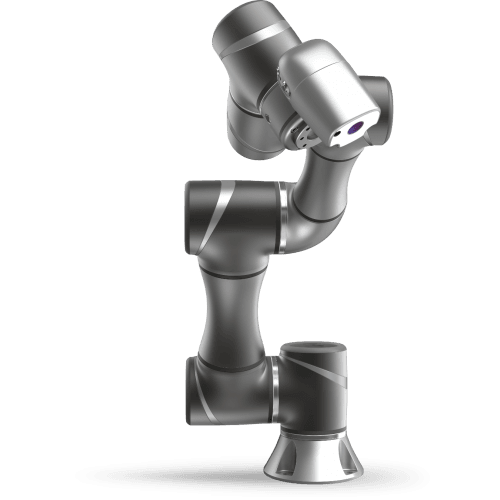
What is mechanical engineering?
The machinery industry focuses on the manufacture and maintenance of a wide range of machinery, both for commercial and private use. This sector, also known as the machinery industry or engineering industry, is an important part of heavy industry. The landscape of mechanical engineering is characterized by a diverse mix of large companies and a growing number of small businesses. These companies operate within the medium to light industry and contribute to the dynamism of this sector.
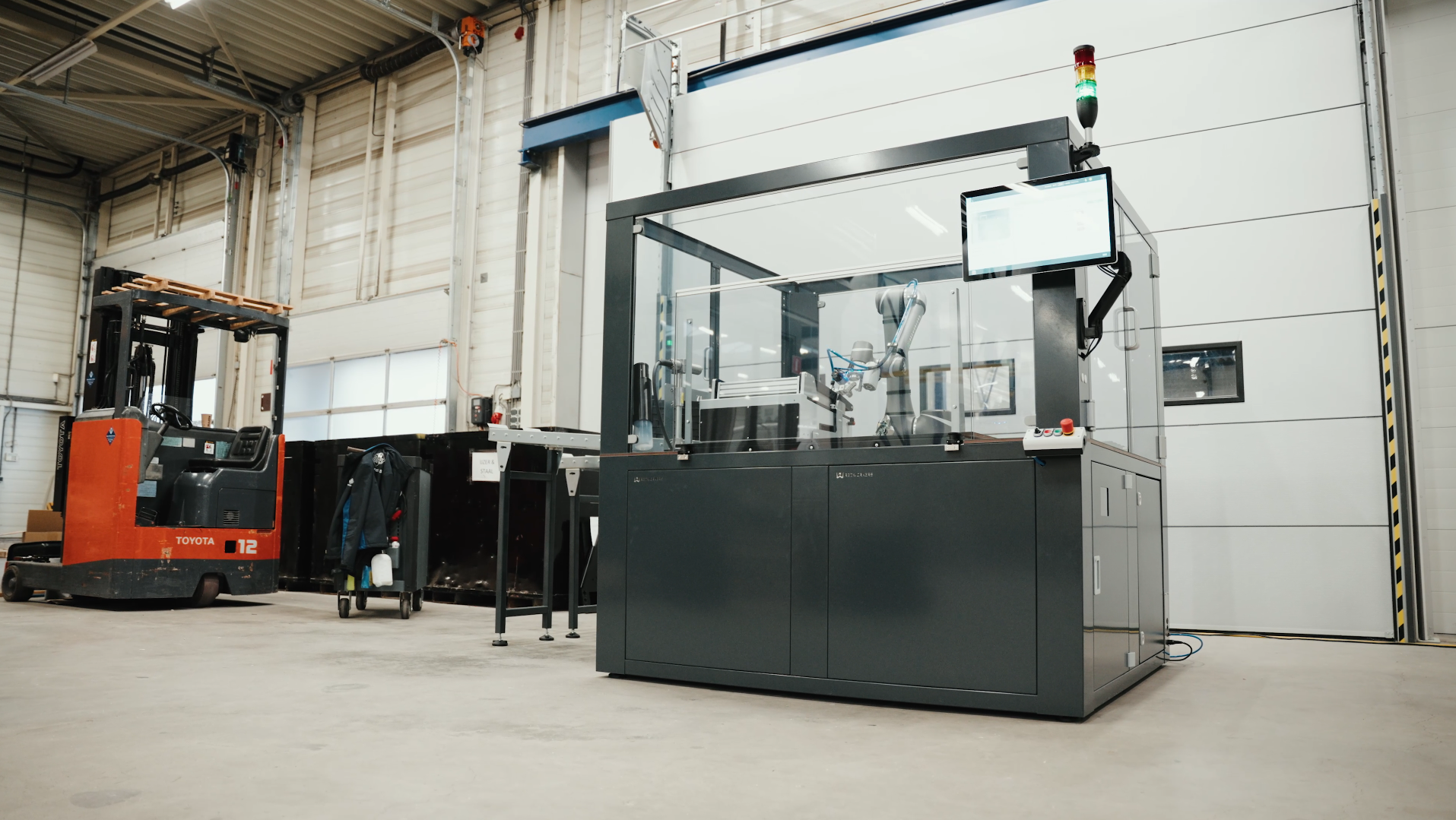
In mechanical engineering, each project begins with establishing specifications and requirements for the intended application. These specifications are then translated into a design, taking into account efficiency, reliability, safety and durability. The design process often includes testing prototypes and making modifications based on feedback.
In addition to design, the production and assembly of machines are also important aspects within mechanical engineering. Different materials are used in manufacturing, such as steel, aluminum and plastics. Assembly of the various parts is often done with automated systems and robots.
Maintenance and repair are also crucial in mechanical engineering. In addition to designing and producing new machines, many machine builders also offer maintenance and repair services for existing machines. Preventive maintenance extends the life of machines, and troubleshooting ensures that production can resume.
Innovation plays an important role in machine building. New technologies such as the Internet of Things (IoT) and Artificial Intelligence (AI) or robotics are being used to make machines smarter and more efficient, which can lead to energy savings and increased productivity.
Various types of machines
Mechanical engineering is an umbrella term for a wide variety of machines built for industry. Each type of machine has its own role within the industry in which it performs its work. From production lines to logistics operations. Below is a brief overview of different types of machinery.
Production machinery
Within the manufacturing industry, production machines take center stage. Production machines are simply machines that produce products. For example, CNC machines for producing metal parts or injection molding machines for producing plastic products.
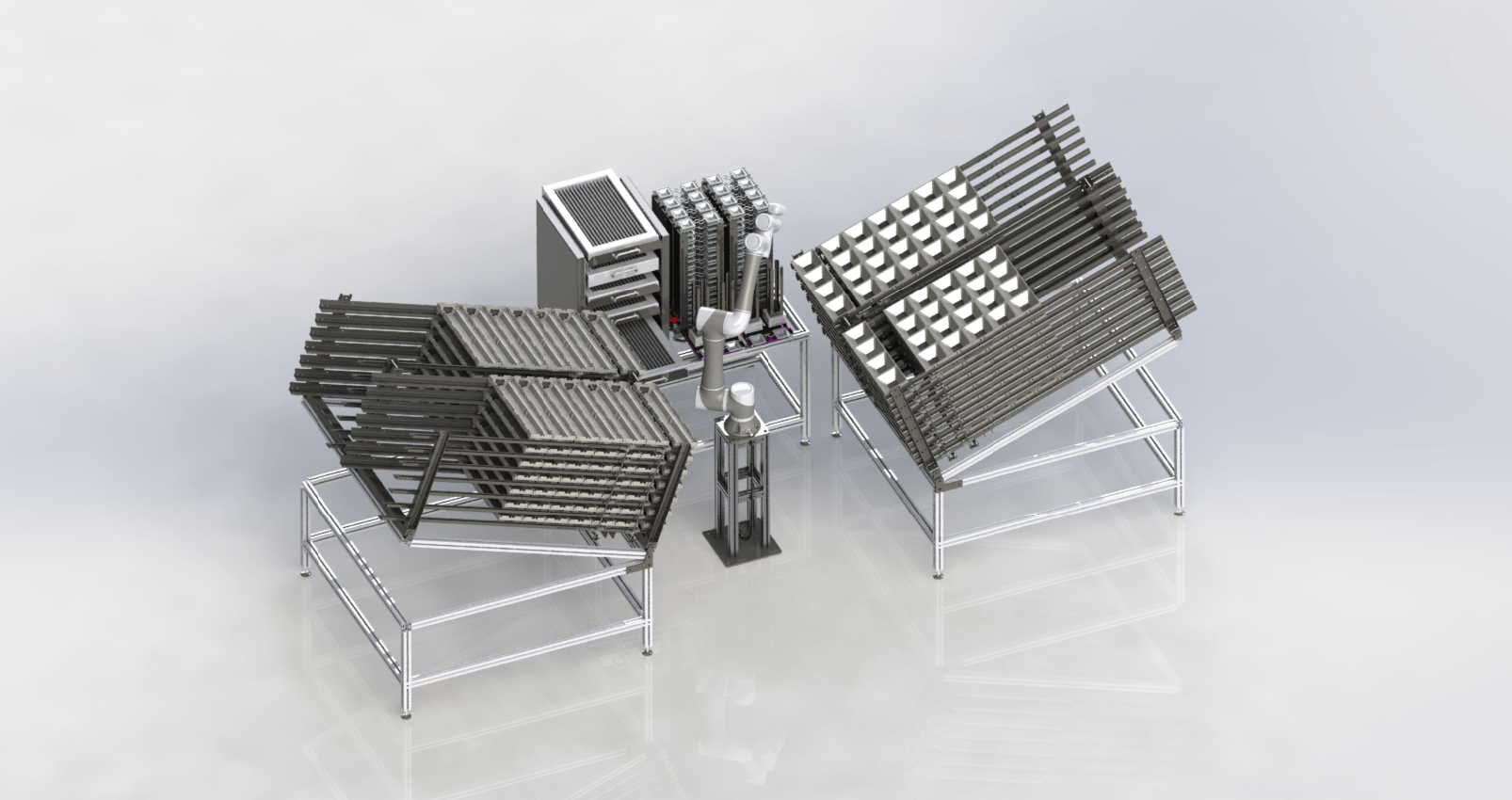
Packaging machines
Packaging machines ensure that products that have been produced are packaged. In this process, efficiency is very important. Not only to carry out the packaging process as quickly as possible, but also to waste as little packaging material as possible. Think flow packers and filling and sealing machines. Indispensable in the food, pharmaceutical and cosmetic industries, among others.
Robotics and automation machines
Within the world of mechanical engineering, robotics and automation capabilities are playing an increasing role. Many operations that are boring for workers and offer little challenge are being automated. Think of robotic arms that take over operations or palletizers. They provide precision, speed and efficiency in various applications, including assembly, packaging or quality control.
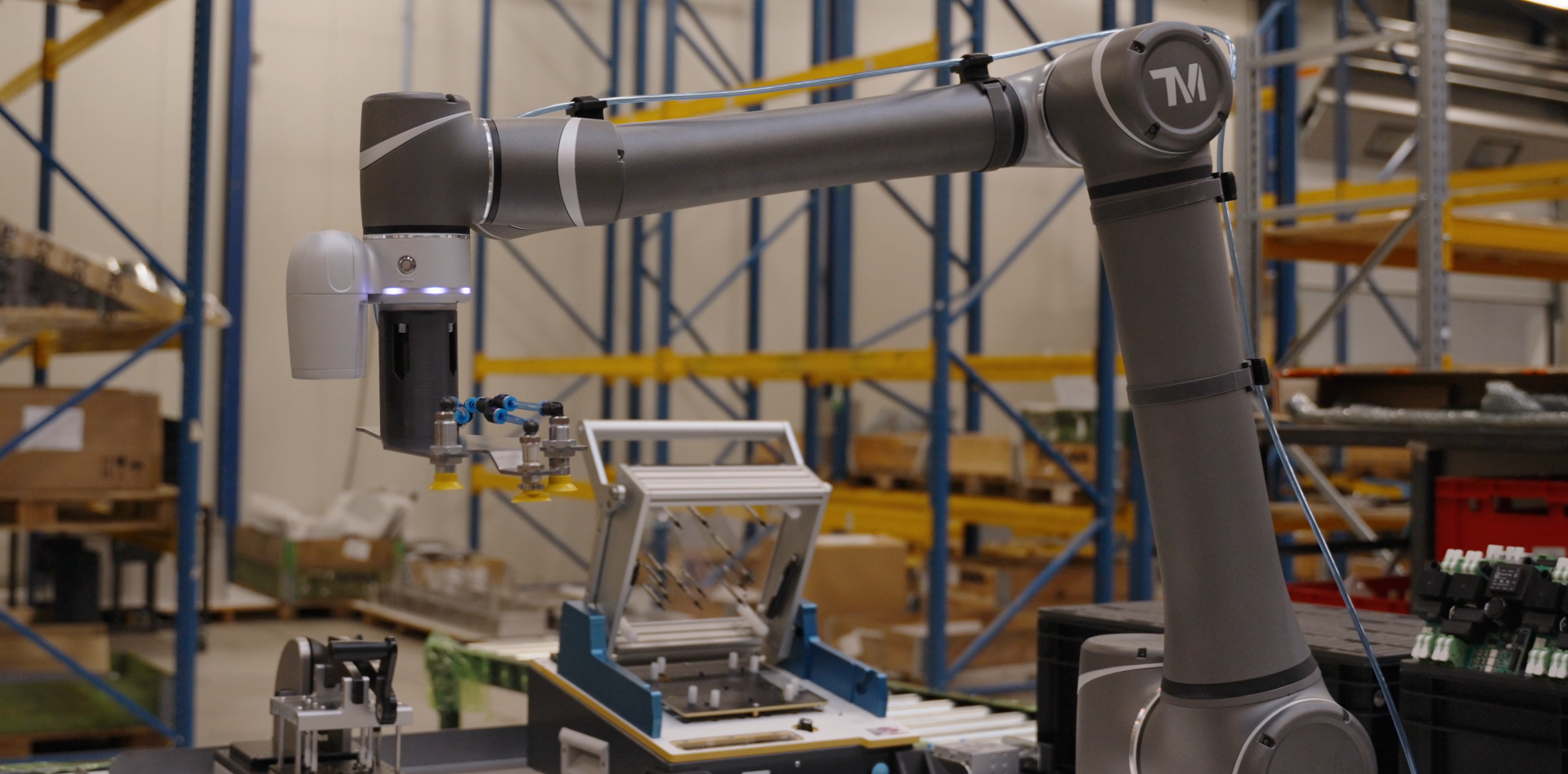
Agricultural machinery
In rural areas and agricultural regions, agricultural machinery plays a crucial role in sowing, harvesting and processing crops. From tractors to combine-harvesters, they increase productivity and efficiency in the agricultural sector.
The design process of machines
Machine design requires a structured approach and a deep understanding of user needs, the operational environment and technical requirements. The design process consists of a number of steps, each of which requires its own key considerations and tools.
Conceptual design
At the beginning of the machine building process, user needs and process objectives are identified. This identifies functional requirements, performance criteria and any budgetary constraints. At this stage, it is important to consider machine efficiency, safety and ergonomics.
Design and modeling
Computer-Aided Design (CAD) software is used to translate the conceptual design into a detailed design and model. This software allows the designer to develop 2D drawings and 3D models, which capture accurate dimensions, material choices and component positions.
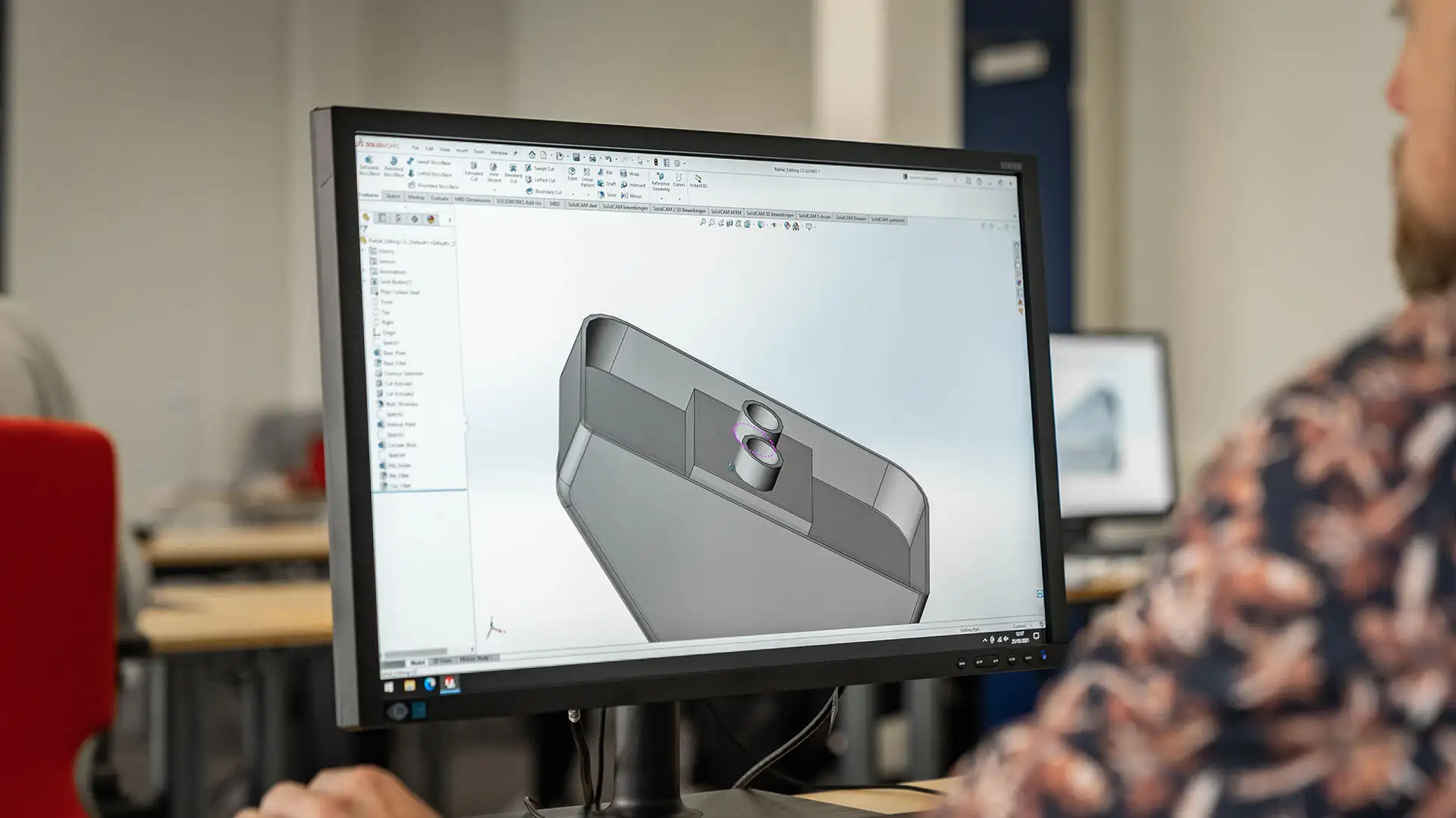
Analysis and simulation
To evaluate the reliability and performance of a machine design, analyses and simulations are performed. For example, Finite Element Analysis (FEA) for structural strengths. But also Computational Fluid Dynamics for flow behavior and kinetic simulations for motion analysis. The purpose of these simulations is to identify potential problems early and apply optimization options before the design is final.
Prototype and testing
A prototype of the machine is then built based on the established design. It is then extensively tested to validate the performance, functionality and safety of the machine. Based on the test results, some more improvements and changes can be added to the design and machine.
Completion and documentation
Finally, the defnitive design is established and documented. This includes creating a detailed technical documentation that includes assembly drawings, parts lists and user manuals. This is then transferred to the appropriate user.
The machinery design process requires not only technical expertise, but also close cooperation between designers, engineers and users to create a final product that meets the highest standards of functionality, efficiency and safety.
Commonly used materials in mechanical engineering
To build a machine that meets all requirements are a number of materials that often come back in the realization phase.
Metal
Metals such as steel, aluminum, copper and titanium are widely used because of their strength, durability and ductility. They are used for structural elements, housings and components subject to heavy loads.
Plastics
Plastics such as polypropylene, polyethylene and PVC are used because of their low weight, corrosion resistance and malleability. They are often used for enclosures, insulation materials and components with complex shapes.
Composites
Composite materials, such as carbon fiber reinforced plastics (CFRP), offer a combination of strength, stiffness and light weight. They are often used in applications where a high strength-to-weight ratio is required, such as in the aerospace and automotive industries.
Key components in mechanical engineering
To build a machine that meets all the requirements, there are a number of composites that are critical to the functioning of the machine.
Motors
Electric motors, hydraulic motors and pneumatic motors are essential drive components in machinery. They convert energy into mechanical motion to drive various mechanical systems.
Sensors
Sensors such as temperature sensors, pressure sensors and position sensors are used to measure and monitor various parameters. They play a crucial role in controlling processes and detecting malfunctions.
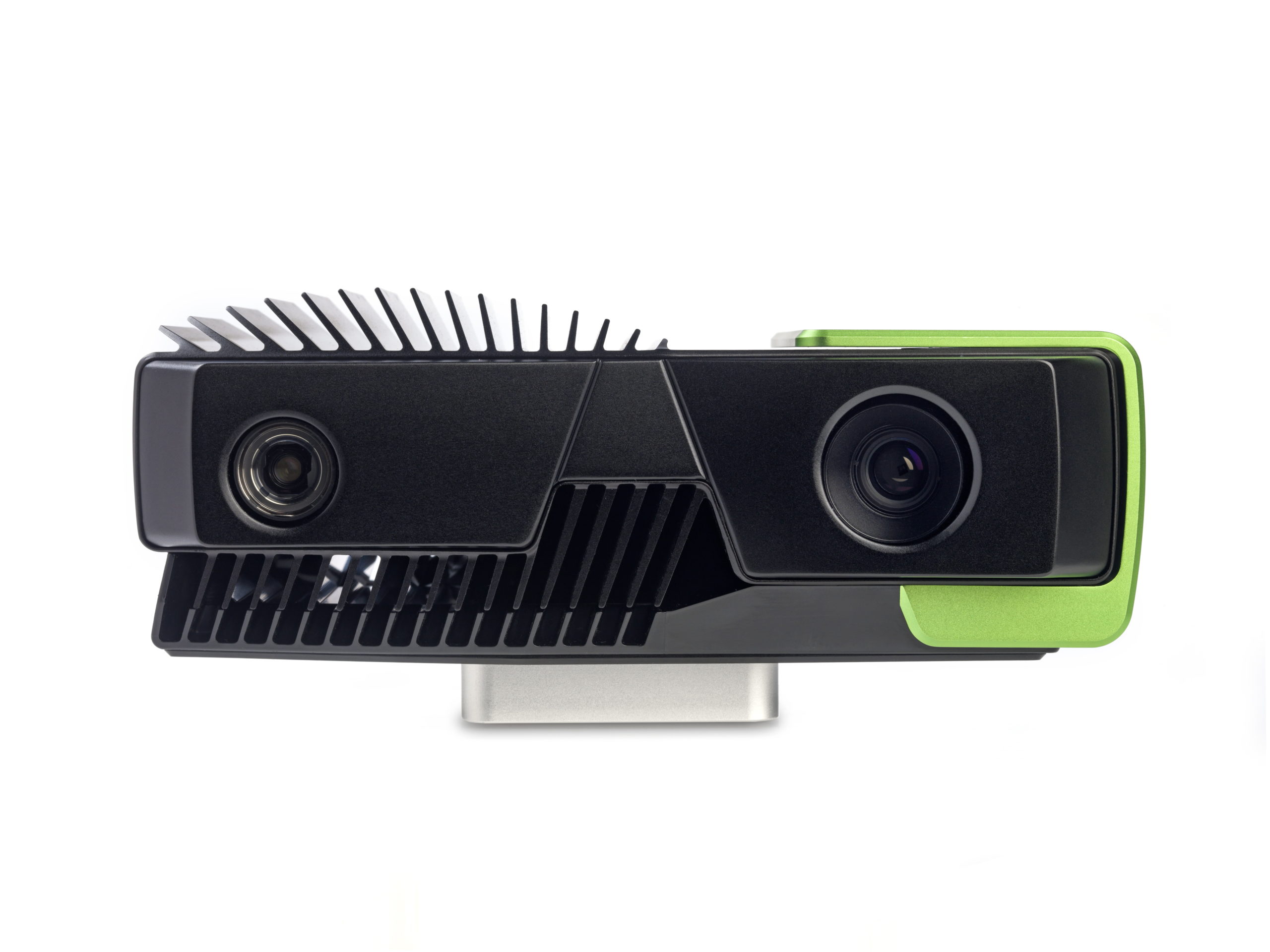
Actuators
Actuators are responsible for converting signals into mechanical motion. Electric actuators, pneumatic cylinders, and hydraulic cylinders are used to control valves, gates, and other moving parts.
Realization and assembly of machines
After designing a machine, it's time to build the machine. What is that process and what are the production methods for it?
Process of realization and assembly
Voordat men kan beginnen met het assembleren van een machine is het natuurlijk nodig om de benodigde materialen en componenten te verzamelen. Vervolgens worden de materialen en componenten gevormd tot bruikbare onderdelen met behulp van verschillende productiemethoden. Uiteindelijk vormen deze onderdelen samen de uiteindelijke machine. After assembly, the machine undergoes extensive testing and quality control to ensure that it meets the requirements and specifications.
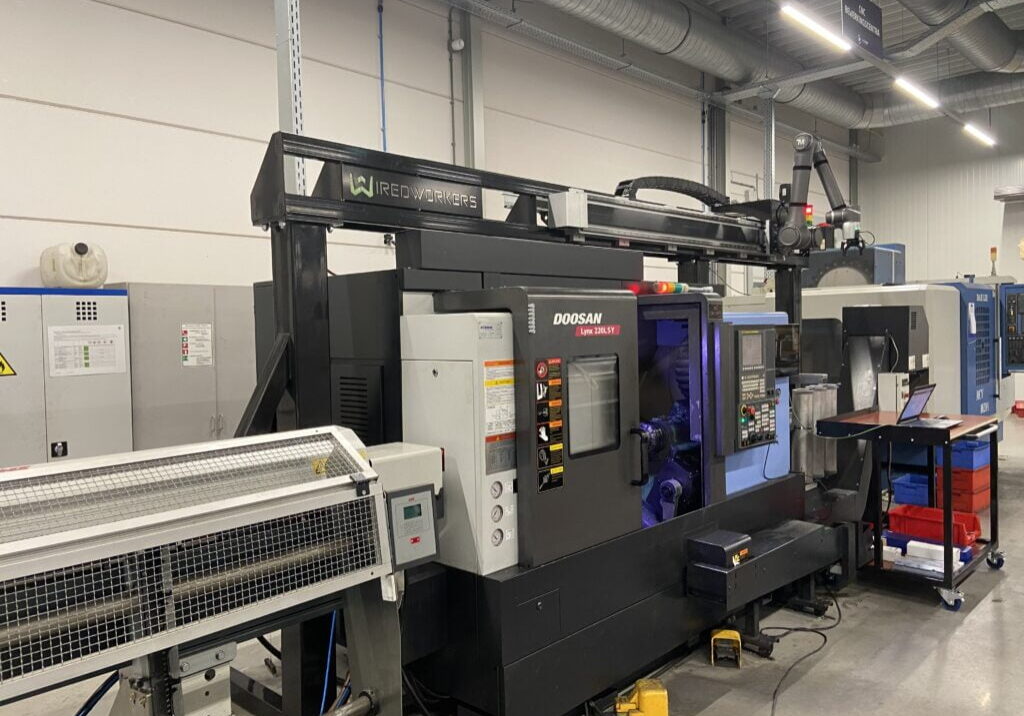
Different production methods
To develop the parts for the machine are different production methods. For example, you can choose to machine metal parts. These include turning, milling and drilling, where material is dilated to give it the desired shape. To join parts, one can choose to weld. In addition, 3D printing is a relatively new technique being used. It is increasingly being used to produce complex parts using layering of material.
Quality control and inspection during assembly
To ensure that machinery meets the specifications and standards established in the design phase, it is important to carry out quality control and inspection during machine production. For example, it is important to properly measure whether parts meet the correct dimensions, it is important to inspect surface finishes, and functional tests must be performed. Automatic inspection systems, such as vision systems and measuring equipment, are often used to ensure accurate and consistent results.
Maintenance and repairs of machinery
Importance of regular maintenance
In the world of mechanical engineering, regular maintenance is vital to ensure the optimal performance, reliability and safety of machinery. Preventive maintenance is a crucial pillar in avoiding unplanned downtime and minimizing costly repairs.
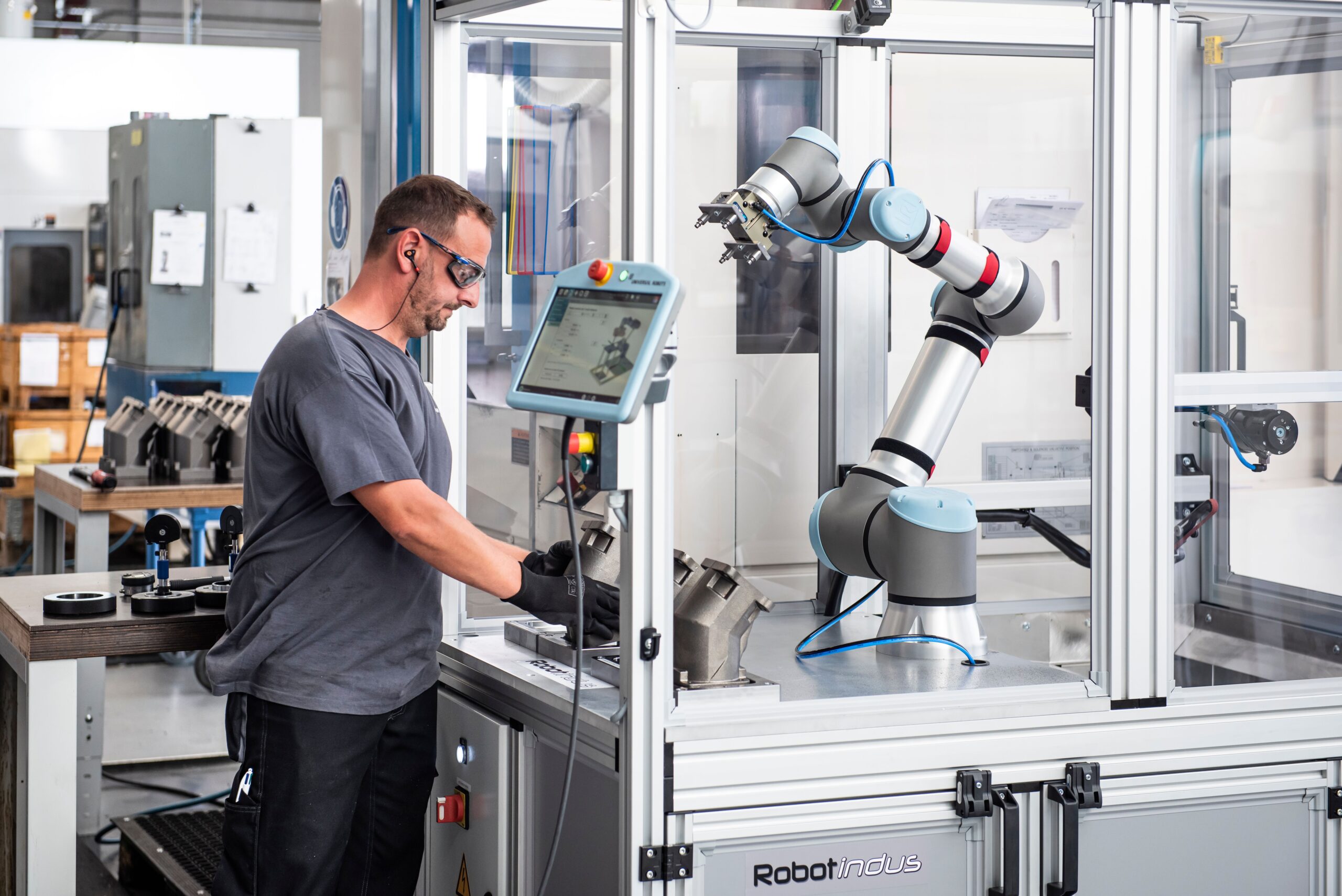
Preventive maintenance tips:
To keep machines in top condition, it is essential to perform regular visual inspections. These inspections are aimed at detecting wear, leaks and other signs of damage that could interfere with the operation of the machine. It is also important to keep the machine clean, free of dirt, dust and other contaminants that can reduce performance. Furthermore, lubrication of moving parts and timely replacement of worn parts is very important for maintaining the smooth operation of the machine. Calibrating sensors and measuring instruments ensures accurate measurements. Finally, training personnel in the proper operation and maintenance of the machine according to the manufacturer's instructions is essential to maintain optimum performance.
Diagnosis and repair of problems
When problems occur, a structured approach to diagnosis and repair is necessary. This begins with identifying the problem by listening for sounds, observing behaviors and analyzing error messages. Next, a thorough inspection is performed to locate the cause of the problem. This may include checking electrical wiring, inspecting mechanical components or performing tests. A thorough plan of action is developed for the repair, including obtaining needed spare parts and tools. The repair is carried out according to proper procedures and safety regulations. After the repair, the machine is tested to verify that the problem has been resolved and that the machine is functioning correctly.
Optimization and efficiency
By applying these methods of regular maintenance, preventive measures, and effective diagnosis and repair, companies can not only extend the life of their machines, but also improve operational efficiency and minimize unplanned downtime. This results in a production environment that performs optimally and meets the demands of a dynamic marketplace.
Technological trends in mechanical engineering
De machinebouwindustrie ondergaat een transformatie. Gedreven door een golf van technologische innovaties wordt er anders gekeken naar de manier waarop machines worden ontworpen, geproduceerd en gebruikt. One of the most notable developments is the rise of advanced automation and robotics. In modern manufacturing environments, robots are increasingly being used for tasks such as assembly, packaging and material handling. But it's not just traditional industrial robots that are stealing the show. Collaborative robots, also known as cobots, are emerging as the new stars of the factory floor. These smart machines can work safely with human operators and offer a flexible and adaptive approach to manufacturing processes.
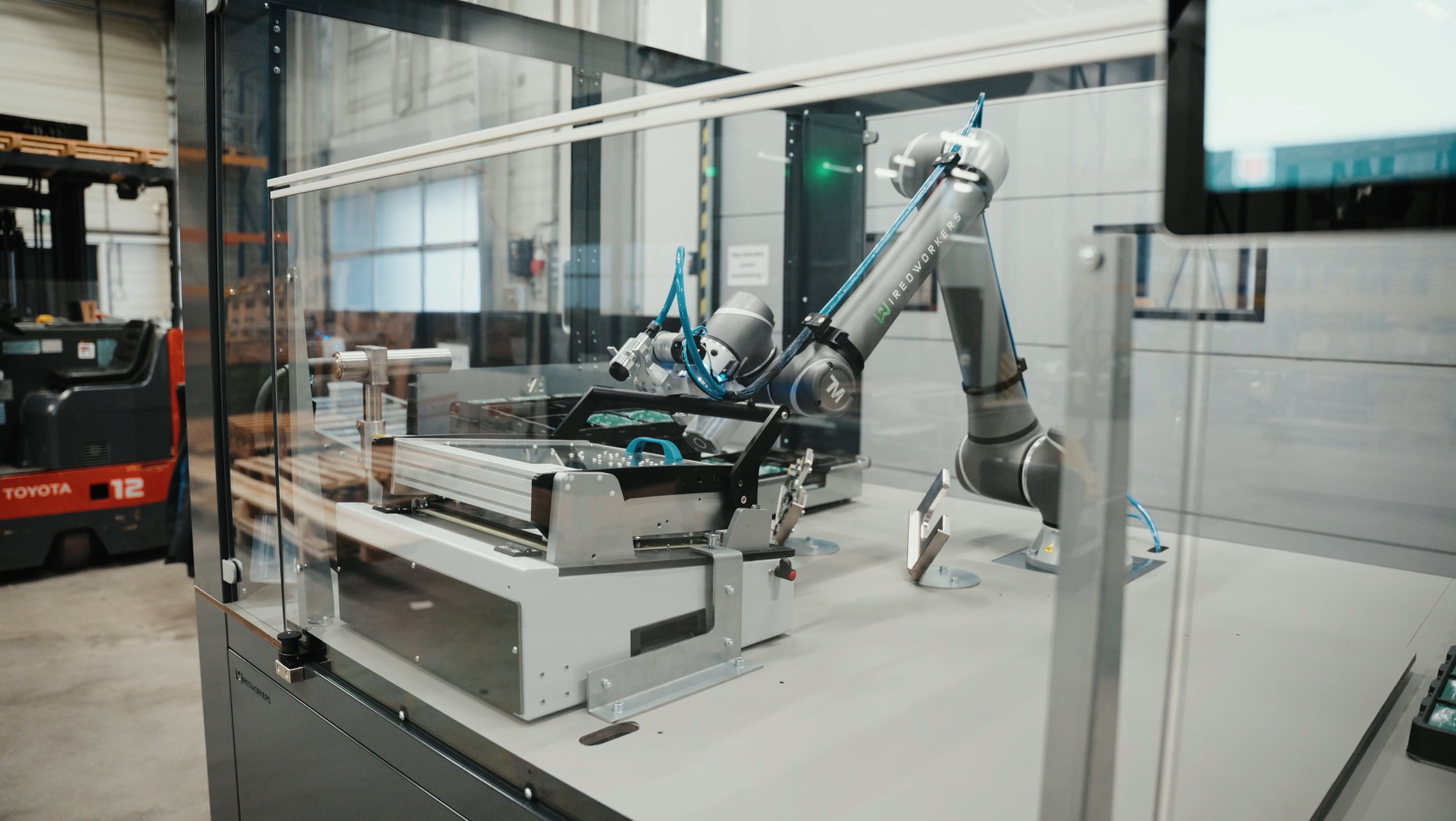
At the same time, the landscape of mechanical engineering is changing with the rise of the Internet of Things (IoT) and smart machines. With the IoT, machines are connected to the Internet, enabling them to collect, analyze and share data in real time. These smart machines offer a wealth of possibilities, from predictive maintenance to advanced monitoring and optimization of production processes. For example, sensors integrated into machines can perform predictive analytics to identify potential failures before they occur, minimizing unplanned downtime and maximizing efficiency.
Meanwhile, the digitization of manufacturing processes is transforming the mechanical engineering industry as a whole, with initiatives such as Industry 4.0 revolutionizing the way factories are managed and operated. Leveraging advanced digital technologies such as big data, cloud computing and artificial intelligence, Industry 4.0 initiatives seek to create cyber-physical systems in which machines communicate and collaborate seamlessly over the Internet. This results in autonomous production systems capable of self-driving, optimizing and anticipating changing production needs.
These technology trends promise to not only transform the mechanical engineering industry, but also reshape the broader industrial landscape, making machines smarter, more efficient and adaptive than ever before.
Sustainability & environmental friendliness
At a time when sustainability and environmental friendliness are becoming increasingly important, the mechanical engineering industry also faces the challenge of reducing its impact on the environment and making its processes more sustainable. Fortunately, there are numerous initiatives and developments contributing to a more sustainable mechanical engineering sector.
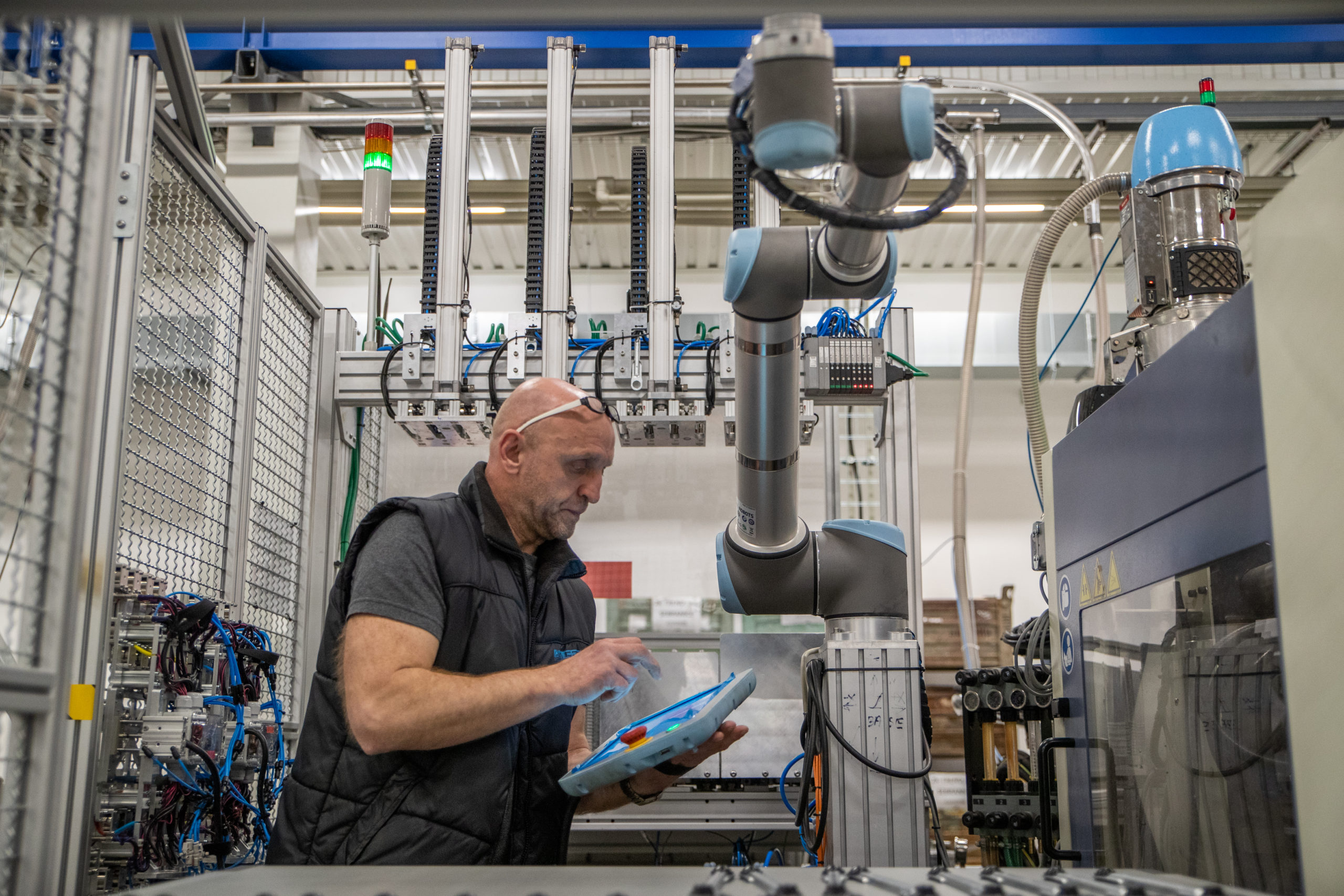
An important trend in mechanical engineering is the emergence of sustainable manufacturing and development initiatives. More and more companies are striving to make their manufacturing processes more sustainable by using renewable energy sources, minimizing waste and reducing harmful emissions. These initiatives are often supported by certification programs such as ISO 14001, which help companies implement environmental management systems.
Another aspect of sustainability in mechanical engineering is the focus on energy-efficient designs and materials. Manufacturers strive to design machines that consume less energy during operation, for example, by optimizing motors, reducing friction and using energy-efficient components. They are also seeking sustainable materials that are less harmful to the environment, such as recycled metals and biodegradable plastics.
A critical component of sustainability in mechanical engineering is waste management and recycling. Manufacturers are increasingly implementing waste prevention, waste sorting and recycling programs to reduce the amount of waste generated and recover valuable resources. This includes recycling materials such as metal, plastic and electronics, as well as reusing parts and components whenever possible.
All in all, the mechanical engineering industry is showing that sustainability and environmental friendliness are not only achievable, but essential to the long-term survival of the industry. By collaborating on sustainable manufacturing initiatives, developing energy-efficient designs and implementing effective waste management programs, machine builders can reduce their impact on the environment and contribute to a more sustainable future.
Safety and regulatory guidelines
In the machinery industry, safety is always at the forefront. Strict safety rules and regulations are in place to ensure that machinery is designed, manufactured, installed and used safely. These regulations are essential to protect workers from accidents and injuries, and to ensure the safety of machine users.
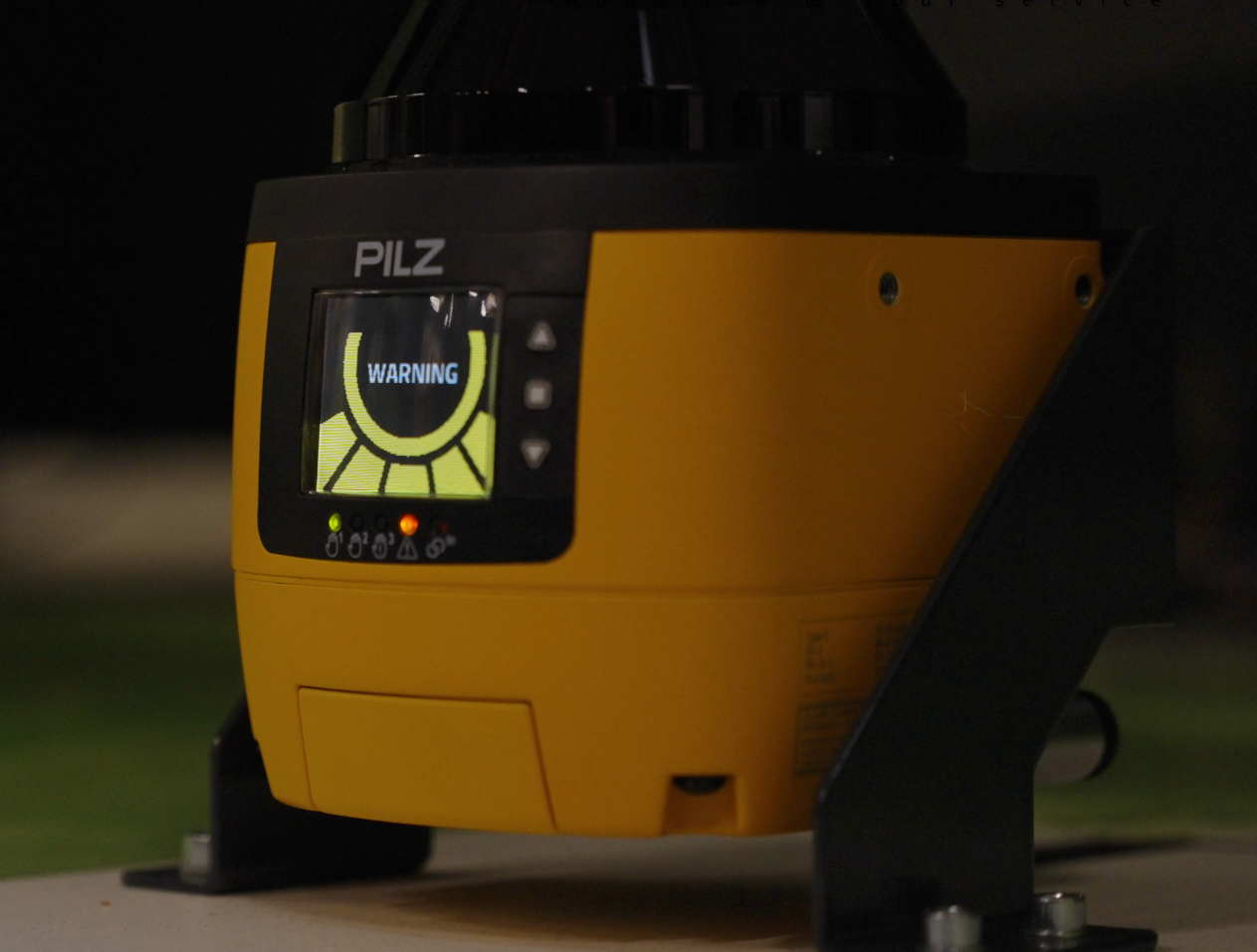
One of the most important safety regulations in mechanical engineering is the European Union's Machinery Directive. This directive sets safety requirements for machinery placed on the European market and requires manufacturers to comply with certain technical requirements and risk assessment and control procedures. In addition to the Machinery Directive, there are also national and international standards and regulations that may apply, depending on the specific industry and application.
To demonstrate that a machine complies with applicable safety standards and regulations, manufacturers must obtain certifications and declarations of conformity. For machines placed on the European market, for example, this may require CE marking, which indicates that the machine complies with all relevant EU directives. In addition, specific industries or sectors may require additional certifications, such as ISO 9001 for quality management or ISO 45001 for occupational health and safety.
Risk management and safety procedures are vital during all stages of a machine's life cycle, from manufacture to use. During manufacturing, manufacturers must conduct risk assessments and implement safety measures to identify and minimize potential hazards. During machine installation, installers must ensure that machines are properly installed and configured according to manufacturer specifications and local regulations. And during machine operation, workers should be trained in safety procedures and provided with appropriate personal protective equipment to reduce risks.
All in all, compliance with safety rules and regulations is critical in the machinery industry to ensure a safe working environment and minimize risks to workers and users. By complying with applicable standards and certifications, manufacturers can demonstrate their commitment to safety and inspire confidence among their customers and users.